Smooth operators
1 Jul 2015
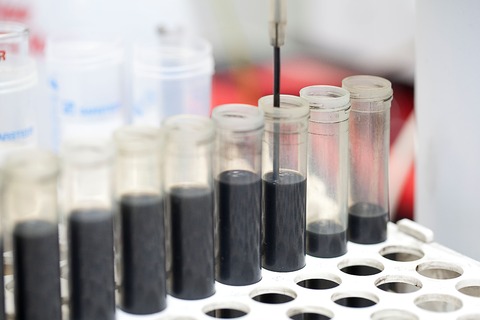
Ensuring high lubrication quality should be at top priority within almost every process plant.
Four out of five failures in rotating equipment can be traced back to lubricant degradation, which in turn is primarily caused by contamination such as particulates, moisture and heat.
So in a very real sense, the battle for improved plant reliability is really a battle against lubricant contamination, argues Rudy McCormick, marketing manager with US-based international lubrication specialist Trico Corporation.
Fluids can offer great insight into how the mechanisms are operating and what problems may lie on the horizon
Miller Oils’ Martyn Mann
What’s more, he says that battle commences before the lubricants even reach the machinery.
“Typically, lubricants are pre-contaminated due to storage and handling practices which allow infiltration of moisture and particulates,” says McCormick.
“Improper storage and handling can occur at various places such as the transportation, blending facility and distribution chain. From one end to another, the lubricant is pumped into tanks, barrels, trucks, through pipes, pumps and back again,” he says.
“If any of these areas are not flushed and cleaned properly the fluid could be cross-contaminated.”
McCormick adds that only thorough testing once the lubricant arrives on site can provide a totally effective safeguard.
Considering how critical effective lubricants are to the smooth running of almost any process plant, maintaining their quality during storage should always be a priority.
Yet lubricant storage is often an afterthought, says Martyn Mann, technical director with UK-based Millers Oils.
Mann highlights containers left exposed to the elements as a typical problem.
“If you’ve got a 45-gallon drum with a rim around the top, people think it’s sealed but that’s often far from the case,” Mann says.
“If you leave it standing around outside in the rain, water will collect on the top of the barrel. On a warm day, the air in the headspace will expand and when it cools down again at night it creates a vacuum and sucks the water in. Barrels should be kept undercover or on their sides,” he says.
New equipment is another potential source of contamination, alternative: “Closing the system and adding expansion chambers is probably a better option in these cases. [There’s] no-pressure build-up and [it’s] closed to ambient conditions [so it] kills two birds with one stone.”
Apart from particulates and moisture, the other main source of contamination is heat. High temperatures lead to a build-up of break-down products in the lubricant, changing the viscosity and pH as the oils oxidise.
“Lubricants have a finite life because they’re in contact with high-temperature components and they will oxidise over time,” Mann says.
Synthetic oils are treated to make them more heat stable than base mineral oils, but this also makes them more expensive.
“In some industrial applications the conditions mean you have to use synthetic oils, while in others you can easily get three or four times the life out of your lubricant,” says Mann.
“That’s even more important if you consider that each oil change could introduce new contaminants.”
On the other hand, synthetics can cost three or four times more than mineral oils, so oil analysis is an important tool to optimise the time between changes.
“The time intervals between lubricant changes can be maximised with the utilisation of oil analysis, which gives you a clear picture of not only what the condition of the lubricant is, but also the machinery as well,” says McCormick.
In fact, condition monitoring is a big advantage of oil testing. Millers Oils launched a new service in April offering oil analysis to help manufacturers monitor the health of their machinery. “A machinery’s fluids can offer great insight into how the mechanisms are operating and what problems may lie on the horizon,” says Mann.
“By analysing the particles and using the data gathered, we can precisely build up a picture to establish the quality of oil used and if any specific components are experiencing unusual wear,” he says.
For example, different alloys are typically used for different components, so a failing rolling element might generate traces of chromium in addition to iron, while nickel or molybdenum might indicate worn gears.
McCormick says that optimising lubricant management is about balancing the effort and expense of various contamination prevention measures against the risk of not taking action.
So while total lubrication management may be a step too far for some, everyone can afford to use a clean jug when they’re carrying out an oil change, for instance.
“A good way to look at this is rating lubrication management on a scale from one to ten, with ten being world class,” says McCormick. “Not every company needs to be a ten. Some may meet or exceed their current goals by being a five.”