New energy centre for Kodak
17 Dec 2012
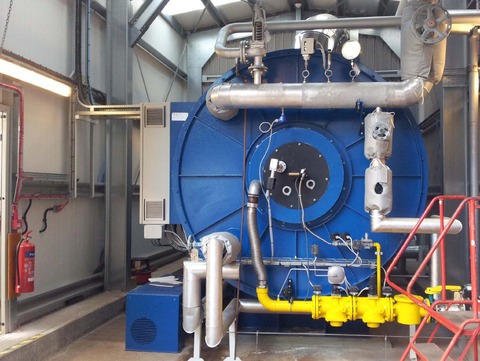
London – Kodak Ltd site in Harrow, north west London, operates a combined heat and power (CHP) plant that delivers steam to the factory producing colour negative paper for world-wide use, and to maintain building conditions, using a 50-tonne water tube boiler.
Built during the heyday of film processing, the plant is sized for a historically larger factory operating seven days a week. But with the site now operating only on weekdays, running the existing CHP plant through the weekend when demand for steam is low is both inefficient and costly.
Kodak launched a project in 2011 to look at ways of reducing its energy consumption at the weekends and other periods of low energy demand.
As a result of this study Kodak decided to install a steam generator able to supply 8000 kg/h of steam to maintain the steam service for non production needs, allowing the CHP plant to be switched off at the weekend and restarted on Sunday night in readiness for manufacturing operation on Monday morning.
As space in the existing boiler house was limited, Babcock Wanson designed a separate ‘Energy Centre’ for Kodak, based around its ESM8000 steam generator.
The coil-type generator is designed to combine high operating efficiency with low emissions – the controls maintaining a close ratio between the burner firing rate and water input with inverter drive of both the combustion air and feed water pumps.
This is said to allow tight control of both steam output and steam quality and lowest practicable consumption of both fuel and electrical power.
In addition to its operating efficiency, the ESM was chosen because of its quick Autostart facility which enables the Generator to be brought on line in a very short timeframe if steam demand fluctuates. This can be controlled remotely from the Kodak main process control centre for maximum convenience.
Construction of the new energy centre housing the ESM required careful planning due to space and access restrictions. Babcock Wanson designed a dedicated vented steel frame boiler house with a separate self supporting flue for the ESM.
The latter, said Babcock Wanson, proved particularly challenging due to the height requirements of the flue - 14 metres above the factory roof - requiring 8m deep foundations and a cruciform pile.
According to Abid Khalil, project manager, paper manufacturing operations, the system puts Kodak in position to control and monitor its steam requirements on a more precise basis and enable significant energy cost savings.
“The new plant set up has driven an estimated 18% reduction in total energy cost for the site. Reduced energy consumption is also driving a reduction in greenhouse gas emissions of NOx, CO and CO2,” said Khalil
The new Energy Centre with the ESM Steam Generator is expected offer a full payback to the company within six months.