When retention is the best cure for machine downtime
14 Mar 2018
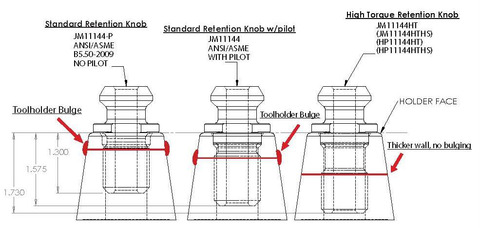
Manufacturers and distributors of computer numerical control horizontal and vertical machines and toolholders base their reputation with customers on their ability to provide quality precision equipment.
This can be undermined by lack of attention to a small and inexpensive part:the retention knob - an overlooked, yet critical component in the machining process.
Craig Gilsinger, applications/quality manager for JTEKT Toyoda Americas for more than 20 years, found that when machinists experienced vibration, chatter and fretting after purchasing equipment, they tended to blame the new spindle, toolholder or high-end carbide cutting tool.
In fact, improper seating of the toolholder due to poorly designed traditional retention knobs was a more likely cause.
Gilsinger explains that when a standard retention knob is tightened, it can produce a bulge in the taper that prevents full contact and correct seating in the spindle. As a result, the toolholder is unable to pull completely into the spindle and, subsequently, cannot make contact with up to 70% of its surface.
“A guy goes to the workbench and uses a wrench and a hammer to tighten the retention knob, and it is certainly not to the proper torque with this method. This ends up distorting the taper and so the tool does not seat in the taper correctly,” he says.
When a standard retention knob is tightened, it can produce a bulge in the taper that prevents full contact and correct seating in the spindle.
This can cause a multitude of problems, in addition to vibration and chatter: poor tolerances, non-repeatability, poor finishes, shortened tool life, excessive spindle wear and tear, run-out, and shallow depths of cuts.
Gilsinger's company found a solution to the problem in the High Torque retention knob produced by JM Performance Products (JMPP).
The High Torque retention knob is designed with a longer reach so that it threads deeper into the threaded bore of the toolholder. Consequently, all thread engagement happens in an area of the toolholder where there is a denser cross-section of material to counter deformation.
It features a precision pilot and is balanced by design, to increase rigidity. Also, in order to guard against the retention knob being over-tightened (which can still produce a bulge), JMPP provides specifically calculated torque specs based on drawbar pressure.
By combining the high torque retention knob with the proper torque, spindle contact with the taper is improved to close to 100% every time, says JMPP and this substantially reduces vibration and chatter.
JTEKT Toyoda Americas opted to recommend the product with each purchase of its machining centre, as well as on its full turnkey systems. High Torque retention knobs work with toolholders including BT, DIN, ISO, and CAT toolholders from 30 taper to 60 taper.
Dan Carlstrom of Carlstrom Associates, which sells toolholder systems, also found the high torque retention knob aided the job of boring.
“[A] customer was having a problem holding size on a component, so they had to take multiple boring passes and then do a final reaming pass to get this hole to size,” explains Carlstrom.
“When they put the high torque retention knob on the toolholder, the boring tool was able to cut the hole to size, in tolerance, in one pass.”
Carlstrom also employs the retention knob when running a test of his product, in order to eliminate poor seating in the spindle as a variable that could affect performance.