Case study: single pipework system prevents corrosion fears
12 Sep 2016
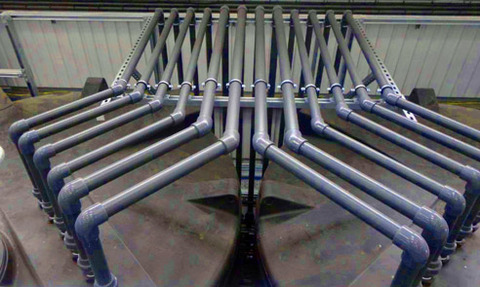
A flexible pipework system has been crucial in protecting assets from corrosion at a multi-million pound manufacturing project in Shropshire.
Bridgnorth Aluminium, a UK producer of lithographic aluminium strip, has invested more than £40 million in extending its lithosheet rolling mill and finishing line.
The investment increases the plant’s capacity to around 130,000 tonnes per year.
As part of the finishing line, a new facility was required to treat and dispose of the effluent produced during the manufacturing process.
The company needs to maintain a clean alloy system in order to create its high-purity aluminium alloy product range.
Its goal is to make clean, surface critical, highly conductive aluminium products, which it says demands a high level of technical understanding.
In the mix
Clearwater Group, specialists in separation, filtration and fluid treatment, was tasked with providing an effective effluent treatment plant for the site in Bridgnorth, Shropshire.
The new plant treats all effluent and then connects to the Severn Trent Water sewer network to dispose of the waste. A reliable pipework system was required to cater for the complex and varied pipework requirements of the plant, says Clearwater.
In seeking such a system, Clearwater turned to Durapipe UK for a single pipework system that could cater for the variety of pipelines within the plant.
The selected pipework needed to safely convey a mix of fluids, including water, treated and untreated effluent and a variety of chemicals such as sodium hydroxide and ferric chloride.
As a result, the Durapipe PVC-U, in sizes up to two inches, was specified for all pipelines within the effluent plant.
Pipe protection
The Durapipe allows the safe transportation of many acids, alkalis and chemical concentrates without fear of corrosion and environmental pollution. This makes it the ideal solution for such varied fluid requirements, Clearwater says.
Its wide operating temperature range of 0°C up to 60°C also ensured it could handle the range of substances that would be flowing through the pipework at different temperatures.
“It was important to both ourselves and the end client that the same pipework system was utilised throughout the effluent plant,” Clearwater’s site manager Keith Field says.
In addition to keeping the installation quick and simple, the use of a single system also simplifies the ongoing maintenance requirements for the end user.
It was important to both ourselves and the end client that the same pipework system was utilised throughout the effluent plant
Keith Field, Clearwater’s site manager
“With such a variety of pipelines required, we needed a product that we could rely on to convey the mix of fluids flowing through the plant and Durapipe PVC-U was the most effective solution for us,” says Field.
“The standards and approvals the product holds also reassured us that we were installing a quality product that would stand the test of time.”
The Durapipe PVC-U is backed by WRAS and Regulation 31 (DWI) approval and Clearwater says it features a simple solvent weld jointing technique to reduce significant installation time and cost savings.