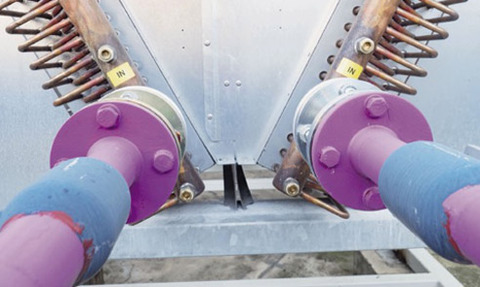
With the energy industry in a state of flux, it’s not only the large corporations that gain from applying their expertise. Firms are developing revenue streams within niche pumping markets too.
Economic gains from the renewable energy revolution are not limited to the existing big players, which has enabled business users to themselves become producers, cutting their own costs and embracing new revenue streams.
And, given that very little of the transformation taking place does so without the inclusion of a pumping system within the overall process, the sector is benefiting in myriad ways.
Sulzer, long a leader in pumping systems in the sustainable energy market, has applied its expertise in transforming one capital city’s cost intensive waste into more profitable enterprises with a green angle.
Vienna’s wastewater treatment company, ebswien has embarked on an energy optimisation through sludge treatment project to achieve this, employing Sulzer to help maximise energy efficiency and optimise power generation.
Combined with high resolution analogue inputs, the accuracy of calculations gives greater control, meaning continued assurance for heat and power generation
Adrian Whitten, systems manager, Ashdale Engineering
Traditionally, the plant consumed circa 60GWh of electricity annually; ebswien aimed to make biogas production, using sewage sludge, into the core of a truly sustainable, self-powering facility based around six 30-metre high digesters, each capable of generating biogas from 12,500 cubic meters of sludge.
Sulzer proposed a 4.5 metre diameter Scaba vertical agitator, rotating at 8rpm and requiring small 11kW motors to continually stir the sludge in the digester tanks to keep the anaerobic digestion process running optimally.
Performance specifications, the Scaba units would need to achieve 90% homogenisation of a tank in a maximum of two hours but achieved this in 77 minutes.
Suspension of the agitator blade from a 25-metre shaft with no bottom bearing ensured fibrous material in the sludge travelled down the shaft, eliminating the risk of tangling and jamming in operation.
Sulzer suggested also that the required output could be delivered using eight smaller 400kW HST turbocompressors in preference to the intended 1.2MW compressors. reducing total power consumption by 400kW.
The site now produces around 78GWh of electricity and 82GWh of heat, generating all the energy required for wastewater treatment with energy to spare and reducing the Austrian capital’s yearly carbon emissions by 40,000 tonnes.
Although there are rewards for operating such systems at scale, the benefit of renewable energy is that smaller scale process firms can also get in on the act.
While it is no minnow itself, Mitsubishi Electric Ireland is enabling companies of disparate sized to play a role in the energy system.
Its automation partner, Ashdale Engineering in Northern Ireland, has designed a high accuracy process control system for an anaerobic digestion (AD) plan using Mitsubishi Electric automation components. These ensure continued operation of the live AD process, enabling the generation of heat and electricity that the plant operator now has plans to sell to the grid.
The anaerobic digester at a large farm near Armagh drives a combined heating and power (CHP) plant that heats the farm’s buildings while also producing electricity. Animal slurry, silage and additives are mixed together and the resulting biomass then is heated to produce biogas, used to power the CHP.
Customers are able to draw on our expertise… to implement the most effective and reliable products for their applications
Richard Hinchliffe, technical sales engineer, Scattergood & Johnson
Temperature control is a vital aspect of anaerobic digestion; the microorganisms that break down the biomass require temperature stability. Fluctuations above 1°C per day can kill them, stopping the process and with it, the generation of heat and power. In the event that this occurs, it takes considerable time to remove and replenish the biomass to restart the AD process. In addition to offering stability, the control system also needs to be responsive, easy to use and reliable.
“The AD plant has capacity for around 40,000m³ of biomass fuel and small changes to any of the variables can impact the temperature of the biomass,” explains Adrian Whitten, Ashdale systems manager.
By utilising the sophisticated programming features of Mitsubishi Electric’s MELSEC-Q Series PLC, Ashdale was able to develop an accurate and reliable control solution. Analogue flow and temperature signals transmitted from the pump house and digesters, which could be up to 30 metres away, are communicated over CC-Link via remote I/O. Interaction with the PLC takes place via a HMI communicating over Ethernet and a variety of Mitsubishi Electric variable speed drives control the system’s pumps. The solution ensures reliable heating and power generation and is now providing the opportunity for profitable export to the grid.
Says Whitten: “Floating point number calculations, made possible by Mitsubishi Electric’s MELSEC-Q Series PLC, were vital to achieve the precise control required to ensure long-term stability of the process. Combined with high resolution analogue inputs, the accuracy of calculations gives greater control, meaning continued assurance for heat and power generation.”
“Some farmers may overfeed the AD system, or feed a recipe that is too rich. Again, this can kill the microbes and stop the process. Any changes in the feed have to be made very gradually and with precise control.” The plc allows for expansion on I/O, as required to control additional drives as well as pumps. This permits the scale up of the operation and energy export to the grid.
“The HMI’s recipe system allows farmers to retrieve feed ratio data from previous months and years, identifying how the ratio changed according to the season. This way, planning and monitoring recipes is a simple process for the farmer to manage for optimum generation and efficiency,” adds Whitten.
Taking in the view
Monitoring data and alarms can be easily viewed from any internet-connected device and the system can be controlled remotely too. Ashdale Engineering’s system design integrates gas monitoring into a single measurement sensor, removing the need for multiple analogue devices that measure each gas separately.
The next stage for the AD plant operator is to expand the process and export biomethane as well as electricity to the grid. This requires an increase in the methane content of the produced biogas from 70% to 90%, the level needed for export to the grid, which will be achieved by the partnership between Ashdale Engineering and Mitsubishi Electric.
The move towards greener energy, though, presents not only opportunities but also greater ethical and regulatory requirements.
Emissions of pollutants from industrial processes mean businesses must invest in various technologies to ensure compliance. A major challenge when reducing CO2 levels is the amount of energy required by many processes.
One firm, C-Capture, has developed technology that uses a new class of solvents to capture CO2 and enable it to be processed and stored, either permanently or for use in another industrial process.
The company designs chemical processes for capturing CO2. Using in-house test rigs, data is generated which, the firm asserts, lay the foundations for industrial-scale solutions that are set to significantly reduce the emission of greenhouse gases.
A key role in the operation has been performed by the use of particular valve systems, pioneered by Bu?rkert. And suggested by C-Capture collaborator, Scattergood & Johnson, the specialist supplier of electrical engineering and fluid control components.
An in-house test rig involves the flow of the solvent into a wetted wall column. It was important to precisely regulate the solvent flow to enable the collection of accurate test data.
The process required an all-electric flow control device, since a pneumatically controlled valve would only add further cost and complexity to the project, both at the pilot stage and beyond. Scattergood recommended the Bu?rkert Type 3361 2-way globe control valve as the best solution, due to its precise and fast flow control.
The Type 3361 also offers a flexibility of design to meet the requirements of the application. As part of an experimental project, the need for precise data was paramount and the valve offers both analogue and digital outputs. Furthermore, the option of five interchangeable valve seats allows the Kv value to be optimised, while the ability to add a position controller or a process controller to the application makes it suitable for both centralised and decentralised systems.
Scattergood technical sales engineer Richard Hinchliffe commented: “Customers like C-Capture are able to draw on our expertise and knowledge to implement the most effective and reliable products for their applications. Having understood all the requirements for the experimental rig, it was clear that the Bu?rkert valve would offer the best solution. Bu?rkert’s wide range of control valves with precision and reliability built-in offered an ideal solution.”