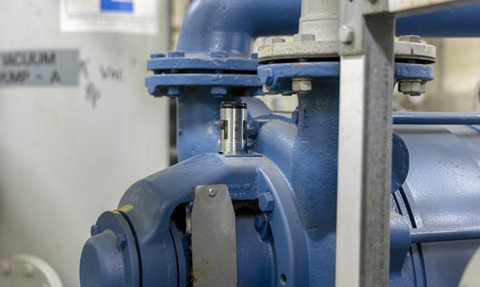
Adopting a condition-based maintenance approach is becoming simpler and more cost effective as new techniques and products hit the market, reports Nicola Curtis.
Geoff Walker, technical director at Faraday Predictive, spent the early part of his career in the chemicals industry. Each year his plant would shut for a couple of weeks so that everything could be stripped down and checked before being put back together again.
“At the end of the shutdown period you’d press the button and hope that all would be back to where it was. But it never, ever happened,” Walker explains.
“You’d press the button on a Friday, and it would take another couple of weeks for the plant to actually get back to anything like the previous production rate.”
Automatic fault diagnosis can provide an answer to the time, cost and skills issues that hinder efforts to detect and deal with vibration problems before they become critical
Lee McFarlane, technical director – asset management, AVT Reliability
While planned maintenance can give some sense of order and is undoubtedly better than the chaos of a breakdown maintenance approach, it is not a perfect solution for two main reasons.
“Even with the best technicians in the world, as soon as you touch a piece of equipment you run the risk of introducing problems that weren’t there before,” says Walker.
“And secondly, very rarely do you have enough data to know what the correct frequency is for doing that maintenance work. You almost always over-maintain so it’s not as cost effective as it could be.”
Adopting a predictive, condition-based maintenance approach, on the other hand, means maintaining your plant only when there is a need to. Any unnecessary work is omitted as is the risk of inadvertently introducing faults.
In principle, condition-based maintenance reaps the planning benefits of planned maintenance but, crucially, also means achieving the inherent reliability level of equipment. As a result, downtime should be slashed, work minimised and huge savings unlocked.
Walker believes that only a tiny proportion of equipment is currently maintained using condition monitoring whereas, in an ideal world, the figure should be around 50%.
Cost is part of the reason for the low uptake. While condition monitoring (CM) reduces expense in the long-term, the significant upfront investment required to not only purchase the necessary equipment but also to fund the required human expertise to run that equipment is likely to feel prohibitive to some manufacturers.
There is also the additional problem of finding enough engineers with the required specialist knowledge to analyse and report on the mountains of data CM produces. However, a new generation of cost-effective, smart CM solutions look set to entice a larger share of the market.
Moving forward
With over 40 years of experience helping companies improve reliability, AVT Reliability is an established name in CM for the process industries. Recent updates to its innovative Machine Sentry system present another step forward in its drive to make CM and asset management faster, more efficient, cheaper and more user-friendly.
Machine Sentry is a web-hosted CM solution that provides detailed tools supported by leading CM engineers. This year the company launched the wireless Machine Sentry MSF-1 tri-axial vibration and temperature sensor.
The sensor incorporates full tri-axial vibration measurement and automatic fault diagnosis assistance (ADA) to identify potential problems and enable pre-emptive action.
“Automatic fault diagnosis can provide an answer to the time, cost and skills issues that hinder efforts to detect and deal with vibration problems before they become critical,” explains Lee McFarlane, technical director – asset management, AVT Reliability [pictured].
The MSF-1 also offers continuous monitoring which reduces the chance of fault conditions being missed and it can be paired to any Android tablet or smartphone, connecting to the Machine Sentry software using standard Bluetooth communications.
“The MSF-1 offers unparalleled real time insight into, and analysis of, the condition of business-critical assets and plant safety,” says McFarlane.
A newer kid on the block, data analytics specialist, Senseye, is also making waves in the world of CM.
Senseye uses a data-driven prognostic approach. Once a data connection is made, the system enters an unsupervised learning phase using either historical data or taking 14 days to learn normal machine behaviour, automatically building models of this. At the same time, it can connect with a Computerised Maintenance Management System (CMMS) in order to learn what actions the maintenance team is taking and build prognostic (Remaining Useful Life) models.
The aim is to automate the data analysis previously undertaken by CM specialists. In theory, the mundane day-to-day monitoring can then be left to the computer while the human experts are freed up to concentrate on the more complex issues requiring creativity and lateral thinking.
Previously focused on discrete manufacturing like automotive, the Senseye system works with any machinery that is collecting suitable data so could be applied to the process industries.
Another way
Vibration analysis currently represents around 85% of the CM industry but it does have some limitations.
It struggles, for example, with equipment which is inaccessible or in a hazardous environment, equipment operating at varying speeds or at varying loads, equipment subject to electrically generated signals and equipment displaying torsional vibration phenomena. Equally, it cannot cope with most electrical problems.
Faraday Predictive are specialists in the application of MBVI (Model-Based Voltage and Current) systems – an entirely different CM technology which does not have the same limitations.
The company’s MBVI systems are a powerful CM and diagnostic technique for equipment driven by electric motor.
We believe that MBVI systems detect almost all the problems that vibration monitoring will detect as well as a whole load of problems that you’d measure with an electrical test
Geoff Walker, technical director, Faraday Predictive
MBVI systems use the motor as a sensor to identify a wide range of phenomena in both the motor and the driven equipment, in the mechanical and operational domains as well as electrical.
The systems measure the voltage and current drawn by the motor and do not need sensors fitting to the rotating equipment itself. These measurements are normally made in the motor starter cabinet, avoiding the cost and complexity of fixing accelerometers to each bearing, avoiding costs of cabling, and avoiding the risk of mechanical damage to the sensors.
The systems build a model of the relationship between voltage and current. This model is used to identify the distortions on the current waveform that have not been caused by distortions on the voltage waveform – and which therefore must have been caused by the behaviour of the motor driven equipment.
MBVI systems can be supplied either for permanent installation or as a portable kit that can be connected temporarily to give a quick assessment of the condition of the equipment. “We believe that MBVI systems detect almost all the problems that vibration monitoring will detect as well as a whole load of problems that you’d measure with an electrical test,” says Walker. “We’ve been working on this system because we believe it has the ability to transform the whole condition monitoring industry.”
* Condition Monitoring Apprenticeships: While there is already some excellent CM training available from a number of service providers, the Institute for Apprenticeships (IfA), recognising the importance of condition monitoring for the future, recently gave its consent for the development of a CM apprenticeship.