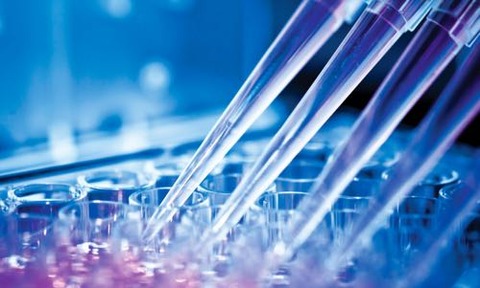
A great deal of specialist knowledge comes into play when choosing pumps for challenging pharmaceutical applications, as Michelle Knott discovers.
Many pumps in the pharmaceutical industry are quite standard, but it’s an industry that also features a range of demanding applications where some pretty specialised kit is called for. In particular, some combination of three factors tends to inform pump choice in these tricky pharmaceutical applications.
First there’s hygiene, which is probably the most obvious constraint. The need for absolute hygiene applies throughout pharmaceutical production.
Pumps designed for pharma therefore need to meet strict standards, such as 3-A or EHEDG certification. The need for hygiene in general also ties in with a related need for fast, effective product changeovers to avoid cross-contamination between batches.
The next consideration is an ability to handle very fragile media, such as living cells. That calls for extremely delicate handling in the form of low-shear pumping.
The need for hygiene in general also ties in with a related need for fast, effective product changeovers to avoid cross-contamination between batches
Third is the need for absolute precision in dosing and metering, whether that’s into the process or portioning into packaging.
These applications typically need pumps that can maintain a steady output, with little in the way of volume and pressure fluctuations – so-called pulseless flow.
As well as these three primary considerations, some applications feature hard-to-handle materials such as abrasives, corrosives or viscous fluids that might also be heat-sensitive.
All these factors can present significant challenges. No doubt there are other options available, but three pump families in particular have proved popular solutions – progressive cavity pumps, peristaltic pumps and diaphragm pumps.
All three technologies offer impressive credentials, so the choice will depend on which of the challenges loom largest in a given application.
Progressive cavity pumps
According to Lesley Eaton, business development and marketing manager with Seepex, progressive cavity pumps are good candidates for some of the most challenging applications.
“There are very few limitations in most applications. Where other pumps stop, we carry on,” she says. “Flow rates range from 200 ml/hr to 500 m3/hr, discharge pressure can be up to 48 bar as standard, and 96 bar as special design.
“Viscosity is not an issue – high-viscosity, non-flowable products are handled using open hopper pumps with auger feed if necessary.”
Progressive cavity pumps work by moving a single helical rotor eccentrically within a double helical stator (the use of an interference fit means that there is no slip).
The rotation forms a series of chambers and these move progressively through the pump. The size of the chambers remains constant throughout, so there is no compression of the pumped product.
As well as use in standard transfer and product handling duties, progressive cavity pumps have many advantages in challenging applications or where accurate dosing is necessary
Lesley Eaton, business development and marketing manager, Seepex
“Progressive cavity pumps can be used throughout the pharmaceutical process: raw materials production by fermentation, accurate dosing of materials and products to mixers, product transfer, accurate metering of finished products into pots and packaging. They are even found on the effluent treatment of liquid waste products,” says Eaton.
“Our pumps have a hygienic design when needed and can be cleaned by CIP processes. They have a low-shear, low-pulsation action. They can handle products with low and high viscosity, even those that don’t flow or are very sticky, such as molasses, pastes for toothpaste, mica, cream products, and so on. They can also handle abrasive and corrosive chemicals, such as sodium hypochlorite or phosphoric acid.
“As well as use in standard transfer and product handling duties, progressive cavity pumps have many advantages in challenging applications or where accurate dosing is necessary,” she adds.
“Pulsation is a big issue when dosing and progressive cavity pumps have the least pulsation of the more common pump types.”
End-of-line dispensing
German company ViscoTec is also promoting progressive cavity pumps – this time with a focus on filling applications at the end-of-line.
The company’s Pharma Dispenser system targets precision dosing of problematic fluids, whether they’re highly viscous or carrying high loads of abrasive solids, for example.
“As far as we know, the Pharma Dispenser [pictured above] is the first hygienic progressive cavity pump on the market for the dosing of small volumes. The principle is already established to transfer pharmaceutical products, but dosing is not common,” says Annemarie Brandstetter, who manages sales for ViscoTec’s pharmaceutical business unit.
The Pharma Dispenser can handle products with viscosities from 1 mPa up to 2,000,000 mPa without any pulsation, according to Brandstetter.
She also says that the ability of the system to accurately dose very small quantities (as little as 0.2 ml) into packaging depends on the system’s ability to deliver the amount without low-viscosity fluids dripping, or high-viscosity fluids pulling a long thread from the end of the dispensing nozzle.
“For pumps based on the endless piston principle [an alternative name for progressive cavity pumps], the path of the fluid is blocked after dosing. Thanks to the chambers inside the rotor stator system, dripping of the product is prevented. A valve inside the dosing needle or pump is therefore not necessary,” she says.
“Due to the reversible direction of rotation, the retraction can be adjusted after dosing. This function helps to obtain a completely clean cut of the thread. Volume, speed and acceleration can be individually set according to the requirement of the product. The thread is cut with precision – therefore very good and highly accurate dosing results are achieved.”
Filling speed is the other key parameter for dispensing systems, and Brandstetter says that the reversible action and accurate thread cutting of the ViscoTec system can reduce dosing duration by 50%, even when pumping against a very high back-pressure (because of high viscosity and/or a very narrow nozzle opening, for example).
Squeezing out a good performance
Peristaltic tube pumps maintain total isolation between the pumped liquid, the pump mechanism and the environment by enclosing the liquid inside an easily changed and/or sterilisable length of pharmaceutical-grade tubing. This makes peristaltic pumps a great choice for aseptic applications.
According to Matthew Thomas, senior product manager at Watson- Marlow Fluid Technology Group (WMFTG), the scalability of peristaltic pumps is a key benefit of the technology. With tubes available in a full range of sizes, pharmaceutical manufacturers can scale up from research to production without having to worry about the possible impact of changing the contact materials.
What’s more, WMFTG goes further by supplying complete fluid path containment using the same materials throughout. “Using the same high-purity, validated, contact materials throughout upstream and downstream processes enables capacity expansion with minimal input in process validation,” says Thomas.
A good example is the use of WMFTG’s Flexicon FP50 aseptic tabletop filling system at Cancer Research UK’s Biotherapeutics Development Unit (BDU). This ready-to-use, validated filling system enables the researchers to develop processes that are easily scalable if a product is later licensed for manufacture.
The latest addition to WTFTG’s range is Quantum [pictured above], which was launched in March. “It delivers high accuracy with flow linearity independent of back-pressure, removing the need for flow meters and load cells.
“Flow linearity is achieved across the 3 bar SU processing pressure range up to 20 litre/min with trace pulsation of only ±0.12 bar. That is far lower than other pumps,” suggests Thomas.
“Quantum represents a step-change in pump technology for bioprocessing by enabling higher downstream process yields throughout the pressure range, delivering virtually pulse free linear flow, lowest shear and easy validation aligned with BPOG [BioPhorum Operations Group] guidelines.”
Single-use strategy
Peristaltic pumps are ideally suited to the ‘single-use’ model, since it’s comparatively easy to switch out the tube between batches.
However, the Quantum does have a patented ReNu SU cartridge that aims to ensure that the fluid paths are perfectly aligned when they are replaced.
“The synergy between peristaltic pumps and single-use pump systems cannot be overstated. The ReNu SU technology cartridge slides effortlessly into position, allowing for a change of fluid path in minutes whilst eliminating alignment errors,” says Thomas.
Single-use is not confined to peristaltic pumps, however. For example, Quattroflow diaphragm pumps also offer a single-use version to suit the most demanding biopharma research applications. The replacement chambers are already quick to replace, but the company announced in March that they have also been upgraded to enable them to be swapped without tools. The new versions should be available this summer. Quattroflow is part of PSG Dover. “
For our smallest and medium-sized pump it takes about one to two minutes to replace a single use chamber, and about five minutes for the larger size,” says product manager Andreas Frerix.
Using the same high-purity, validated, contact materials throughout upstream and downstream processes enables capacity expansion with minimal input in process validation
Matthew Thomas, senior product manager, Watson- Marlow
“While for the Quattroflow stainless steel multi-use pumps CIP and SIP is possible, the single-use chambers are designed for the use of one batch and are then disposed [of]. The great advantage here is that efforts and costs for cleaning, sterilisation and validation do not apply and the risk of cross-contamination is eliminated. In addition, production is more flexible and requires less downtime for cleaning.”
Quattroflow pumps are quaternary diaphragm pumps, so they cycle through four flexible diaphragms as they pump, rather than the more usual one or two.
“Pulsation is one of the advantages, as the overlapping strokes from each of the four diaphragms lead to an efficient reduction of pressure and flow pulsation, which are essential for maintaining optimal process conditions of critical applications like tangential flow filtration (TFF or cross flow filtration), chromatography or virus filtration,” explains Frerix.
“Also, the four diaphragms are located in one plane, which makes the pump very compact. The quaternary diaphragm pump is driven by an electrical motor and...the flow rate is proportional to the motor speed, resulting in great flow stability and a broad flow range.”