Reducing pumps energy use at chemicals facility
2 Jul 2012
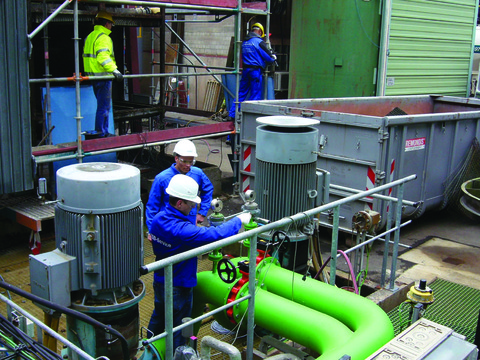
London – ?Solvay Fluor GmbH has reduced power consumption by a quarter at a modernised re-cooling system serving its hydrogen fluoride plant in Bad Wimpfen, Germany.
Following the modernisation, which involved installing a new cooling tower, Solvay Fluor engaged KSB Service GmbH to check that the installed power of the pumps matched the upgraded system. Previous changes to the production processes had reduced the total amount of cooling water required, so that that the old pumps were running outside their original operating point.
KSB assessed the system and its components and recorded essential measured variables, including suction and discharge pressure, temperature and flow rate as well as electrical characteristics such as voltage, current, power and speed. In addition, the vibrations measured on the bearing bracket allowed engineers to judge the amount of wear on the pumps and identify any imbalances, misalignment and warping.
Solvay Fluor had two Wernert VZ 250/250-470z type tubular casing pumps installed in its cooling water circuit. Built in 1976, they normally worked one-at-a-time and supplied the required cooling water from an open collecting tank positioned at the foot of the cooling tower.
The analysis showed the input power of the two pumps to be between 80.3 and 93.5 kW, depending on their output. Although originally designed for a flow rate of 600 m³/h at best efficiency point, they only delivered 300 m³/h 90 % of the time; during the remaining 10 %, the flow rate amounted to 400 m³/h.
The two pumps were clearly oversized, because changes in the process conditions and the construction of the new cooling tower meant that the required flow rate had gone down to 400 m³/h, and even after the planned addition of a further cooling tower cell would not exceed 450 m³/h.
To find a replacement for the old tubular casing pumps, KSB engineers compared several GPV-W type vertical volute casing pumps of different designs, KRTK type submersible motor pumps and B16 type deep-well turbine pumps.
The exact comparison of power ratings, savings and payback periods showed that replacing the existing pumps with vertical volute casing pump type GPV-W 150-400 would optimise energy consumption without the need for major modification work.
With a flow rate of between 310 m³/h and 390 m³/h, and a head of about 60m, the input power of this pump type is between 65 and 79 kW. This would give an annual energy-saving of 99,776 kWh - around €9,978 per year - and the payback period based on the investment costs of about €18,000 came to around 1.9 years.
After commissioning, KSB performed a second set of measurements to establish the second load profile and to check the efficiency of the newly installed pumps.
Vibration measurements produced normal values and the flow measurement data showed that the pumps, running alternately, delivered cooling water at a flow rate of around 365 m³/h.
The power input now amounted to 76 kW, which meant that pump input power, taking into account both motor efficiency and cable losses, was around 71.6 kW. If the changed operating point and the flow rates of the old pumps of 310 m³/h and 390 m³/h, respectively, are taken into consideration, the savings reached 28.7 %, slightly exceeding the savings originally predicted.
The two new pumps have been in operation for an entire year and, reports KSB, the cost savings are running higher than initially assumed, at €20,700 a year.