Ozone truths and myths
27 Oct 2005
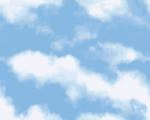
A decade or so ago, ozone generation for hygiene control was greeted with some scepticism. Improvements in technology have changed all that, as Gary Heayn explains.
Threats to public health due to the spread of disease in critical areas such as food production and healthcare are increasingly making the headlines - often putting at stake reputations, huge sums of money and even political futures.
Although the food production industry has led the way in infection control, with the establishment of strict isolation and control procedures along HACCP (Hazard Analysis and Critical Control Point) guidelines, traditional chemicals (such as chlorine-based compounds and quaternary ammonium substances) have their limitations.
Many of these chemicals form carcinogenic and teratogenic compounds that damage unborn children and it is for this reason that their use is being increasingly limited by the EU and US FDA authorities.
Another problem that is increasingly being recognised is that a significant proportion of contamination in food processing occurs via the transportation of micro-organisms through the air in a factory. Complex air filtration systems are now commonplace in food processing plants, but they are often costly and can even act as a reservoir for contamination, due to the fact that they merely trap, not kill, bacteria and moulds. Increased concerns posed by bioterrorism and diseases such as SARS illustrate the growing importance of clean (pathogen-free) air in crowded places such as tube stations, aeroplanes and even public buildings.
The good news is that there are many proven techniques, all utilising aspects of advanced oxidation processes. These use the basic forms of energy (UV and electrical energy) together with the elements oxygen and hydrogen, usually obtained from air and water. The energy transforms molecular oxygen (O2) into highly reactive, unstable, ozone (O3), which can in turn react with water to produce, via a complex series of reactions, compounds including hydroxyl-free radicals (OH*), super oxide ions (O2-), hydroperoxides (HO2) and hydrogen peroxide (H2O2). These substances are all very antimicrobial in trace (ppm) amounts and very short-lived, so they quickly break down into benign by-products after use, avoiding issues of harmful, polluting residues.
One good indicator of a compound’s biocidal activity is its oxidation (or redox) potential — for our purposes here it is basically how strongly it can oxidise the organic compounds found in micro-organisms and so kill or inactivate them.
Table 1 demonstrates that the common advanced oxidation products have amongst the highest redox potentials possible. Also these compounds work immediately on vital membrane lipids and proteins so that contact times required for ozone-based biocides can very often be measured in seconds, rather than minutes for other common disinfectants.
Table 1: Oxidising Potentials of Various Reagents
Oxidising Reagent | Oxidising Potential |
Fluorine Hydroxyl Radical Ozone Hydrogen Peroxide Permanganate Chlorine Dioxide Hypochlorous Acid Chlorine Gas Hypobromous Acid Bromine Hypoiodous Acid Hypochlorite Chlorite Iodine | 3.06 2.80 2.07 1.77 1.67 1.57 1.49 1.36 1.33 1.09 0.99 0.94 0.76 0.54 |
Natural environmental mechanisms based on UV photochemistry, electrical storms and free radical reactions have, for aeons, been preventing harmful micro-organisms and naturally produced hydrocarbons from building up in the atmosphere - this is what gives us ‘fresh air’.
Contrary to popular belief, ozone is not itself a pollutant; instead it is produced as part of a photochemical chain reaction that ultimately removes man-made pollutants from cities. High ozone concentration is just an indicator of high man-made pollution. Artificial versions of these processes based on ozone and UV have been used for many years and shown to be more effective at decontaminating and disinfecting than any other practical method; as long as sound engineering principles are utilised.
Ozone gas (O3) can be produced when oxygen (O2) is exposed to either a high voltage or to certain wavelengths of UV light. In nature, at high altitudes, UV from the sun produces the ozone layer, which protects us from damaging solar radiation. At ground level that fresh smell detectable after thunderstorms is due to ozone generated from lightening bolts. Ozone is highly reactive and unstable and quickly reverts back to oxygen.
This means it cannot be stored and must therefore be generated at the point of use; it also means that there are no harmful residues left after treatment with ozone. Above certain concentrations in the air, ozone can be harmful to humans; the recommended occupational exposure limit is 0.2ppm weighted average over a 15 minute period. It is worth noting that under certain conditions - a hot summer’s day in a city, for example - natural background ozone levels can reach in excess of 0.5ppm.
Even at very low levels in air (<0.1ppm) ozone gas will have a biocidal/biostatic effect on pathogenic and food spoilage organisms, including bacteria, viruses, moulds, yeasts and other microbes, while also removing low level organic contaminants and odours. It is soluble in water, producing solutions of ozone varying in strength typically from 0.01-5ppm.
Many domestic potable water installations have converted to ozone both in the EU and US and a large proportion of all bottled potable water is now ozonated.
As Table 2 shows, ozone is more effective at sterilising/sanitising water than any other chlorine-based disinfectant. ‘Ozonated water’ is proven to be more effective and faster acting than other sterilisers/sanitisers commonly used such as sodium hypochlorite, chlorine dioxide or peracetic acid.
Table 2: Values of Specific Coefficients of Lethality for the Main Disinfectants (mg/l-min)
Disinfectant | Enterobacteria | Viruses | Bacterial Spores | Amoebic Cysts |
03 HOCI OCI NH2CI | 500 20 0.2 0.1 | 5 1 up <0.02 0.005 | 2 0.05 <0.0005 0.001 | 0.5 0.05 0.0005 0.02 |
There is no doubt that in the 1980s and ’90s some ozone generating companies produced misleading material purporting to be scientific fact. Many primitive ozone installations were sold on this basis, leading to a bad reputation, but then diesel cars used to be slow, smoky and noisy, and aircraft were made of wood and canvas. Thanks to technology, things have improved. It is therefore essential to look at potential limitations of ozone and the innovative engineering and control systems that are now available to overcome these to create radically improved hygiene control systems.
Oxygen concentrators
Historically, generators used untreated air, which, as well as limiting the amounts of ozone produced and necessitating large installations, also led to low reliability due to corrosion problems stemming from the unwanted production of nitrous acid from nitrogen and moisture in the air. All modern installations now use ‘oxygen concentrators’ - devices that remove nitrogen and feed at least 98% pure oxygen into the generator cell. The result is very efficient, high output systems, usually only requiring a single phase 13 amp socket and minimal maintenance.
One limitation of ozone is that it is non-specific - it will act on any organic material in the water, such as organic cell debris, dirt and so on, as well as microbes - and in the process be consumed before it can do its job. Good engineering can overcome these issues, but many early attempts to utilise ozone floundered due to lack of simple engineering know-how. It is important to seek out the small number of ozone generator supply companies that actually know what they are selling.
Although low levels of ozone (below safe levels, up to 0.1ppm for example) do have a mildly biocidal effect, these levels cannot be used to achieve the sort of disinfection and sanitising required to replace conventional sanitising systems in industrial applications.
There have been incidences of devices, touted as ‘air purifiers’ being sold (typically in the US or increasingly via internet sites) that are at best ineffective, or at worst produce dangerous amounts of ozone in excess of safety limits. However, very safe, modern systems often include ozone detection apparatus and methods of capturing and removing (or quenching) any excess ozone gas to both eliminate any potential exposure and speed up the process to make it fit in with tight production schedules.
Any study of serious scientific investigation into the effects of ozone as a biocide will show that, when applied correctly at the right concentration (>5ppm), and in combination with other controllable factors such as temperature and humidity, a very effective broad spectrum, non-specific kill/inactivation of micro-organisms is readily achieved.
Hospital studies with the NHS have shown that up to 10ppm for 15-30 minutes is enough to provide up to 6 log reductions of methicillin resistant Staphylococcus aureus (the so-called MRSA super bug) on exposed surfaces. This has lead to verification of the technique by the Campden and Chorleywood Food Research Establishment as a potential method of hygiene control in food processing.
Advanced oxidation
Conventional filters in air-conditioning/heating and ventilation systems are limited in that they only collect debris that can become a breeding ground for micro-organisms. In a normal office environment this can lead to ‘sick building syndrome’ — a phenomenon that is now generally accepted as a real threat to health. In a food production environment the consequences can be even more serious.
Although we cannot use ozone directly for this application, new developments in advanced oxidation, using combinations of UV and free radical chemistry, can ‘activate’ the air by producing hydroxyl radicals which, although harmless to people, are still significantly biocidal. Such devices can either be installed directly into air circulation systems to protect the whole area, or fitted into individual rooms for specific applications.
Ozone and advanced oxidation technologies have many advantages over traditional chemical-based hygiene treatments and, if applied with thought, using sound engineering and a detailed understanding of the chemistry involved, can take industrial hygiene standards to a new level.
Gary Heayn is a management/business consultant and former managing director of Ozone Systems in Halifax