Integration or bust
3 Sep 2014
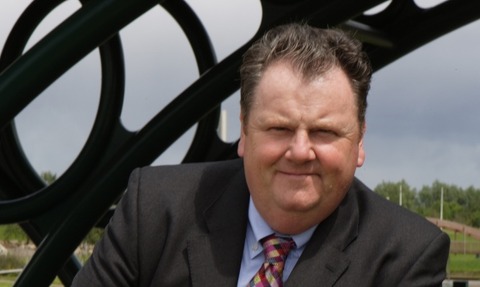
The UK’s chemical industry may be sleepwalking into further decline due to the lack of industry leadership and governmental understanding on the need for an integrated supply chain, says Stan Higgins.
Almost all of the growing locations for chemical manufacture around the world, and particularly our close competitors in Europe, are based on a fully understood model of process integration that maximises the benefits from economies of scale.
However, here in the UK studies and modelling of process integration is not being done.
This is largely because of the continued fragmentation of the UK chemical industry that began in the 1990s with the break-up of ICI and led to a subsequent lack of UK-based leadership from a flagship chemical company.
Manufacturing looks less attractive if most of the added value materials used have to be imported
We must not allow further fragmentation of the process industry and a decline in self sufficiency at previously integrated complexes such as those on Teesside, Humberside, Grangemouth and the Wirral.
To do so will result in many of our factories being decoupled from global growth drivers and result in less efficient units as more and more products and processes lose their economy of scale.
This has been the cause of the demise of many units over recent years from Ethylene Oxide, Nylon to Polypropylene and intermediates like Para-xylene.
I for one still cannot get my mind around an advanced manufacturing country operating in the 21st century without its own polypropylene manufacturer.
In globalised markets it is all too easy to import such commodity materials from large efficient factories and undermine local production prices.
Increasing free trade will ensure that logistics costs continue to fall in relation to the cost of manufacture and make importing ever more competitive.
But this will not provide local jobs and the security of supply of materials that are vital to a country with an advanced manufacturing strategy.
Nor will it help the balance of trade as the country focuses its efforts on rebuilding its manufacturing sectors.
Manufacturing of consumer goods as a strategy for national economic advancement look less and less attractive if most of the added value materials used have to be imported.
To counter global competition in materials and energy costs, manufacturers must be able to control or at least impact their costs.
The major process industry Clusters around the world and particularly in Europe are already investing in the study and modelling of how greater energy and materials integration might sustain their industries into the future.
Studies like the EU LOCIPMAP study – a benchmarking study of industrial parks - are already beginning to reveal that very significant energy savings can be achieved through factory reintegration.
Industrial symbiosis is also finding new linkages and uses for raw materials, intermediates and waste on the large scale.
This is encouraging companies to migrate production to such locations where raw material compatibilities are understood and lower costs can be achieved.
These locations all have a detailed integration model to follow, but in the UK no such modelling has been done and it is exposing our chemical industry to great risk.
As far as the UK is concerned locations such as Rotterdam and Antwerp are the locations where the industry has already created its integration plans and is providing lower cost solutions to potential investors.
The studies have been done through public and private partnerships with models and plans developed to improve infrastructure, energy supply, feedstock security, waste management, and logistics development.
Even in Denmark, a relatively small chemical manufacturing nation, such studies have determined how related industries can be integrated and materials symbiosis achieved.
If we do not proceed urgently to perform an integration study and model the integration of the major chemical manufacturing locations in the UK, revealing where and how greater energy and material efficiency can be gained, the process industry will decline here even more quickly than it has in the past.
Outcomes from such integration studies often lead to product, process, waste, heat and water efficiencies.
Performing the study and generating business plans for the opportunities identified will give the local managers of our chemical plants the ammunition they need to intervene and ensure that their units at least have the option to improve their costs and bring a more sustainable future for chemical manufacturing in the UK.
Without the data and modelling, manufacturing units will not be aware of any potential integration opportunities and they will become increasingly uncompetitive, stagnate and decline.
Such fragmented businesses have no chance of influencing and creating better outcomes effectively through the greater economies of scale that integration could bring, and that is being sought and developed elsewhere.
This is particularly true of energy supply, where integration studies in other locations are revealing new abundant energy scenarios that will enable future growth.
- Dr Stan Higgins is chief executive of the North East Process Industry Cluster.