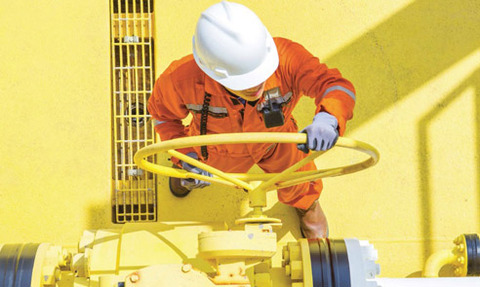
Often represented as overly traditional, the oil and gas sector and the pumps industry are driving process innovation, not following in its wake, learns Brian Attwood.
The pumps industry, like the oil and gas sector, prizes predictability and reliability – and with good reason.
In an era when profit margins are tight or fluctuating, when much of the focus is placed upon extracting value from diminishing resources and environmental concerns are on the increase, risk taking is not an attractive proposition.
Offshore especially, sustained performance of equipment may be seen as more essential than other considerations.
As the British Pump Manufacturers Association’s (BPMA) Steve Schofield has noted previously in these pages, the production impact of taking [units] out of service, for replacement or some improved energy use, outweighs any potential cost saving by such undertakings.
It would be easy to assume that this leads to entrenched conservatism; in reality, pump technology in oil and gas has played a pioneering role, provided innovation proves its worth commercially.
Oil and gas is an early adopter of industrial 3D printing, and thus realising its unique manufacturing benefits, while furthering the development of this technology to larger size capability, faster speeds, and increased material flexibility
Mike Browning, sales manager for global oil and gas OEM clients
Among the notable advances made have been those in seabed compression systems and additive manufacturing.
Norwegian company Fuglesangs Subsea’s (FSubsea) Omnirise miniBooster won the company the 2017 Offshore Technology Conference Spotlight on New Technology small business award.
Billed as the world’s first barrier fluid-free and seal-less pump intended for permanent subsea applications down to 3,000 metres, it includes a unique subsea electric variable speed drive.
The company has now teamed up with a consortium consisting of Statoil, Aker BP, Lundin, and National Oilwell Varco to develop a joint industry project to produce less expensive, more lightweight yet stronger subsea boosting pumps.
Traditional seabed compression systems can increase recovery from offshore oil and gas by up to a fifth, through boosting production streams or injecting water into side wells. Benefits are increased production rates and extended field lifetime.
However, there are challenges that impact on cost and efficiency. Conventional systems require complex topside equipment such as electric variable frequency drives and hydraulic power units.
These can add several hundred tonnes of weight of equipment. They also contain barrier fluid systems with fragile mechanical shaft seals –- which typically cause 70% of pump system failures.
Furthermore, systems rely on sensitive regulating valves and expensive hydraulic umbilical cables, often extending tens of kilometres from the host to the pump units, which increase the risk of environmental spills.
Omnirise’s all-electric boosting system involves no traditional barrier fluid and boasts embedded variable speed functionality.
“We think we’ve cracked the code,” said FSubsea CEO Alexander Fuglesang. “This project has the potential to deliver improvements in all three areas: cost, weight, and reliability.”
Key to the breakthrough was the mechanical shaft seal, the source of nearly three quarters of subsea pump failures.
Benefits boost
“Once we eliminated the single biggest problem with subsea pumps, all the other pieces fell into place,” explains Fuglesang.
Powered by patented HydroMAG drive technology, the boosting system consists of three key components: electric motor, advanced HydroMAG coupling system, plus closely integrated control and cooling.
The rotating force is created by a subsea qualified, fixed speed induction motor which rotates at low speed (3k-3.6k rpm) in order to reduce viscous losses. Rotational energy from the motor shaft is transferred to the magnetic coupling by means of fluid in a hydrodynamic torque converter.
Fluid flow from the impeller located on the motor shaft is transmitted to turbine on the magnetic coupling shaft. With the motor shaft rotating at fixed speed, the turbine can rotate from standstill up to as much as two times faster than the speed of the motor.
This reduces drag losses in the motor while still providing pump shaft speeds required to pump gas-rich hydrocarbon mixtures.
Once we eliminated the single biggest problem with subsea pumps, all the other pieces fell into place
Alexander Fuglesang, CEO, FSubsea
Magnetic coupling ensures a full hermetic separation between the motor cooling and lubrication liquids and any process fluid.
This is achieved without a mechanical shaft seal or any barrier fluid supply – enabling the use of a standard pressure compensated motor, as well as reducing costs and complexity of pressure casings and electric penetrators.
The pump cartridge employed can be either a single or multiphase pump or a gas compressor.
“Omnirise is already less expensive, more flexible, more reliable and more environmentally friendly than traditional solutions,” says Fuglesang.
Leading oil and gas consultants Rystad Energy reportedly estimated that, in Capex alone, Omnirise had the capacity to produce savings of 150 million Norwegian kroner (£137 million) on a single well-boosting installation. FSubsea claims Capex savings over conventional systems of 50%.
Benefits include minimal maintenance for unmanned platforms and low cost seabed processing. All-electric, hermetically sealed units can also remove risk of toxic leakage from hydraulic systems and umbilicals.
An additional gain is the low carbon footprint – ensuring an average equipment reduction of several hundred tonnes and using considerably less space than topside counterparts.
Additive enabled
Back in the UK, it is additive manufacturing (AM) that is making waves in the oil and gas sector.
Last September Lloyd’s Register made history when it certified the first part to be produced through AM – a titanium gateway manifold, designed for pipelines, constructed by 3T RPD for the Safer Plug Company.
Although 3D printing is the best-known variant, other techniques include additive fabrication and layered manufacturing. The SPC manifold construction relies upon powder bed fusion.
The ExOne company, now a presence in the UK pumps market but founded in the USA, has been at the forefront of 3D printing of casting media for foundry applications that are now impacting oil and gas and the pumps sector.
US-based sales manager Mike Browning (pictured), who has 20 years’ experience in foundry castings and machining of pump, valve and flow components for global oil and gas OEM clients, explains why it represents a breakthrough: “Oil and gas is an early adopter of industrial 3D printing, and thus realising its unique manufacturing benefits, while furthering the development of this technology to larger size capability, faster speeds, and increased material flexibility.”
Upstream, says Browning, demand is strong for solutions that reduce time-to-market for new or custom designed pumps, valves and flow components (impellers, valves, industrial components). Also significant is the flexibility to create new designs along with an overarching return on investment for development projects.
“Creative R&D in upstream applications is imperative to long-term growth. Rapid prototyping capabilities are vital in reducing time to market for new designs and capturing additional market share,” explains Browning.
“The 3D printed sands and casting media available in today’s 3D printers allow engineering teams to quickly go from a 3D CAD concept to physically holding a machined product in their hands and in test environments in a matter of weeks – not months.”
Oil and gas’ innovative role extends to the use of new materials too, such as 3D printing coarse carbon and graphite powders. Overall, the benefits can be succinctly demonstrated, says Browning, specifically:
- High costs of hard tooling can be drastically reduced or eliminated by as much as $10k to $100k for each design
- 3D printed moulds for castings are achieved in just a day or two, as opposed to months in a traditional pattern-making environment, drastically reducing time to market
- Technology-driven manufacturing process allows for designs previously unattainable due to constraints of a traditional patternmaking process.
In the latter case ExOne cites the example of a Tier 1 valve manufacturer that was able to reduce scrap rates for a complex casting by 80% by utilising 3D sand printers to cast the valve body in a different orientation, with core float problems and shrinkage either reduced or eliminated. Additionally, the prohibitive cost of testing multiple designs is reduced.
“During the R&D phase of upstream components such as drill bits, impellers, valves, pumps, and supporting components, 3D printed media allows engineers the ability to test multiple designs at minimal costs.
“Traditional tooling dictates long lead time and high cost to produce the tooling for each design; 3D printers allow for multiple designs to be printed, cast, and tested at a fraction of the cost and delivery time – concurrently if desired.”
Manufacturers are abandoning existing impeller core boxes in favour of 3D printed cores which maintain a tolerance of +/- .32mm, adds Browning. These exhibit significant improvement in static balancing during the machining process, while hydraulic balancing is greatly improved which reduces noise/vibration and improves flow efficiencies.
Companies with an international reach benefit too from the ability to ensure consistent quality for equipment parts.
If the same spec of pump is used at plants in Brazil, India and the UK, explains Browning, it is likely the casting for each individual pump will have been poured in the country where it is employed.
The right casting
Frequently the pattern in each location is machined slightly differently, with varying tolerances, and may be even possibly damaged or in certain stages of decay.
Original equipment manufacturers (OEMs) can seek foundries with 3D printers, emailing a mould design to each supplier who prints the exact same sand-mould in all locations. Result: consistent product lines incorporating up to date design revisions.
Downstream, the impact is being realised also, in terms of reverse engineering of product, says ExOne.
Browning outlines: “Turn-around on replacement PVF components are vital to petrochemical plant operations. In addition to rapidly casting replacement parts, clients are able to offer improved performances by optimising legacy designs affordably.
“Traditionally, patterns for replacement castings are stored in a warehouse, consuming space and valuable resources. With 3D printing, storage is eliminated. If the same component is required, digital files are re-printed on the 3D printers and cast. The result is unheard-of delivery times for legacy parts with no patterns.”
Pipe dream
KSB pumps bring environmental benefit for Oman
KSB pumps have enabled Oman to eliminate the use of ship and truck to transport product from the Mina Al Fahal and Suhar refineries to storage facilities in the capital Muscat.
A total of 39 API type OH2, VS1 and VS4 pumps, supplied with cast steel casings and their shafts made of forced alloy steel, operate the country’s first two-way pipeline, extending 280 kilometres to the Jifnain and Muscat International Airport storage facilities.
The installation has significantly reduced traffic and shipping transports of liquid petrochemical products with a benefit to the environment, says the company, particularly in Muscat which houses one in every three of the country’s 4.5 million people.