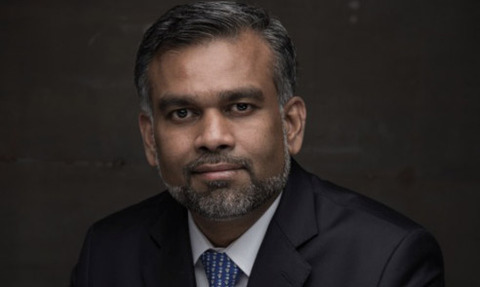
GE’s Azeez Mohammed outlines how analytics are giving the process industries the edge, thanks to asset performance management for variable frequency drive systems.
The world turns – and much of it is moved by motors and generators. Behind every industrial process, electric rotating machines (ERMs) drive production – their ubiquity is such that they consume 45% of the world’s electricity.
Motors are the wheels of industry, powering everything from manufacturing plants and enormous marine vessels to liquefied natural gas (LNG) plants and the ever-increasing number of electric vehicles. Typically, they are connected to a variable frequency drive (VFD) that controls their operating speed and allows them to perform at the optimal point, depending on various mission profiles.
The efficiency gain brought forward has been fuelling the growth of VFD systems, as energy efficiency has become a market and regulatory requirement in the past few years.
For process industries, the consequences of an ERM failure can be severe. But it’s the financial implications linked to those failures that keep operators up at night: unplanned downtime can cost an LNG facility as much as US$4 million per day. Globally, unplanned shutdowns in the process industry cost 5% of total annual production – that’s as much as US$30 billion a year. Similarly, the failure of a multi-megawatt generator that sits in an offshore wind turbine means not only lost revenues, but also very expensive maintenance costs.
It’s the financial implications linked to those failures that keep operators up at night: unplanned downtime can cost an LNG facility as much as US$4 million per day. Globally, unplanned shutdowns in the process industry cost 5% of total annual production
With potential costs so high, profitability is largely linked with the unplanned downtime. The ubiquity of ERMs, thus, makes them a significant part of this equation. Traditionally, vibration sensors have been used to detect ERM failures. However, their cost, both from a material and a deployment perspective, mean they are used for only the most critical machines – and they only detect mechanical failures, not electrical ones, which limits their impacts.
In parallel, one drive can connect to up to 15 ERMs – the consequence of a single drive failure is therefore substantial. However, drives’ selfdiagnosis capabilities have been limited in the past.
Today, each drive possesses one or several processors. Similar to the evolution of processors from personal computers, today’s drives have more enhanced computing capabilities to do high-speed control, data gathering and self-diagnosis. That processing power, sitting ‘at the edge’, leaves huge and yet untapped potential for predictive analytics and ultimately improving performance.
Digitising ERM performance
It is now possible to develop digital asset management tools that offer cost-effective monitoring and analysis of every ERM and drive within a plant. I see these tools as ultimately offering a complete suite of analytic capabilities, broken down into four levels of digitalisation.
The first would be descriptive: enhanced connectivity across the plant would enable machinery to generate vast amounts of data that could be pooled into one centralised location, such as Predix, GE’s Cloud-based digital platform. This could then process the data into quick-view dashboards and provide a real-time overview of the plant’s health and performance.
The second level would be diagnostic, looking at past performance to determine what happened and why. The value here cannot be underestimated: in general, only 3% of data is used for any meaningful purpose, so harnessing data insights will help operators understand the root cause of failure or inefficiency, fine-tune processes and make informed decisions that ensure optimal performance day in and day out.
The next level is predictive – in other words, the ability to analyse likely scenarios of what might happen, usually delivered in a predictive forecast. This relies on large data lakes to build digital twins that compare data to spot performance deviation and give early warnings for potential failures.
Both Cloud and edge processing will be crucial here, so any data that can’t be sent directly to the cloud is processed locally in a device attached to the component being monitored. This reduces the frequency and volume of data that needs to be transmitted to the Cloud, and ensures all possible failure modes are detected. The final level is prescriptive: identifying what actions should be taken, with rules and recommendations for next steps. Imagine the productivity potential when machines are able to communicate directly with each other.
So, once a digital tool, such as asset performance management (APM), detects a deteriorating part for example, it automatically connects with the warehouse or repair service to prepare and deliver a replacement. It then waits for the next scheduled downtime to fit the new part. This is a key step to achieving autonomous operations and an exciting prospect for industries looking to raise efficiency.
Assessing the potential benefits
I envisage effective digitised ERM adding value in several ways. The most essential advantage is the unplanned downtime reduction – by identifying any degradation issues early and before a failure strikes, operators can take action to mitigate problems before they occur and perform maintenance in a predictive manner.
Having predictive foresight of failures, both for ERMs and drives, means being able to automate the ordering and replacement of parts, therefore eliminating the need to tie up capital in costly inventory – and an APM could even provide crucial data to a company’s supply chain that informs factory acceptance tests and minimises the risk of poor performance when new machinery comes online.
Process plants usually encompass a large variety of rotating machines and drives technologies, yet there are also a very large number of standard and thus similar units. Over time, a digital blueprint of these assets can be created to detect similar assets’ performance, as well as to check quality of new units.
Today at GE, we have designed APM algorithms for both ERMs and drives that draw on our vast data lake to deliver accurate analytics – with no costly vibration sensors required. This solution is already being developed across various industries, including metal plant, refinery plant and the navy.
Process plants usually encompass a large variety of rotating machines and drives technologies, yet there are also a very large number of standard and thus similar units. Over time, a digital blueprint of these assets can be created to detect similar assets’ performance, as well as to check quality of new units
In China, Zhongfu Industrial is implementing GE’s digital smelter solution at its aluminum plant to increase smelting efficiency and enhance productivity.
Alco Bio Fuel, one of Belgium’s major biorefineries, is now using GE’s APM to future proof its refinery field operations. And two of the U.S. Navy’s Military Sealift Command’s dry cargo ammunition vessels will also deploy the digital solution, with all monitoring and diagnostics performed remotely by GE in partnership with the Space and Naval Warfare Systems Command.
Industries are under pressure from narrowing margins, stiffer competition and fragmented processes. Used intelligently and backed by technical expertise, I believe digital APMs can be an indispensable ally in the push for productivity and profitability, allowing companies to become leaner and more resilient, both now and for the future.
* Azeez Mohammed is president and CEO, Power Conversion business at GE