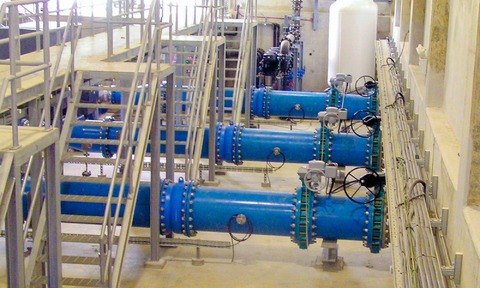
GEMÜ Valves in Drinking Water Applications: In a successful large sea water desalination, the system operates according to the reverse osmosis principle and produces more than 136,000 m³ of drinking water per day. This is enough to fill about 55 Olympic size swimming pools.
Technology and process
Sea water desalination runs in several process steps. The first step is the drawing of the sea water which feeds into the system. This is followed by multi-stage filtration, floatation and ventilation to remove suspended matter and undesirable substances dissolved in the water. The filtered water is conditioned with ferric chloride FeCl3, sulphuric acid H2SO4, hydrochloric acid HCl, caustic soda NaOH and other additives for reverse osmosis and set to a specific pH value. Without these important water treatment steps, the downstream osmosis diaphragms would become useless in no time.
After conditioning, the water is fed to the osmosis diaphragm modules by high-pressure pumps. The systems have a modular structure so that the diaphragms can be backwashed at regular intervals. In a system with 10 modules, for example, one of the modules is always in backwash mode whilst the others produce drinking water. In the last part of the system, after the reverse osmosis, which supplies almost distilled water, the water is brought back up to drinking water quality mineral content. This is the final process before the water is fed into the distribution pipes to the consumers.
The GEMÜ solution
GEMÜ has supplied more than 760 valves in nominal sizes from DN 15 – 1400 for this project. With our wide range of valves and accessories, as well as measurement and control instrumentation, GEMÜ provides an optimal solution from a single source saving the customers time, effort and cost not only in logistics and installation but also in documentation.
A range of pneumatic, motorised and manual butterfly valves with different disc materials in 1.4408, bronze or ECTFE coated are mainly used in the sea water inlet, in the filtration/floatation and in the supply (tanks and pump stations). The nominal sizes range between DN 65 – 1400, with operating pressures of 2.5 – 18 bar depending on the process area.
In water pre-treatment and post-treatment, highly chemically resistant diaphragm valves made of PVC or PVDF are used for dosing FeCl3, H2SO4, HCl, NaOH etc. The nominal sizes range between DN 15 - 40, with operating pressure approx. 3 – 5 bar. Float flowmeters of nominal sizes DN 20 – 40 are also installed. Chemical dosing is fully automatic, so the valves are usually controlled either electrically or pneumatically.
The high pressure and non-return valves on the pump stations in front of the osmosis modules are made of special materials such as Super Duplex A890. These valves are pneumatic and equipped with intelligent position indicators. The differential pressure in the start-up phase of a pump is up to 59 bar. The operating pressure is usually between 5 – 84 bar, and the valves are designed up to DN 300.
For more information, click here.