Wireless: How hard can it be?
15 Aug 2012
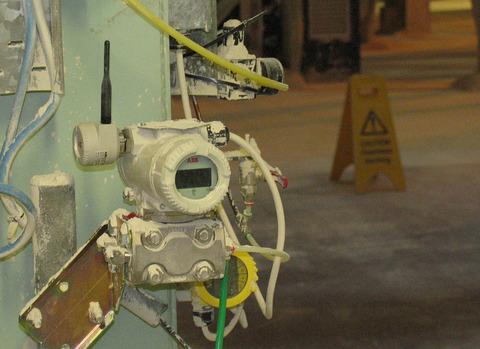
The adoption of industrial wireless at a process manufacturing facility can, it seems, be a daunting and complex affair – even after the relative merits of the WirelessHART and ISA100.11a standards have been considered.
As recommended by a wireless working group at ZVEI - the German Electrical and Electronic Manufacturers’ Association – industrial wireless requires meticulous planning to avoid problems such as jamming or hacking, or interference with systems such as WiFi, Bluetooth and GPRS.
Wireless surveys and the use of simulation software are also recommended to ensure a robust network, as are meetings between all relevant departments including IT, logistics and planning.
The goal, ZVEI advises, should be to develop a co-ordinated approach to managing the overall wireless infrastructure.
While this is all sound advice, it seems at odds with the actual approach being adopted out in industry.
Over recent months, I have picked up a wide range of feedback about the adoption of industrial wireless, particularly from companies in the oil & gas, refining, chemicals and power sectors.
Most, if not all of these companies, are taking a far more direct approach: installing a few devices to see if/how the technology works, and then building up the network from there.
Most operators are impressed with the performance of the network in terms of signal strength and reliability. Where there are concerns, these are more to do with battery life and update rates than, as might be expected, cyber security.
The latter issue, they believe is effectively dealt with by encryption and ‘security by obscurity – or, as one refinery engineer put it “who wants to hack in to find out the temperature of my boiler?”