Slick decisions: correct lubrication provides critical care
12 Sep 2016 by Louisa Hearn
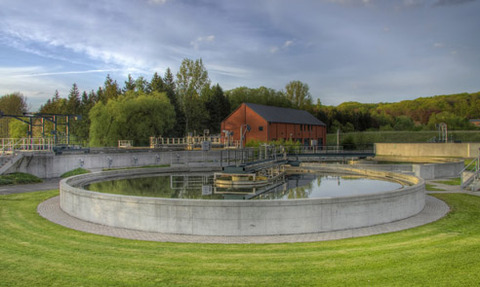
When it comes to protecting essential plant assets, small actions can have very big consequences, writes Louisa Hearn.
The maintenance crews charged with the care of plant machinery wage an unrelenting battle against the forces of friction, corrosion and contamination.
Without them, running costs could escalate out of control as unplanned downtime and replacement equipment hammer the bottom line.
Lubrication is an area of particular importance and selecting products wisely can avoid catastrophic errors, says Matt Preston, lubrication systems application engineer at SKF.
“It all comes down to the right lubrication in the right place, at the right time, and in the right quantity.”
According to Preston, about 80% of bearing failures are lubrication based. They might be caused by contaminated, incorrect or degraded lubricant that is out of date or has been stored incorrectly.
It all comes down to the right lubrication in the right place, at the right time, and in the right quantity
Matt Preston, lubrication systems at SKF
To skirt such issues, automated lubrication systems are becoming more prevalent as factories push for 24/7 operations, says Preston. He adds that more companies are wanting plant uptime increased to the 90% mark.
“Because the most common reason to shut down machinery is for basic preventative maintenance, automating lubrication can reduce the need to do this.”
SKF designs automated lubrication systems, which also reduce the manpower required to maintain equipment.
“This process involves mapping lubrication points on a machine and designing a system to supply each bearing or lubrication point with the correct amount of lubricant.”
Little and often
These machines then work on a ‘little and often’ principle so every hour or so they get a small amount of lubrication, rather than the feast or famine of previous lubrication methods, says Preston. By automating this process, it can also reduce risks to staff.
“This is because lubrication points are often deep within the machine, so fitting a system to remotely lubricate these points eliminates the need for maintenance staff to be climbing into the machine itself.”
It can also ensure the correct products are used. “The mixing of lubricant types can have disastrous effects on a machine as well as any attached lubrication system,” says Preston.
“If you put something into the system and it reacts, it can change form and jam everything up in the lubrication system. Cleaning in many cases is not cost effective, so all metering systems and pipelines would have to be replaced.”
While food companies don’t deliberately allow contamination, the incorrect lubricants are still too often used on food processing machinery, says Paul Holland sales and marketing director at Klüber Lubrication.
“Almost every piece of food processing machinery has a moving part of some type which inevitably requires lubricating in order to function correctly
Paul Holland, sales and marketing director at Klüber Lubrication
“It’s definitely not in their interest to do so, which is why facilities are monitored both internally and via external authorities…it cannot be assumed that ‘no incidental food contact’ means it’s safe to use industrial lubricants.
“Almost every piece of food processing machinery has a moving part of some type which inevitably requires lubricating in order to function correctly, thus a safer route is to ensure that only food-safe lubricants are used across all production areas,” says Holland.
The company, which makes speciality lubricants, says a small investment can make a big difference to equipment reliability, and increase equipment functionality under extreme temperatures.
It supplies a wide range of lubricants, registered as NSF H1, for the food & beverage and pharmaceutical industries. The selection of a non-toxic speciality lubricant, known as ‘food-grade’ is just the first step in the lubrication management process, says Holland.
“It is also important to look at the entire cost-benefit calculation of a given application, and price is just the tip of the iceberg.”
Clean slate
Once the correct lubricant has been selected, cleaning and replacing it at the correct intervals is yet another factor to be considered. The summer shutdown is often the only chance engineers and plant managers have to spruce up machinery, says Peter Crossen, vice president of the Maintenance for NCH Europe.
“Plant engineers approach summer shutdown on a mission to replace broken parts and upgrade systems,” he says.
“While all of this is necessary to keep production at optimum levels for the next 12 months, it is also important to take advantage of this time to clean everything thoroughly.”
This means cleaning and degreasing all machinery and parts before beginning maintenance work, to remove any grime-concealing problem areas that could result in downtime during the rest of the year. It also offers an opportunity to swap out oils and greases, says Crossen.
“However, you can’t simply throw a new lubricant into place; you need to remove all trace of the old one. For optimum performance, your new lubricant needs to be in direct contact with the part you’re protecting and cannot be contaminated with particulates that have accumulated during the year,” he says.
You can’t simply throw a new lubricant into place, you need to remove all trace of the old one
Peter Crossen, vice president of the Maintenance for NCH Europe
This is also a useful period to apply protective coatings. In the water industry, the spotlight is increasingly being turned to the ‘service life’ of systems.
This has spawned rising interest in protective coatings that will increase lifespan, says Mark Lemon, managing director of CSC Services, a specialist cleaning, repair and coating contractor to the UK water and power industries. It is also an approved installer of Polyurea protective coating technology used for waterproofing and corrosion protection.
Although more expensive than traditional coatings, Lemon says Polyurea is an extremely versatile coating.
In the power sector, it can be used to protect steel storage tanks, concrete bunds, and internal and external pipe-work.
It offers benefits to the wastewater industry, which must protect assets from the effects of hydrogen sulphide degradation caused by septic conditions during the collection and treatment of wastewater. This colourless gas forms at virtually all points of a wastewater system from interceptors to holding tanks and drying beds and is highly corrosive, says Lemon.
Fluid dynamics
Managing director of Thermal Fluid Solutions (TFS), Richard Franklin, offers tips on monitoring the condition of their thermal fluid systems:
- Regularly monitor thermal fluid: While most companies are aware that thermal fluid systems operating above the flash point of the fluid within must be maintained, many do not appreciate that organic thermal fluids based on mineral oils degrade over time. Degradation can cause a fluid’s flash point to decrease, so regular fluid sampling and analysis is required to ensure that minimum flash points are not reached.
- Use long-lasting thermal fluids: Employing a thermal fluid with a high flash point combined with chemical stability prolongs the period for which it may be safely used, making it highly cost-efficient.
- Recondition rather than replace: New reconditioning techniques can extend fluid life by a factor of at least 10, saving customers up to 70% of their thermal fluid costs.
- Employ a long-term strategy: Only a continuous risk assessment and management approach will ensure a system’s safe and efficient operation and compliance at all times. Bespoke risk assessment and management plans, and explosion protection, deliver proof of safety credentials to insurers and so reduce their premiums.
Readers' Comments
There are no comments on this article, leave a comment below to have your say
Have Your Say
The comments have closed for this article