Bayer tracks down hidden efficiencies
15 Mar 2011
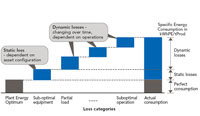
Bayer Technology Services (BTS) has developed a process optimisation programme that is being applied at the chemical and pharmaceutical plants of the Bayer sub-groups, as well as at process facilities owned by external companies.
The BayOpX programme, which is based on Bayer’s technological expertise, employs hardware and software tools to continuously monitor process, unit and plant data. The integrated approach also taps in to the know-how of operators at the plant.
The programme is designed to help engineers and operators identify and exploit efficiencies often hidden within the complexities of their production processes and production networks. It focuses on five specific areas: energy, raw materials, equipment efficiency, working capital and personnel.
According to BTS, energy efficiency is currently the most effective ’lever’ for BayOpX: reducing investments in energy infrastructure, minimising energy cost, increasing competitiveness and lowering emissions.
BTS has, therefore, developed the Bayer Climate Check to identify energy savings up to 20% in production processes and pinpoint priority measures on how to achieve these potentials. It employs two elements: Energy Efficiency Check and Climate Footprint.
By the end of 2010, Bayer had systematically analysed over 140 production plants around the world with the Bayer Climate Check, accounting for around 90% of the group’s greenhouse gas emissions.
Energy Efficiency Check is a systematic methodology to identify all measures to reduce energy consumption and CO2 emissions. It is an integrated approach, which requires the efficient and systematic cooperation of experts from various disciplines, including plant personnel.
This encompasses energy sources such as electricity, steam, cooling water, fossil fuels, and pressurised air up to raw materials and additives.
lso analysed are the production process, auxiliary units, energy production and infrastructure, facilities, the lighting as well as air conditioning.
Integration networks
Typically, the identified measures include the improvement of pumps as well as complex heat integration networks. But the system can also highlight the potential of innovations in process intensification, such as microreaction technology or solvent-free production routes.
Bayer Climate Footprint, meanwhile, considers all direct and indirect emissions of a production plant, including its supply chain, until the product leaves the plant (cradle-to-gate analysis).
With this tool, it has become possible to evaluate not only a production plant, but also all the raw materials and energy needed for production itself, together with the logistics up to the factory gate.
The BayOpX programme is designed to help engineers and operators identify and exploit efficiencies often hidden within the complexities of their production processes and networks
Bayer has also recently developed the STRUCTese energy efficiency management programme to sustainably implement all measures identified in the Energy Efficiency Check.
The STRUCTese programme allows the direct measurement, tracking, benchmarking, and target-setting of energy efficiency, in contrast to measuring energy consumption alone. It, therefore, requires commitment from all organisational levels of the company, from shop floor up to management board.
Current performance as well as technological, technical, and operational potentials at each plant are calculated and reported month by month. The system helps plant personnel to optimise the operation of their units, plant management to focus on the most effective measures, and management to develop an overall efficiency strategy, set targets and track progress.
At the heart of STRUCTese is the Energy Loss Cascade, which allows users to consider various types of energy carriers - steam, electricity, cold etc - and the aggregation of cascades on various levels, such as plant, site, product, or company, as well as over time.
Product- and process-independent KPIs are calculated from the cascades to allow straightforward tracking, benchmarking, and target setting. Losses between minimal and actual plant energy consumption are assigned to a number of different loss codes to visualise dominant levers, separate main influences, and clarify in which field progress can be achieved most effectively.
Continuous progress
The company-wide cascade reporting and management system is supplemented by measures at the plant level to support continuous progress, including active change management, improvement project initiatives, on-line monitoring and daily energy protocols.
Setting up STRUCTese, and thereby moving an entire company towards operational excellence in energy efficiency, requires the cooperation of a number of disciplines, including plant and process expertise, statistical data analysis, process simulation and IT.
The Energy Efficiency Check facilitates the preparation of suitable lists of activities and enables optimisation methods to be prioritised. By 2012, over 60 plants will be included in the STRUCTese roll-out at Bayer, the company forecasts.
The BTS approach
Teamwork vital for process optimisation
Process optimisation projects often have two steps: the concept synthesis and the implementation of optimisation measures, according to Dr Hans-Joachim Leimkuehler of Bayer Technology Services GmbH.
During concept synthesis, he explains, different disciplines like chemistry and chemical engineering contribute to the project success. Experts from the plant (client) and the consultant are involved and strong unit operation experts are needed for the optimisation of specific items of equipment.
Process simulation experts integrate their results into an entire process concept, working together under a strong project management.
Experts for different disciplines are important, but the management of the interfaces and visibility of the entire process are the most crucial requirements for success, explained the Bayer expert. The project team, he added, needs cutting-edge methods, such as for process simulation (short-cut and rigorous) and fast-cost estimation.
“A deep knowledge of unit operations and a comprehensive overview over actual equipment developments is a must,” said Leimkuehler.
“The contributions of the whole team enable us to generate and evaluate several process variants in a short time. The team then designs the optimal solution for a given optimisation task, considering profitability and feasibility of the proposed measures.”
The second step involves implementing the selected solution in the plant. Sometimes it is possible to improve the process only by optimising the process parameters, but in most cases process optimisation requires reconstruction within the plants.
Here we need a higher degree of efficient execution skills,” said Leimkuehler. “Additional disciplines, like process control or engineering, join the team and therefore a strict project management is very important.’
Data handling should be supported by data warehouse software applications to assure consistency in the realisation phase, either BTS’ PEDW (Process and Engineering Data Warehouse) solution or commercial products.
Leimkuehler also strong recommends the continuous involvement of key experts during the synthesis and implementation phases to minimise the risk of communication failures.
“Process optimisation should have a sustainable effect,” the BTS manager concluded. “We assure the sustainability by technical measures like on-line monitoring of efficiency indicators and by management of the change in the plants, such as training of the operators. Both aspects lead to sustainable and more efficient and profitable processes.”