Achieving effective spares management
14 Aug 2012
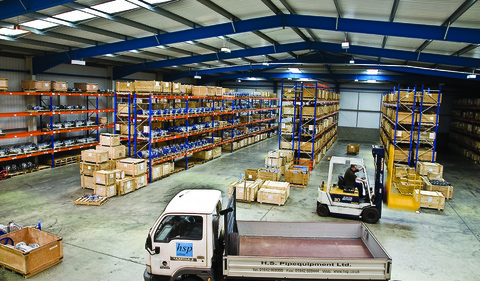
Faced with tight budgets and the need for optimum plant and equipment availability, organisations should more consider the importance of effective spares management says, Mike Aldridge, service business manager for Siemens Industry:
Manchester, UK – When dealing with ageing machinery, organisations may consider the need to keep significant quantities of spares on site to overcome the associated risks to production and equipment efficiency.
They may also hold the view that ensuring spares levels are high will mean maintenance teams can operate more effectively. However, by keeping levels of onsite spares high, organisations also face the risk of tying-up cash reserves which could be used in other areas of the business.
When substantial amounts of an organisation’s capital are used to fund spares stockholding, financial departments can face regular problems around cash flow, but for maintenance teams, the need to have swift access to quality spare parts is important.
To enable plant and equipment to run effectively and efficiently both issues need to be overcome, requiring an effective solution that balances the need for quality spares at a moment’s notice, with minimal impact on cash flow.
It is also important to consider that spare parts for ageing machinery can often be hard to source, which is why some operators overstock to avoid any potential impact on production if a part fails or needs replacing as part of routine maintenance.
In addition, due to technological advancements, newer parts are introduced to incorporate design improvements and old spare parts are systematically phased out.
When faced with the need for an obsolete spare part which is no longer in stock, some organisations may rely upon second hand spares, which can pose a risk to a plant’s operational efficiency.
Without effective predictive maintenance in place, the failure of a component cannot always be predicted accurately and this means the management of spare parts can often be an uncertain process.
Accurate decisions need to be made around when to replace a part, which part to replace and the quantity to order. In some cases, organisations do not have the skills or resources to enable accurate spare parts control and efficiency.
To overcome these challenges, an organisation could enlist the help of an expert partner. This can enable the right spare to be sourced at the right time, reducing downtime and relieving the potential impact on costs.
Obsolete parts can be quickly and easily identified through a site audit, providing a thorough gap analysis and obsolescence dates showing which spares could be scrapped and successor spare parts introduced.
Finance options are available for future spares management packages, enabling effective spares management and preventing capital being unnecessarily tied-up in excess spares. In addition, the spares benefit from a comprehensive warranty and it is possible for organisations to access extended warranty options to further minimise risks.