Food firms take the heat
17 Jul 2015
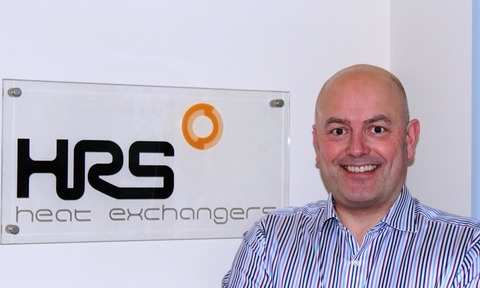
Food and drink manufacturers are investing heavily in heat exchanger technology to recover waste heat and slash energy bills, says heat exchange expert Matt Hale.
According to the Carbon Trust’s Food and Drink Processing Report 2012, the UK food and drink industry is the fourth highest industrial energy user consuming around 37TWh a year and emitting around 11 million tonnes of CO2 into the atmosphere.
Perhaps not surprisingly, heat accounts for a large proportion of this - as much as 60% according to some estimates.
This includes heating and boilers, cooking and other processes including distillation, drying, pasteurisation and concentration.
Implementing heat exchanger technology, to use waste heat from one process to fuel another, could save food factories 7.5 pence per kWh² used.
Using renewable heat sources rather than burning fossil fuels has a number of advantages.
The most obvious one is cost. Even at current low crude oil prices, the costs of electricity, fuel oil and LPG are significantly higher than biomass fuels or biogas, not to mention the cost difference with other ‘free’ sources of heat such as solar thermal and heat pump systems.
As well as immediate cost savings, which often offset the higher capital cost of a bioenergy boiler or anaerobic digestion (AD) plant, there are other benefits.
For instance, a long term analysis of wood fuel prices in the UK shows that while the price does vary, it is not subject to the same volatility as fossil fuels.
Given the availability of biomass wastes and processing by-products, the food sector has invested heavily in bioenergy projects such as biomass boilers and anaerobic digestion.
However, as a company which is focused on designing technology to recover waste heat from one process operation and use it productively for another, HRS sees many incidences where heat which is generated or used in one part of a process is lost rather than reused.
As these sources of heat are essentially free, in the right circumstances they can significantly help to reduce the energy bill of the food sector.
One of the most common situations where heat is wasted is where businesses have installed an AD plant to manage their food waste and factory by-products.
In most cases, the primary energy output is electricity supported by Feed-in-Tariffs which is used on site or exported to the grid.
The electricity is generated by a gas engine combined heat and power plant - but what happens to the heat?
In some cases it is used for processing or heating the food factory, but often not to its full potential.
Recovering the heat, using heat exchanger technology, and using it for further processes, or to improve the quality of the digestate is proving increasingly popular.
Pasteurisation of the digestate to comply with the PAS110 standard increases both the options available for its use – it is free from pathogens and can be spread on other people’s land as well as your own – and its value.
In operation, heat exchanger equipment has been shown to recover more than 50% of heat that was previously wasted.
This heat can then be used for a variety of uses such as water, space or process heating within a food plant.
One potential use of this recovered heat is to reduce the water content of the digestate, making it easier to handle and reducing transportation and storage costs.
Using an HRS Digestate Concentration System to concentrate the digestate also improves the end product quality, locking in nutrients, so that it can be sold as a biofertiliser.
Whether or not your project qualifies for support under the Renewable Heat Incentive - which for a biogas project could be worth around 7.6 pence per kWh -, with LPG prices currently anywhere between 38 and 62 pence per litre, using recovered heat without further financial support could save you 7.5 pence per kWh² used, as long as you use energy efficient heat exchanger technology.