Permanent magnet AC motor redefines energy efficiency
12 Nov 2012
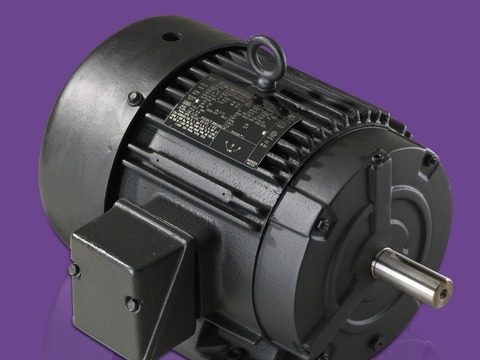
Regal is redefining electric motor efficiency with its Marathon SyMAX permanent magnet AC motors, which surpass European IE4 efficiency levels, five years ahead of their scheduled implementation.
This is achieved through the elimination of rotor conductor losses, optimised fan design, precision-wound stator and variable speed operation. Compared to motors designed to meet other high efficiency standards such as NEMA Premium, the SyMAX typically uses 30 per cent less energy, thereby producing less carbon dioxide and a significant contribution to reducing the carbon footprint of individual machines, process, manufacturing and logistics facilities.
In new applications – designed to be more energy efficient from the start, PM motors represent a big move forwards in Overall Equipment Efficiency (OEE). Converting the energy reduction into financial savings as quickly as possible is also the fundamental driver for installing these motors in existing applications; field tests show the purchase price of the motor is often recouped in two years or less.
This is especially true in high-duty applications, making them highly relevant in the MRO world. Furthermore, with energy prices set to rise continually for the foreseeable future, the savings will become ever-more significant.
SyMAX permanent magnet AC synchronous motors have a wider efficient operating range in terms of load and speed than many non-inverter driven induction motors. This increases the opportunity to operate the motor at a speed commensurate with optimum energy savings for each application, rather than having to match machine RPM to optimise motor efficiency.
The SyMAX design also offers improved speed and torque regulation, dynamic performance, and higher torque/amp, for those applications requiring maximum system performance.
Electric motors consume an estimated 25% of all the electricity generated in the world and up to 65% of all electrical energy used in industrial processes, much of which is consumed by electric motors. It is estimated that a 1% overall gain in motor energy efficiency would reduce carbon emissions by an estimated 80 million tons per year, and at 30% the wider application of PM motors could go a long way to achieving that target.
For retrofit applications, SyMAX motors are a direct drop-in replacement for Induction motors. They are configured to have identical footprint, shaft height and other critical NEMA or IEC prescribed dimensions.
Significantly the higher power density of permanent magnet motors will typically result in a 2-3 frame size reduction, while providing the same output torque. Alternatively by matching frame sizes more torque is provided to power the host equipment.
In order to maximise reliability and longevity SyMAX motors are designed with wider than traditional air gaps. Low operating temperatures, high ingress protection levels and ultra-precision balancing techniques also contribute to their reliability, while reductions in the vibration and noise profile are achieved through the elimination of die cast components.
As they are produced by one of the world’s largest electric motor manufacturers, SyMAX permanent magnet AC motors from Regal are available throughout Europe ex-stock and supported globally by the extensive Regal worldwide sales and technical support network.