Case study: maintenance management upgrade improves efficiency
9 Aug 2016
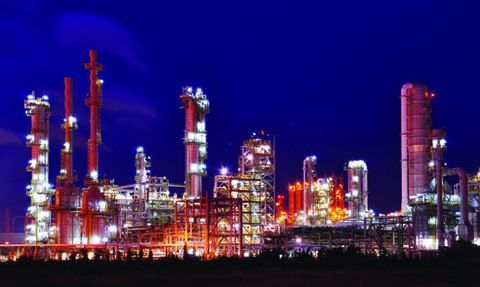
Better maintenance management methods transform efficiency levels and work behaviour at a Belgium-based specialty chemical company.
Taminco manufactures amine-based specialty chemicals for a wide range of markets including crop protection.
Prior to its acquisition by Eastman Chemical, the company was facing serious challenges delivering a consistent level of product quality.
Ongoing diversification of its product slate was part of the cause as it shifted from solid formulations to more complex liquid, multi-component ones, says Peter Van Hauwermeiren, a vice president at Hitachi Consulting.
Hitachi Consulting’s assessment of business processes at the site over a four-week period revealed four key issues: a broken performance-management structure; lack of standard ways of working; suboptimal use of asset capacity; and fire-fighting maintenance behaviour.
To overcome these problems, a 32-week programme was launched in 2013.
A new way of working
Hitachi Consulting found that product changeover represented a key area contributing to losses. To decrease changeover times, the site adopted single-minute exchange of die (SMED), which is a lean production method for reducing waste in a manufacturing process.
The issue Taminco was facing at its Ghent plant in Belgium was the need to thoroughly clean equipment before processing different materials. To achieve most rapid changeovers, Hitachi analysed online vs offline activities and where efficiency improvements were possible. To ensure all factors were considered, the company physically observed the plant floor during the changeover period, including preparation time.
It also held cross-team workshops to determine how one activity in the production line affects another in terms of time on the plant floor.
This end-to-end balancing was of significant importance in decreasing line downtime, says the company.
Maintenance mindset
Ghent changeover times fell on average 30-40%. In one line, hours reduced from 58 hours to only 18–19; in another, it decreased from 81 to 41 hours. The programme’s second work stream focused on tackling fire-fighting behaviour in the maintenance department. Hitachi says it identified improper prioritisation as the problem.
Work orders had been regularly rated ‘high priority’ because employees thought this would speed up maintenance but it led to an inability to prioritise.
This created a backlog of notifications and poor maintenance planning. In addition, the notifications frequently lacked specific detail on the maintenance necessary, prompting unnecessary back and forth between departments.
Plant staff also received guidance to help them correctly prioritise maintenance tasks and create maintenance plans
To address this, Hitachi set clear criteria for the fields that team members needed to complete, the specific type of replacement parts required and their specific location on the faulty equipment.
Plant staff also received guidance to help them correctly prioritise maintenance tasks and create maintenance plans.
The programme also tackled the siloed nature of the plant’s performance management processes by installing an efficient performance management system (Hitachi MCRS) as the backbone.
By refining existing key performance indicators (KPIs), creating new ones to build an integrated KPI ‘tree’, and discussing these at all levels in the organisation with appropriate frequency, the site achieved a significant shift in focus towards end-to-end performance.
Overall, Hitachi says the programme resulted in 20% volume/output growth. The quality of work order notifications rose to 82% from 32% and, as a result, scheduled maintenance compliance increased to 86% from 43%, it says.