Selecting rolling bearings for drill rig plant and machinery
16 Jul 2012
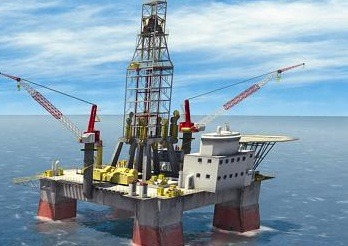
Drill rig operators must select bearings that maximise machine availability and prevent unplanned downtime, says Dr Steve Lacey, Engineering Manager at Schaeffler UK:
Rolling bearings for offshore drilling rig applications such as mud pumps, winches and drill string rotary tables, must operate in some of the harshest conditions on (and under) the Earth. These unforgiving environments subject the drilling equipment to extremely high stresses, so the bearings must be robust and reliable.
In terms of total cost of ownership, when selecting suitable rolling bearings, the entire lifecycle of drill rig plant and machinery must be considered, not simply the purchase costs of individual components such as the bearings.
As well as finding a suitable supplier of rolling bearings, drill rig operators must also consider what type of related support services that supplier is able to offer.
For example, does the supplier offer expert technical advice from experienced engineers who are familiar with oil & gas industry applications? Can the supplier tailor its bearing products to meet my exact needs?
Also, is the supplier willing and able to develop new bearings for specific applications, from concept through to volume production? Perhaps the OEM or drill rig operator is looking for a bearing supplier that is willing to collaborate as a development partner?
Bearing technical support is also an important consideration here. These services typically include advice and guidance on the mounting and dismounting of bearings, as well as recommendations on suitable lubricants and how to properly inspect used bearings.
Some bearing suppliers are also able to offer powerful bearing design calculation software tools to help analyse bearing designs in more detail and to ascertain whether these designs are suitable for a particular drill rig application. The friction values of alternative bearing designs, for example, can be compared quickly and easily.
Using these software programs, it is also possible to precisely calculate, display and document the load acting on each individual bearing location on a mud pump or motor, while taking into account a wide variety of environmental conditions. In this way,
Bearing design calculation and analysis software will become increasingly important to drill rig operators and their equipment OEMs, as operators continue to search for new oil and gas reserves at ever increasing drill depths.
Condition monitoring (CM) of bearings is also an important consideration and can prolong the life of critical items of equipment. CM services include vibration analysis, acoustic emissions monitoring, force/torque measurements, multi-channel systems for modal analysis, thermal imaging cameras and endoscopes.
As incorrect lubrication is the most common cause of bearing failure, operators should employ suitable bearing greases and lubrication systems for rolling bearings, including automatic lubrication systems. In addition, some larger size bearings can be reconditioned as a cost effective alternative to buying new. Reconditioned bearings are typically available on shorter lead times too.
Some bearing suppliers also offer tailored training on-site at the customer’s premises. Typically these training courses can include the fundamentals of rolling bearing technology, vibration monitoring, or how to install and remove bearings.
Drilling applications
There are many applications for rolling bearings on a drilling platform, from the crown block down to the drill string. These applications require all types of rolling bearing, from basic application-specific bearings to complete ready-to-install systems. This includes needle roller bearings, tapered roller, axial tapered roller, cylindrical roller, needle roller, spherical roller, ball bearings and custom special bearings such as those made from a special corrosion-resistant steel.
Mud Pumps & Motors
Mud pumps supply the drill rig with a constant flow of high-pressure mud, which is used as the drilling fluid. These positive displacement pumps operate at pressures of up to 10,000 psi, resulting in high radial loads at the typical bearing positions, including the crosshead bearings, eccentric bearings, crankshaft main bearings and drive shaft bearings.
Similarly, rolling bearings for mud motors are one of the most demanding applications on a drilling platform. Operating at the end of the drill string, mud motor bearings must withstand high temperatures, high loads, impact forces, as well as direct contact with the contaminated drilling fluid (i.e. mud).
Sheaves and Pulley Systems
Sheaves and pulleys are used in crown and travelling blocks, as well as for heave compensation systems, whose function is to decouple the dynamics of a floating drilling platform from those of the drilling tools. Reliability under high static and dynamic loads is therefore required in order to ensure maximum uptime under such an extreme range of drilling conditions.
Swivel, Top Drive
The top drive or swivel supports the drill string, whilst simultaneously acting as a rotating passageway that permits drilling mud to flow into the drill string. In addition, the top drive provides the torsional force required to turn the drill string. This application requires high reliability bearings that also withstand the shock loads generated during the drilling process.
The solution here is to utilise high capacity bearings that are resistant to any possible spikes (peaks) in load. As well as providing these types of bearing, Schaeffler also encourages operators to work more closely with its application engineers in order to better understand the stresses developed during these periods of high load. By carefully analysing both the bearing design and structural components, these resulting stresses can be minimised.
Rotary Tables
The rotary table is the traditional method of providing the rotational force to turn the drill string. When the drilling process is interrupted, the rotary table can also function as a supporting device, carrying the entire weight of the drill string. Here, the bearing locations are exposed to high radial and axial loads.
Due to these very demanding requirements, axial angular contact ball bearings are the preferred choice for the main bearing in rotary tables, in either single row designs or as three race assemblies. These bearings are distinguished by their high axial load carrying capacity. Schaeffler also manufactures the pinion bearings that help provide trouble-free operation on the input shaft.
Winches & Draw works
The primary function of the draw works is to raise or lower the drill string and to provide the correct weight on bit. The latest draw works and winches can also operate using Active Heave Compensation, which compensates for the movement of the ocean’s waves on the floating rig. The resulting rapid load cycles require an extremely rigid system.
Spherical roller bearings are the preferred solution for a hoist drum main bearing. These bearings compensate for any misalignments, whilst providing high load carrying capacity. Other bearing positions can be found in the motor and gearboxes that drive the hoisting drum. All of these bearings work together as a complete system to ensure reliable operation.