Safe hands
7 Jan 2015
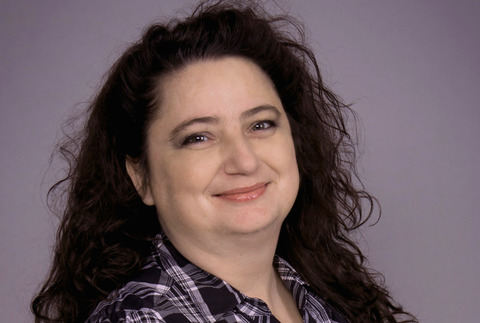
Replacing run-to-fail strategies with condition-based maintenance is an investment in health and safety, says Davina Reilly of AVT Reliability.
Carrying out maintenance in the safest possible way can do more than protect employees – it can also make plant equipment less likely to fail in the first place.
Facilities utilising condition-based maintenance (CBM) to detect and monitor potential faults and dangers are therefore also well on their way to maximising health and safety.
Ensuring work equipment is maintained in a safe state is a key requirement of the Health and Safety at Work Act 1974. But in 2012/13, the manufacturing industry accounted for almost one in five reported injuries and fatalities to employees.
If equipment is allowed to run to fail, the consequences can be sudden and may cause a catastrophic failure with very serious ramifications
The statistics compiled by the Health & Safety Executive (HSE) also revealed that 13 per cent of reported injuries were attributed to contact with moving machinery. In 2011/12, some 787,000 working days were lost to injury.
This came at considerable cost to employers and points to significant potential gains to be made by tightening up health and safety procedures. Refining health and safety guidelines must always begin with risk assessment.
Although it is often considered an activity that takes place at the outset of a project, risk assessment is in fact the cornerstone of both safe working and safe maintenance and an activity that must be constantly revisited.
All machinery is subject to change over time. Whether it is from technical modifications or atmospheric changes that affect lubrication effectiveness or energy usage, risk assessment can never really cease until the machinery is decommissioned.
And as risks evolve, so must safety procedures, maintenance schedules and practices. As well as informing safety procedures, risk assessment is an essential stage in implementing an effective CBM programme.
To this end, equipment and components are audited to determine their reliability and provide guidance as to the correct monitoring techniques and intervals. Plants implementing CBM are therefore already likely to fulfil one of the major requirements of the Provision and Use of Work Equipment Regulations 1998 (PUWER) – that equipment provided for use at work is “safe for use, maintained in a safe condition, inspected to ensure it is correctly installed, and does not subsequently deteriorate”.
Manufacturers employing reactive maintenance techniques, where equipment is allowed to run to fail, may therefore be in contravention of PUWER.
PUWER argues against run-to-fail maintenance strategies owing to the substantial risks associated with using equipment once a fault has developed.
If equipment is allowed to run to fail (when bearings explode, for example), the consequences can be sudden and may cause a catastrophic failure with very serious ramifications. Aside from the risks to the health and safety of employees and the downtime which will inevitably result, such a failure may also invalidate the warranty of the equipment.
An efficient CBM programme enables manufacturers to comply with PUWER regulations, as it allows for monitoring intervals to change according to need, for example when equipment is exposed to extremes of temperature. It is important not to rely on the original equipment manufacturers’ (OEMs) advice alone when determining monitoring intervals, as these may need to be shortened in case of intense usage or adverse environmental conditions.
Adjusting the monitoring schedule also allows faults to be detected in good time, averting potentially dangerous situations as well as maximising uptime.
Preventing the exposure of employees to risks is also a key facet of PUWER, and one that can benefit the maintenance programme as a whole.
For example, to maintain the safety of workers while carrying out essential maintenance, PUWER states that, where possible, equipment should be capable of being isolated from power sources to prevent moving parts from accidentally restarting.
It is important to remember here that while a machine as a whole may have been isolated, components inside may have their own independent power source which must also be shut off to prevent injury. When maintenance personnel work under the pressure of minimising downtime, work may be rushed or not fully completed, heightening the danger for the person undertaking maintenance, as well as future users of the machinery.
Where employees are permitted to take the proper health and safety precautions and work at a safe pace, they can be more thorough – protecting themselves as well as the equipment.
This more comprehensive maintenance approach, where symptoms or faults have been thoroughly investigated and their primary causes fixed, is far preferable to a rushed or temporary fix.
Setting standards for safety in maintenance is essential as part of a reliability-centred programme, and in order to adhere to current regulations and guidelines, safely undertaking regular condition-based maintenance is a must.
- Davina Reilly, is health, safety, environment and quality manager at AVT Reliability