Why motors break down
11 Feb 2015
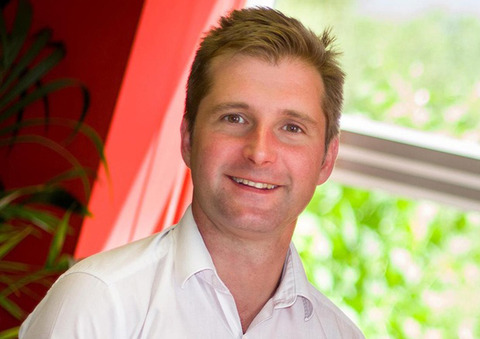
There are many reasons why electric motors fail, but some are much more common than others, says European Automation’s Jonathan Wilkins.
When it comes to electric motor failure, there is a rogue’s gallery of problems we see time and time again.
From this gallery, I have identified a set of the five usual suspects that tend to crop up more often than the rest of the villains.
Excess heat: It’s getting hot in here
Excessive heat is one of the biggest killers for electric motors; this is the granddaddy of motor issues.
In fact, the other four items on this list are often damaging precisely because they contribute to excess heat generation.
The oft-stated rule is that the life of the motor winding insulation is halved for every 10 degrees centigrade of additional heat to the windings.
Because of the excessive levels of deterioration that entails, keeping your motors running at optimum temperature is one of the best ways to extend their life.
Dust and contamination: Can’t keep them out
Particles suspended in the air will find their way into an electric motor.
That means that even some encapsulated motors are at risk here.
That’s not to say that enclosures don’t help, but it does mean that if they are not Ingress Protected to the correct standard, they won’t offer full protection as one would assume.
Once inside, the damage contamination can cause depends on the type of particle.
If they are abrasive they will wear down components, while some particles are electrically conductive and can interfere with currents across components.
Power supply: Thunderbolts and lightning, very, very frightening
Harmonic currents caused by high frequency switching and pulse width modulation can lead to voltage and current distortion, overloading and overheating.
All of these factors reduce the life of the motor and its components and increase long-term equipment costs – but that’s only one issue.
Power surges cause their own problems, as do over- and under-voltage.
In specific operating conditions, electric motors have been known to suddenly draw more current than their overall capacity.
When unpredictable events like these happen, the effects will greatly impact the motor.
To avoid an over-current surge, Variable Speed Drives should be installed that can prevent current surges from happening.
Humidity and moisture: I feel it in my bones
When a motor is unpowered for a period of time in which it begins to drop near the dew point temperature, a significant problem arises.
Electric motors should be kept warm when inactive to prevent moisture from weakening insulating materials and electrical varnish.
By themselves, moisture and humidity contribute to the decay of mechanical components, but when coupled with particles from the air they can create a deadly combination for a motor.
Certain particle contaminants can combine with moisture and create even more damaging solutions, shortening the life of motor components even further.
To reduce all risk of corrosion and weakening, relative humidity should be kept below 80% at all times.
Improper lubrication: The Goldilocks zone
The problem with correct lubrication is that it’s a balancing act that can be very difficult to achieve.
Just like Goldilocks and the three bears, there are multiple options to get it wrong and only one way to get it right.
Over-lubrication and under-lubrication both pose problems, but there can also be issues with contaminants in the grease, or the use of a lubricant not suited to the task at hand.
Consistency, viscosity, oxidation resistance and anti-wear characteristics all play a huge part in the selection of a lubricant.
If you need to mix greases, compatibility should also be considered. Incompatible greases will soften or become fluid.
Keeping your motors running at optimum temperature is one of the best ways to extend their life
In other cases, stiffening may occur and this can also lead to a lack of lubrication. Incorrect lubrication can lead to premature bearing failure.
Different motors pose different requirements for the introduction of new lubricants and removal of old lubricants.
Usually, the application will dictate the amount, type and frequency of lubrication needed.
It is worth remembering that these problems are all interlinked, so tackling only one of them won’t necessarily solve the problem.
All of them also have one thing in common; they can be avoided with correct motor usage and maintenance as well as environmental management.
When all of these five issues are minimised, electric motors can live a happy, healthy life, operating for hundreds of thousands of extra hours and ultimately, saving plant managers the same amount of time in stress. And when in doubt, ask the experts