Age defying assets
24 Feb 2016 by Rob Smith
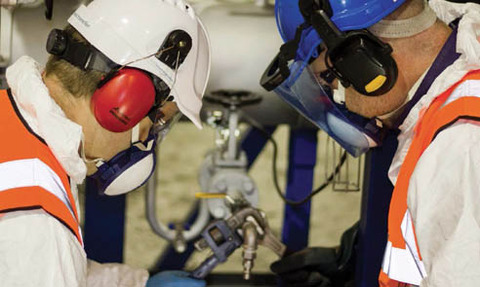
Operators need more robust strategies when maintaining ageing equipment, writes Robert Smith.
Throughout much of the engineering world, money often casts the deciding vote. However, for engineers taking care of ageing equipment, the vote rarely goes in their favour.
Such is the dilemma, a lack of investment has caused many maintenance engineers to develop a talent for ‘firefighting’ – a reactive form of maintenance that helps keep older plant running.
“Some engineers develop the ability to respond to a breakdown and get a piece of kit up and running by hook or by crook, by workarounds and by finding equipment that can be adapted,” says Phil Lawson, OGC service manager at ABB.
Lawson says it is often engineers with more experience that have the ability to care for ageing equipment.
“Engineers that have been on site for long periods of time know how the equipment runs and what the typical failure modes are. They have a very in-depth knowledge of their plant,” he says.
However, Lawson says that because of their firefighting mentality, engineers often overlook longer-term maintenance strategies, or else do not have the capacity to implement such strategies.
“Some engineers develop the ability to respond to a breakdown and get a piece of kit up and running by hook or by crook, by workarounds and by finding equipment that can be adapted
Phil Lawson, OGC service manager at ABB
“Engineers working on older kit will typically shrink into the mind-set of ‘what’s my next problem’,” Lawson says.
“Rather than repetitive problems, plants will often face problems they have not seen before and once a maintenance engineer has fixed it, he will just move on to the next one,” he adds.
Unfortunately, this approach can sometimes lead to disaster, according to Doug White, managing director of consulting engineers DC White.
“One thing I find repeatedly is that engineers forget what happened at Flixborough. Almost 30 people were killed and many more were injured because of a very simple mistake,” White says.
According to the Health & Safety Executive (HSE), the Flixborough explosion in 1974 was caused because a plant modification was conducted without a full assessment of the potential consequences.
“In the case of Flixborough, an engineer conducted a pragmatic fix but failed to look at the overall implications,” says White. “He initially got the plant up and running after a fault was detected, but it was all short-termism.”
Forward-thinking
Companies such as DC White specialise in providing services designed to promote more forward-thinking maintenance strategies, he says.
Once called in, two independent DC White engineers will typically conduct a ‘walk down’ assessment of the facility.
“Separately, the two engineers will make notes about a plant and then come together to discuss what they have found,” White says.
“The engineers will usually agree, but do not always discover the exact same issues, which makes the walk down a very good method for identifying a wider range of problems at the superficial level,” he adds.
A walk down is only the first part of what DC White offers its clients. “After the walk down, we identify further actions and access issues that we consider questionable,” White says.
“We produce a comprehensive survey and each item is described and discussed and the risks associated. We then report immediate problems and present a structured and strategic approach for the ongoing maintenance of a plant
Doug White, managing director of DC White
The company also produces a manual that demonstrates how safe a plant is, and identifies any risks and actions needed to ensure the longer-term assurance of the facility.
“We produce a comprehensive survey and each item is described and discussed and the risks associated. We then report immediate problems and present a structured and strategic approach for the ongoing maintenance of a plant,” White says.
He says a final piece of the puzzle can be offering training for maintenance crews, which teaches them to look out for certain types of issues.
“A lot of it is common sense. Often, it is just a case of reminding engineers not to overlook problems,” White says.
Equipment care
Ian Pledger, field service engineer at Schaeffler UK, says the best approach to ageing equipment care is to consider using condition monitoring technology from the time the plant is signed over from commissioning.
“That way you get an immediate fingerprint of the state of the kit – that’s your line in the sand. After that, you can monitor the machine on a regular basis and take action as and when the conditions change,” he says.
To monitor the condition of a piece of plant, Schaeffler would typically measure vibration, Pledger says.
“But you can also measure power, pressure and flow rate and monitor those on a regular basis and trend them over time and apply alarm limits to trends, which if breached will indicate to a maintenance team that they need to act,” he adds.
Unfortunately, plant operators tend not to install condition monitoring equipment on day one, Pledger says.
“In general in the UK people see condition monitoring as a luxury and they question why they need it. Often we visit customers and we give them advice and quotations but then do not hear from them for 18 months, after which time they call us back about condition monitoring because they’ve had a major breakdown, for instance.”
For those who do invest in condition monitoring, Pledger says they must also consider the resources and the training that comes with it.
“Operators buy the kit, switch it on and think the job is done. But if you haven’t got the proper resource in place or adequate training, you won’t get the full benefit of condition monitoring. It can be a false economy. People talk about condition monitoring and implementation but it has to be part of a complete maintenance strategy and part of a buy-in by senior management,” he says.
VIEWPOINT – UNMAINTAINED ASSETS
Bill Treddenick, director at engineering consultancy firm Lorien Engineering Solutions, suggests there is no real difference between “aged” equipment and “new” equipment.
“When operational or reliability issues are explained through reference to ‘ageing equipment’, the key point is being missed,” Treddenick says. “No equipment, regardless of age, will be reliable unless it is properly maintained.”
According to Treddenick, asset care is independent of age. “[It] commences with the success (or not) of the early equipment management process, and continues through having (or not having) a consistent maintenance programme based upon well-defined and appropriate tasks,” he says.
Treddenick argues that it is a fallacy to expect a new plant to operate more reliably than an older plant if the maintenance practices are fundamentally flawed.
“A new plant can quickly reach the bottom of the overall equipment effectiveness (OEE) charts, especially as the newer plant may be more automated/complex, and therefore considerably harder to ‘fix’. “The word ‘ageing’ could and should perhaps be exchanged with the word ‘unmaintained’,” he suggests.