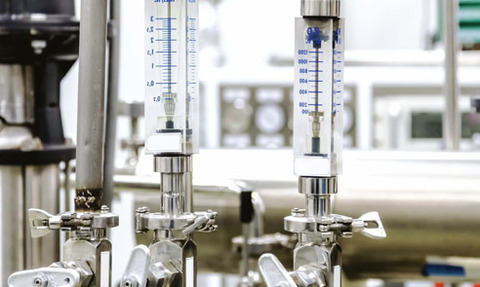
With an eye on the World Cup, The Pump Company’s Peter Staddon returns with his own selection advice on choosing pumps for chemical applications but first offers some calming tips for those worried by how current events will impact trading.
The UK chemical industry is extremely diverse and ranges from the manufacture of bulk chemicals, speciality chemicals, polymers (plastics) and consumer chemicals (eg personal care and cleaning products).
More than 97% of this sector comprise approximately 2,500 SMEs (each employing less than 250 people).
Production is concentrated into four main clusters – Hull, Teesside, Runcorn and Grangemouth accounting for 49% of sector employment, although the other 52% are spread throughout the UK.
In an industry that employs around 500,000 people (directly and indirectly), and with a turnover of £32 billion, it has total exports of £26bn of which 59% (£15bn) goes to the EU.
However, the chemical industry also imports £25bn of which 72% (£18bn) comes from the EU.
Therefore, with materials moving back and forth across the channel numerous times it’s no surprise that the industry would prefer not to have tariffs imposed upon them at each border.
Back in March, the Chemical Industries Association chief executive Steve Elliott called upon the government to abandon its ‘wait and see’ approach to Brexit and provide clarity for the chemical industry and in fact industry in the UK as a whole.
Last month we heard that the economy grew at its slowest pace for five years in the first quarter of 2018 and the Office for National Statistics confirmed its estimate that GDP growth slowed to 0.1% in the three months to March.
On the other hand, the Bank of England has argued that the slowdown is a weather-related blip and although wages appear to be outpacing inflation, the worst may soon be over as the Brexit clouds begin to clear.
So, while all this is going on it’s no surprise that the sector is being cautious with investment, or is it?
Pumps placed on the market within the EU are currently required to meet certain safety, environmental and energy-related directives and regulations and that won’t change after Brexit
In the speciality chemicals sector, we have not noticed a slowdown in spending on pumps due to the continual upgrading of plant and equipment and new projects are still going ahead.
Pumps placed on the market within the EU are currently required to meet certain safety, environmental and energy-related directives and regulations and that won’t change after Brexit.
Similarly, out of the 18,403 substances registered within Reach (Registration, Evaluation, Authorisation and Restriction of Chemicals) 6,625 are registered in the United Kingdom.
However, like so much of the preparation for Brexit, there’s no doubt that the bigger companies with large legal teams and advisors are better placed to plan.
Jim Ratcliffe the billionaire owner of Ineos recently named the richest man in the UK and a fan of Brexit, was quoted as saying: “We had always said we would make things work either in or out of the EU. We are not going to win everything, but we should win the important points because we have some very good cards in my view.”
So, what is the correct formula? I guess we’ll have to wait and see. In the meantime, the best approach is to ensure the tools we have are the most appropriate for whatever is the working environment. With that in mind, let’s now consider pumps for chemical applications…
- Peter Staddon [pictured above] is managing director of The Pump Company
A question of application
Whatever the arena, it’s all about making the right selection
The application and use of chemical pumps can be found across all industries where chemicals are manufactured, used or disposed of.
General industry uses 45% of all chemical pumps, with 21% found in the oil and gas industry, but chemical pumps can be found anywhere, and they come in all shapes and sizes.
Selecting the right pump for the job is not as simple as it first appears, just like a winning team.
The design and construction of these pumps must withstand substances that can be viscous, volatile, corrosive or aggressive. Materials of construction range from various grades of stainless steel, hastelloy, monel, titanium and exotic alloys through to plastics such as PVDF, polypropylene, ETFE, PVC or composites.
The largest and most frequently used chemical pump is the centrifugal, this is due to its simplicity of design and operation together with its relatively low cost.
This range of pumps has one or more impellers that vary in profile, the most common being the centrifugal impeller, but there are many applications that utilise mixed, radial or axial flow impellers.
Centrifugal pumps generally are used for medium flow rate and head and as a rule of thumb the thicker/wider the vanes of the impeller the greater the flow, and the larger the diameter the higher the head/pressure that can be generated.
Within the centrifugal pump there are three basic impeller designs: closed, semi open and open.
Closed impellers have the vanes sandwiched between two solid plates. The liquid enters at the eye of the impeller and travels from the centre to the outside between the plates. This type of design suits clean liquids.
Semi open impellers have the vanes attached to one plate, leaving the vanes exposed. These are more forgiving to liquids that have suspended particles or are of greater viscosity; the downside is a drop in efficiency.
Open impellers, as the name suggests, have no front or back plate and the vanes are open on both sides. The ability to handle greater solids is balanced with the pumps being smaller and of reduced power to avoid breaking the vanes. This style of pump, however, is the least efficient of the three designs.
The next area to consider is the selection of the sealing options. Again, the choices are vast, but in general the guide to selection must be driven by the process fluid and how the user will operate the pumps. For example, should you choose a sealed pump or opt for a sealless alternative for your application?
While the right choice can be straightforward in some instances, it may be far from clear in others.
Upfront cost coupled with ongoing maintenance, the ability to handle a variety of liquids, temperatures and pressures, the likelihood of dry running and the impact of leaks or fugitive emissions on the personnel or the environment must all be considered.
A single mechanical seal is perhaps the most popular and by far the cheapest solution. However, they should only be considered where a failure of the seal does not have catastrophic consequences. Double mechanical seals [see picture above] virtually eliminate the possibility of leakage from the pump and they are essential when pumping dangerous or toxic liquids. When fitted back to back and incorporating a pressurised barrier fluid they ensure that highly dangerous process liquids are contained, reducing the risk to operators and the environment.
This orientation is only possible if contamination of the process liquid by the barrier fluid is acceptable, as the barrier fluid pressure pot needs to be 1-2 bars higher than the pumped fluid pressure. The barrier fluid also displaces the sealed fluid across the inboard seal and lubricates the seal faces.
The cost of these systems can be high, but there are times when you can’t put a price on safety.
An alternative double mechanical seal arrangement is tandem. This configuration uses a low-pressure buffer fluid and provides a back-up should one seal fail.
Barrier fluids support the system in many ways, such as preventing liquids from vaporising across the seal faces, lubricating the inboard and outboard seal, preventing the process liquid from becoming contaminated and can be used to identify seal failure.
Sealless pumps (mag drive) do not have the flexibility that mechanical seal pumps have. However, it all depends upon the fluid that you’re asking it to handle.
If the process liquid is nice and clean, and low viscosity, a mag drive may be the right option.
If you take cost out of the equation (mag drives are typically 20-40% more expensive upfront than a standard mechanical seal-based alternative) in the right application, these pumps benefit from very little maintenance.
Limitation of use includes liquids containing suspended solids, and applications/operations where dry running or dead heading the pump is possible. This is due to the tight clearances and the need to cool the magnetic coupling by using the process liquid to remove the heat generated by the eddy current losses. Mag drive pumps typically consume around 10% more power than sealed equivalents.
So, what are the basic rules of selection?
Give your pump supplier as much detail about the fluids that you intend to pump: flow, head and suction conditions, the location of the pump, details of the pipe run and material, filters, meters, valves, and the chemical name of the fluid or mix of products.
A competent pump supplier is somewhat like a competent coach, they should be able to offer more than one solution and be able to explain the benefits linked to them.
- Peter Staddon is managing director of The Pump Company