Automation enables firm to drive contract storage ambitions
13 Jul 2022
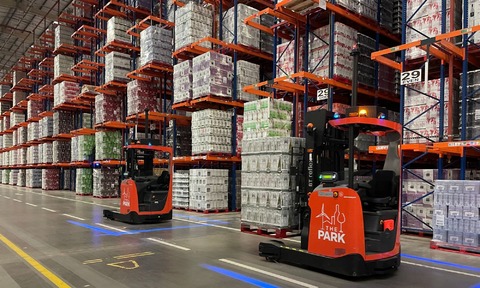
Britain’s largest bottling and storage independent wanted to ramp up its customer supply. Automation was the key ingredient for achieving this...
Situated close in Bristol to the River Severn, The Park facility is the UK’s largest independent bottling and wine storage site.
Operator Accolade Wines is an industry leader both in Britain and its native Australia, with a portfolio that includes several of the best known Antipodean brands including Hardys, Echo Falls, Banrock Station and Kumala.
Its strategy involves boosting its roles as a contract beverage and packing company for other businesses in the drinks sector: The growing use of bulk tanks to import wine by ships has massively increased delivery levels from the likes of Australia.
But, said The Park’s general manager Richard Lloyd, this has led to a need for more storage in the UK.
“More than 40 per cent of all the wine that arrives in Britain is estimated to be brought into the country in bulk tanks before bottling for the simple reason that it is possible to fit close to two and a half times the amount into a shipping container if the wine is stored in a bulk tank rather than bottles,” explained Lloyd.
Its strategy involves boosting its roles as a contract beverage and packing company for other businesses in the drinks sector
To enable it to achieve its objectives, Accolade needed to reorganise its Bristol base in order to improve production efficiency and reduce overall labour costs while attracting and counter problems keeping key personnel such as forklift operators.
The company turned to Toyota Material Handling, which had successfully delivered more than 270 automated projects across Europe, featuring more than 1,000 guided vehicles across Europe.
When it came to redeveloping The Park, nearly 50 percent of the budget was devoted to automating empty bottle storage sand upgrading the manually-operated truck fleet.
Eight Toyota Radioshuttles were installed within the empty bottle storage system, to automatically place or retrieve palletised loads of empty glass bottles within the racking.
Initially, manually-operated forklifts unload empty glass and deliver them palletised at the in-bound marshalling area.
There, an order is triggered and the fully automated reach trucks are sent to collect loads in a pre-arranged sequence and deliver the empty bottles to the high-density rack system. Automated reach trucks place pallets on to one of eight newly-installed Toyota Radioshuttles which delivers the pallet to its designated position.
When required, a Radioshuttle is instructed to retrieve an appropriate pallet and deliver it to the automated reach truck that delivers the bottles directly to the production area.
Finished loads are taken by the automated reach trucks and deposited at stations within the finished goods store before being stored by Toyota VNA trucks.
The firm had made certain that it did not simply invest in automation that might become obsolete quickly
Built-in scanners and obstacle detection units preventing collisions allow machines to operate in the same area as staff and materials-handling equipment. Toyota’s in-house-designed Order Manager software tracks goods storage, orders, traffic and flow.
Said John Hobbs, Toyota project manager – logistics solutions: “A lot of integration was required to automate what had originally been done manually. We had to be sure that messages were going back and forth correctly between the client’s WMS and the system that controls the new hardware.”
The finished site opened for operation this summer. General manager Lloyd commented that although automation costs were decreasing and producing better returns, the firm had made certain that it did not simply invest in automation that might become obsolete quickly.
Toyota’s Hobbs added: “As The Park demonstrates so clearly, automating those aspects of a wine warehouse’s operation that follow a predictable pattern makes a lot of sense – particularly since relatively recent developments in automation technology have seen the emergence of flexible and scalable products that deliver a rapid return-on-investment by driving productivity, saving costs and improving on-site safety.”