Calibration: monitoring the vital signs
9 Feb 2016 by Louisa Hearn
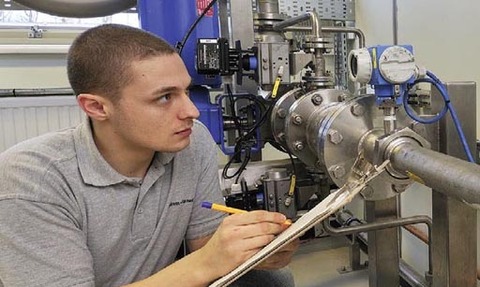
As process control instruments proliferate in the plant, operators are turning to new technologies to provide a chain of traceability against national standards.
Handheld verification devices and asset management software are just some examples of tools being deployed.
“The trend is moving toward calibration in the field. Our customers have got more and more demands on them so effectively we need to work around their requirements,” says Steven Endress, service director at Endress+Hauser.
We try to do as much out on site as back at base. It is fair to say most customers want us to be flexible to their requirements.
Steven Endress, service director at Endress+Hauser
The company provides calibration services for its own and third-party equipment tasked with monitoring flow, pressure, temperature and PH within industrial processes.
“We try to do as much out on site as back at base. It is fair to say most customers want us to be flexible to their requirements.”
According to Endress, contracts and service level agreements are also evolving as industrial needs change. “We’ve found we are adding different levels of service into our agreements.
For example providing periodic or refresher training is not unusual,” he says.
Although performing a calibration is a relatively simple task, Endress points out that the amount of information being generated by devices is steadily increasing, which means data storage has become an important consideration.
To address this, the company has developed web-enabled asset management (WAM) technology.
Another driving force is tightening compliance requirements – which means the company is becoming increasingly involved in pre-audit checks.
“The customer needs to know what assets they have, where they are, and what condition are they in,” says Endress.
“We can perform an installed base audit and then that information gets ported over to WAM. This system allows disparate parts of information to live in this system to build up a picture of how and what needs to be managed.”
There is also a trend towards ‘verification’ says Endress, owing to the increasing number of sensors being used in the field. Verification of these with a handheld instrument is often enough provide proof of their accuracy, he says.
“A lot of people get confused between calibration and verification. Handheld devices are more a verification tool,” says Endress.
Taking verification technology a step further, the company has developed ‘Heartbeat’ technology to provide diagnostics, monitoring and verification attributes within its flowmeters to ensure they are functioning correctly, independent of process and ambient conditions.
“This is the future of calibration and verification,” he says.
Full traceability
Regulatory bodies are increasingly demanding full traceability for the measurements obtained from manufacturers’ sensors, says Chris Fox, sales and marketing manager at Rotronic.
He says Rotronic is regularly asked to provide a UKAS calibration within its accredited laboratory for the temperature, humidity and dew point devices it supplies, as well as for third-party equipment.
“We have noticed an increasing requirement for multipoint calibrations covering the working range of the sensor - which is what we recommend - compared with a humidity calibration only performed at ambient [conditions],” he says.
“Many customers need us to provide a UKAS calibration certificate to enable them to use the sensor as their ‘gold standard’ reference against which other instruments are checked in situ within production, storage and other areas.”
Rotronic also provides calibration accessories so maintenance crews can perform their own UKAS calibrations. This includes the portable temperature and humidity calibrator, HygroGen2, that enables set points across wide ranges with up to six probes that can be calibrated simultaneously.
This allows sensors to be calibrated very quickly at multiple points across the working range, and then logged to an embedded PC running compliant software, says Fox.
Complex calibration requirements such as trend analysis and uncertainty calculations were once only associated with laboratory equipment, but Jake Bishop, managing director of IndySoft, says these are increasingly being requested by manufacturing plants.
IndySoft produces calibration and asset management software for laboratory or manufacturing environments that need to keep track of multiple assets. Some of these requests for more complex analyses are coming from further up the supply chain, says Bishop.
“Uncertainty calculations are a bit of a black art. Fortunately we can provide customers with a software module they can deploy to perform these,” he says.
Bishop has also witnessed an increasing demand for remote access and onsite calibration capabilities.
“Since our latest release, remote workers can use Apple or Android devices to dial in over the internet from anywhere on the planet.”
For onsite handheld calibrations, the company also supplies standalone software licenses for ruggedised devices, which can then feed data back to a central database.
“Remote access is something [our customers] may only want to do occasionally, but they appreciate the choice. It means they don’t have to go off with the files and manually enter data. This is so much more convenient, eliminates typos and speeds up data collection,” he says.
IndySoft also supplies asset management software for commercial laboratories, such as Roxspur Measurement & Control (RM&C).
RM&C says growing demand for the company’s services was not supported by its existing software.
The laboratory decided to upgrade to IndySoft’s Calibration Software for Commercial Labs. This has helped to stream-line its laboratory’s administration function, speed calibration procedures and simplify the tracking of customer’s instruments, says Mark Donnelly, RM&C calibration services manager.
RM&C says it has significantly reduced the time spent generating and issuing calibration certificates.
“We have customised our IndySoft software home page to allow quick views of equipment and process status and also developed flow charts to map processes and to better visualise work flow.
“We are now able to store unlimited numbers of records related to companies, equipment and histories,” he says.
Measured approach
In the oil & gas industry, an emphasis on environmental standards and fiscal accountability means that accurate measurement is a key driver, says Craig Marshall, project engineer at flow measurement specialist NEL.
Over the past few decades, metering technology has advanced significantly, he says. However, while flowmeters can now record and store a vast amount of data, recalibrations are still both costly and labour intensive. This is particularly so when multiple meters are involved, says Marshall.
One of the oil & gas industry’s key goals is to reduce operation downtime considerably, while saving money associated with calibrating meters, and meeting the requirements of government and regulatory bodies.
For decades in the oil & gas industry, physical witness testing has been the normal method, but it is costly as calibrations may take days to complete.
“To keep pace with technological change, and save valuable cost and time for the oil & gas industry, a more innovative calibration approach is now required,” says Marshall.
Remote witnessing is a new approach to calibrations that could be adopted to tackle this issue.
“This is where internet-based technology takes the laboratory to the world and no longer requires the world to come to the laboratory,” says Marshall.
This means that those delegated to witness calibrations would not have to be physically present.
“While this new approach has obvious benefits for business efficiency, it would have no negative impact on the accuracy or traceability of calibrations,” he says.
It could also reduce the cost associated with the length of the calibration process, and move the process from one based on predefined re-calibration intervals to one that is condition-based.
“This would reduce well operations downtime and save significant amounts of money on calibrating meters which are operating within required limits,” he says.