The right chemistry
16 Jun 2015
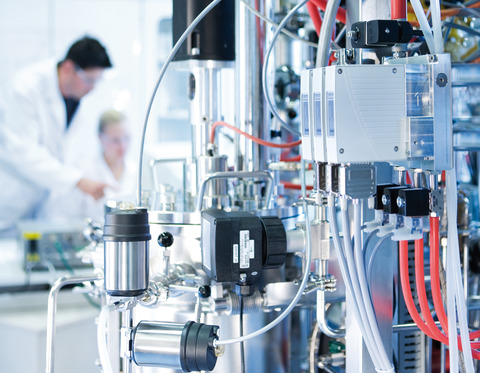
Avoiding the most common mistakes when dosing chemicals is a simple case of using the right tools.
Every industry has its share of headaches when it comes to dosing chemicals into critical processes.
Depending on the application, accuracy, pressure and corrosion are all forces that need to be reckoned with.
In the pharmaceuticals industry, the relatively small size of ingredients can be one of the most challenging factors says Keith Plumb, managing director of Integral Pharma Services.
Things that were once upon a time measured in milligrams are now measured in micrograms and nanograms
Integral Pharma Services MD Keith Plumb
Improved technologies mean active ingredients are constantly becoming more potent, which means less of them are required within products.
In the pharmaceuticals industry, Plumb says there is commonly a dedicated weighing area from which dispensed materials are taken in either bulk or small containers, depending on the process.
“The ingredients in pharmaceutical products have become more active, so most of the issues we get are between the biggest and smallest component,” says Plumb.
“Things that were once upon a time measured in milligrams are now measured in micrograms and nanograms.”
Although the issue of potency is not so critical, the problems of scale can be very much the same in processes involving cosmetics and toiletries, says Plumb.
He cites the example of a 2000kg batch of cosmetic cream which only requires a tiny amount of colour or perfume to be added.
When it comes to chemicals used in the pharmaceuticals industry, health and safety is also a serious concern.
“Dosing is one part of the process where the active ingredient could be exposed when weighing, so making use of isolator technology or glove boxes is one of the ways of working at the nanogram level,” he says.
“High containment connectors might be required to move the product from the isolator to the process to avoid any powder release.”
This, as well as energy and environmental concerns, has seen a shift towards single-use or disposable technology, he says.
“If you clean equipment, you need to use high purity water and chemicals, so there are some arguments in its favour, although the case is not yet proven.”
The issue with automating a process that deals with such small quantities can also arise, he says.
“The question is, how do you add a few grams of a solid to almost a tonne [of mixture]?”
One solution, says Plumb, is to premix the colour with an inert material to increase its volume to 50kg, which can then be dosed in automatically.
Automation of the dosing process is yet to take hold in many pharmaceutical or food and beverage plants, says Ashley Buck, coriolis product manager at Bronkhorst.
“A lot of people are currently using weight scales to perform small chemical dosing operations in these industries, which generally involves introducing the contents of a beaker into the process,” he says.
“The issue is that if you leave a drop in the beaker, that could make a difference to the process and you might get inconsistent dosing.”
Although it has traditionally been a component supplier, Buck says Bronkhorst has recently developed a new dosing unit specifically for process plants seeking a more automated dosing solution.
“We have had a few customers already using our pumps and flow meters that want to be able to dial in an amount they want to dose,” he says.
“They have asked us to supply the complete solution.”
The result is the company’s first prototype dosing box that includes a pump and a flow meter as well as the electronic components necessary to connect with a touch screen PLC.
“It has all been integrated into a compact box that can be hand carried and plumbed into a pipe, at whichever point they may need to apply a dosing application,” says Buck.
Within the new prototype, Bronkhorst is using coriolis flow meter technology as the weight scale, which provides a continuous dose, automating the process, he says.
“We are going to offer this as a standard product, but it will need to be customised for many different customer specifications.”
Bu?rkert is another company that provides dosing and dispensing systems for a range of industries, including a solution for chemical dosing and liquid product mixing by volume. A particular area of focus for the company is applications that require a high level of hygiene, says Neil Saunders, Bu?rkert’s general manager.
For chemical dosing and liquid mixing it combines diaphragm process valves and solenoid valves in a control loop with sensors, says Saunders. In combination with a Bu?rkert controller this can provide a dosing system that either runs independently, or with wider communications infrastructure, without the need for a PLC.
In the future, Saunders predicts that 3D printing may also influence the production of components for dosing, as more materials become available.
“This could well reach the point where a customer will be able to produce their own spare part in the event of requiring an especially fast repair.”
Another sector with specialist dosing requirements is the oil industry. “When crude oil comes out of the ground, it is analysed to determine the mix of additives it will need,” says Charles Wemyss, chief executive of Litre Metre.
These additives might include corrosion, scale or wax inhibitors to protect pipes, or emulsifiers to help the oil to flow.
According to Wemyss, about 30% of the cost of running a platform in the North Sea is the addition of chemicals to make the crude oil easy to handle.
“When you’ve got a tonne of [anti corrosion] liquid and then inject it into crude, if you don’t put enough in then it starts corroding the pipe,” he says.
“If you add too much corrosion protection then you have to pay to take it out at the other end, so it is worth spending the time to get it right.”
He says business has increased substantially in recent years as companies seek new ways to avoid safety breaches.
“The push for big companies is to ensure they are taking the right measures to avoid potential disaster.”
The other big driver is the increased difficulty of extracting oil. As oil companies dig deeper, the pressure becomes higher and they encounter lower flow, which can be far more challenging to dose. This demands flow metres built to work at very low flow rates in hazardous, high pressure environments, says Wemyss.
Litre Meter’s continuous chemical injection solutions are based on rotary piston positive displacement technology, and the company has recently shipped a number of flow meters to Petrobras for use in a chemical injection application for offshore production in Azerbaijan.
Here, three different sizes of VFF positive displacement flow meters were supplied for chemical injection at different flow rates to measure the flow of triethylene glycol (TEG), which is used as a hydrate inhibitor, to prevent it from solidifying as ice-like crystals that can block pipelines and valves. The water industry also has its own unique issues when it comes to chemical dosing. In this industry, peristaltic pumps are commonly used for dosing abrasive chemicals such as lime, says Paul Dale, marketing manager at pumps supplier Verder.
“Verder’s pumps are at the higher end of the market because they are targeted at pumping abrasive mediums,” says Dale.
“They are excellent for off gassing and can deal with high solid content associated with waste that other pumps can’t cope with.”
Another common chemical dosing application is within the pulp and paper industry that uses an acid called EDTA that acts as a bleaching medium and is quite corrosive. Verder has also designed hoses to deal with particular variants of acid, says Dale.