Viewpoint: Working safely with heat transfer fluids in plastics manufacture
13 Mar 2024
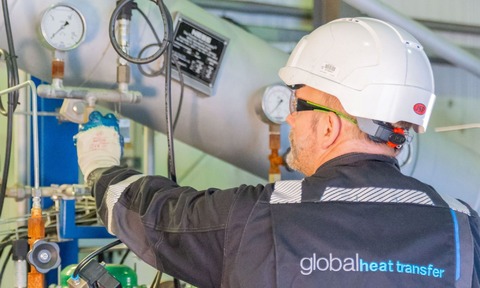
Plastics and polymers are vital materials in manufacturing. Global Heat Transfer’s Clive Jones explains how choosing, operating and maintaining thermal fluid can impact productivity…
Many applications in plastics manufacturing processes, such as die casting, molding, and extrusion, require precise temperature control. Specialist heat transfer fluids are designed to safely and effectively reach and maintain these temperatures when used with plastics manufacturing equipment, such as coating rolls and heaters.
With so many thermal oils on the market, manufacturers must take the time to understand their specific requirements. By matching the fluid to the system and the application, manufacturers can maximise efficiency and sustainability while reducing costs and environmental impact long term.
The chemical composition of the heat transfer fluid will often determine its properties. Mineral oils are often used for non-toxic, cost-effective applications with moderate temperature requirements, whereas synthetic fluids are designed to operate in higher temperatures for extended periods of time. In plastics processing, synthetic fluids are often a better choice than mineral oils because of the high temperature requirements. As a result, synthetic fluids will have a longer lifespan, extending time periods between fluid changes, when managed correctly.
After shortlisting fluids based on chemical composition, looking at operating temperature ranges will be key. Molding processes, for example, require heat transfer fluid with a broad temperature range to ensure effective heat transfer and maximum efficiency across production. The fluid must be able to work efficiently at both the highest and lowest temperature required for the application, so manufacturers should look at the fluid’s minimum and maximum operating temperatures.
While it often operates in the background, heat transfer fluid is integral to many steps of the plastics manufacturing process
Once selected, engineers must drain, clean, and flush the heat transfer system of older fluid before introducing the new heat transfer oil. Circulating a specialised cleaning and flushing fluid at temperature will activate the detergent additives that will mix with suspended loose particles.
Maintaining
If thermal fluid is left to operate for long periods of time without regular monitoring or maintenance, any potential issues may go unnoticed until they impact production.
If the system temperature fluctuates too much, it will impact the product finish — for example, plastic materials that are exposed to very high temperatures for prolonged periods will lose strength and toughness, and if the temperature drops too low the material may not mold properly. By introducing proactive measures, such as regular thermal fluid sampling and analysis, engineers can reduce waste while slowing fluid degradation to improve overall efficiency.
Degradation will occur as a heat transfer fluid reaches the end of its lifespan but will accelerate if thermal fluids are heated above operating temperature or not regularly monitored and maintained. Operating at high temperatures for long periods at high temperatures leads to oxidation and thermal cracking. These processes produce contaminants, such as carbon, that may start to build up inside the pipes and negatively impact heat transfer efficiency, eventually causing blockages.
Regular thermal fluid sampling and analysis is essential to understanding oil condition. We recommend engineers take a closed sample when the system is live, hot, and circulating. Thermal fluid specialists and independent analytical chemists can analyse these samples and provide advice on any interventions that will slow degradation. These interventions could include changing the operating temperature, fluid dilution, or commission of a Light Ends Removal Kit (LERK) that filters potentially harmful light ends from the system. Over time, engineers can also look at sample analysis to track fluid condition.
To complement regular fluid sampling, proactively monitoring the system itself will help engineers maintain uptime. Daily checks of pipework, pumps and gauges give engineers an opportunity to identify any potential issues with core components. Detecting issues early on and keeping critical spares on site enables engineers to clean, fix or replace any parts in a timely manner, reducing the risk of production losses and downtime. During walkarounds, engineers can also check the facility is clean, organised and that areas are correctly signposted — improving general housekeeping and clearly posting procedures can both keep workers safe and aid productivity.
While it often operates in the background, heat transfer fluid is integral to many steps of the plastics manufacturing process. Taking the time to select a fluid with the optimal temperature range and desired characteristics, introducing regular sampling to understand its condition and promoting best practice to safely and efficiently maintain the system are therefore key to increasing productivity in this growing industry.
Clive Jones is managing director at Global Heat Transfer