Biscuit problem crumbled
2 Jul 2012
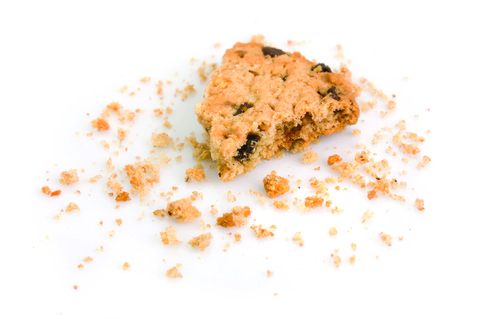
London – ?A process that defied automation has finally been brought into the 21st century by systems integrator Clint Johnson of Control Freaks Ltd.
Johnson has managed to automate a machine for producing biscuit crumbs, breakfast cereal and snack foods, replacing a labour-intensive manual process with one that provides consistent results.
“The basic process is to mix ingredients into uniform pellets and dry them,” he explains. “Sounds easy enough, but the devil is in the detail.”
Getting a consistent mix was difficult, and the liquid content needed to form pellets tended to cause the entire mix to turn into one stodgy amorphous lump.
The system includes two horizontal spiral blade mixers. These are run backwards and forwards at different speeds to achieve a thorough mix.
“There is quite an art to the speed profiles we use, each product seems to require a unique pattern of fast and slow, forward and backwards.
“We have stored those profiles as recipes on a Mitsubishi FX3U PLC, which controls a number of 15 kW E700 and D700 variable speed drives on the mixer axes over an RS485 network.”
The finished mix then flows through a series of holding hoppers and graters to form the desired pellet size. From here a dosing mechanism drops the pellets onto a conveyor and a series of levelling systems to even it out into a consistent layer before it moves into a dryer to form the final dry product.
“This was quite a complex job in itself, but there were two more related issues we had to address. The first was machine safety; operators would regularly have to access the machine for product changeovers, cleaning and maintenance. The second was that the machine had to be built as several separate subsystems then connected up without compromising operator safety.”
The solution was to define several discrete safety zones within the machine and connect them up with a control system that could determine whether to stop a single zone, several zones or the whole machine as appropriate.
“We ended up with two-hand controls, multiple emergency stop zones, interlocks on the access doors and trapped key mechanisms for assembling the various sections together,” recalls Johnson. “In all there are about 30 safety switches across the machine that all needed to be interconnected into one coherent system.”
Mitsubishi Electric recommended the use of a single WS Safety Controller, with which Control Freaks could define a multi-level control network. This was networked with the FX plus an E1163 HMI using Ethernet, so that a full record of diagnostics was logged and instantly available for analysis.
“Handling the pelletised material was difficult, but it was really the safety implications that had floored previous attempts to automate the process. The capabilities of the WS Controller made this far easier than was previously possible; we could work through the various possible safety sequences in the same way as the production processes.”