UK valves suppliers meet N Sea demands
15 Oct 2012
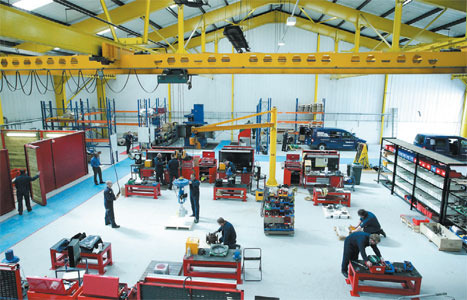
?The oil & gas sector is driving demand for UK manufacturers of valves and related systems - as reflected by recent activity at a range of equipment suppliers to these industries.
Among the players to benefit from this trend is John Mills Valves, part of Wärtsilä Valves Ltd, which has supplied a bronze globe valve to GE Oil & Gas. The unit was for the firefighting system, handling seawater on the Triton FPSO facility, approximately 100 miles off the east coast of Scotland.
The Triton FPSO is used to process 105,000 barrels/day of tanker-stabilised crude oil, using three stages of separation, with a dehydrator and a test separator for well testing.
GE Oil & Gas had required a non-standard valve with alternative flanging and face-to-face dimensions, as well as a quick delivery.
With all the key functions placed under its control, the Newcastle upon Tyne-based valves supplier was required to ensure the turnaround of the project.
“We worked from design drawings to alter the valve pattern, manufacture the product and fully build and test the valve,” said Noel Barker, operations director at John Mills Valves. “The unit was ready for dispatch within two weeks to ensure GE Oil & Gas supplied the valves to the offshore platform on time.”
Specialist valves maker Hobbs Valve Ltd is expanding its operations to meet growing demand for its products from the oil & gas and related industries. The plan has attracted £190,000 in funding from the Economic Growth Fund. This has enabled the company to acquire a fully equipped machine shop double the size of its existing premises in Caerphilly, Wales.
The expansion will enable Hobbs Valve, which produces triple offset butterfly valves, to increase the amount of machining carried out in-house, providing greater control over quality and delivery.
On the back of the investment the company has already created ten new jobs, bringing staff numbers up to 36. The valves maker has also benefited from a £175,000 loan from Finance Wales.
The funding ensured the investment came to Wales, as the company were considering opening another facility in India, said chairman Alun Hobbs, who founded the business seven years ago.
“All our manufacturing is in-house but the machining element was sub-contracted and some suppliers were struggling to keep up with demand, costs, quality and delivery on time,” said Hobbs. “{The expansion] now means we have better control over these elements.”
Hobbs Valve’s core business is high corrosion resistant materials, which are used particularly for off-shore/marine services. It is one of only three companies in the UK solely producing its specialist type of valve and one of around 30 worldwide.
The Welsh manufacturer has also just completed a £1.8-million contract to supply valves for the ballast systems of two new ships to be built in the UK.
Meanwhile, Brighouse, Yorkshire-based Koso Kent Introl (KKI) has recently supplied pneumatic control valves for a project to upgrade the firewater protection system on Statoil’s Kvitebjørn platform in the Norwegian North Sea.
The original firewater protection system had incorporated two, single-stage pressure-reducing valves with simple parabolic plugs. This design had resulted in serious vibration, causing damage to the valves, pipes and other associated equipment.
Testing procedures
Cavitation and instability in the system were identified as the main issues, and the challenge, therefore, was to design a solution that would eliminate these. Central to the problem was the fact that the valves needed to manage a significant pressure drop during testing procedures.
KKI’s proposed design increased the number of pressure let-down stages to be employed within the valve, and incorporated these into a three-stage, cage-guided trim.
Due to the absence of an external power source, a pilot valve, rather than an actuator, was required to provide the valve positioning function in response to changes in the system pressure.
As self-acting actuation is not integral to the KKI range, Blackhall Engineering, located just one mile from its Brighouse site, was selected to fulfil the actuation requirement.
With the design fully approved, production of the two required units was carried out at the KKI plant. The valves were identical, and were produced according to the following specifications: 10-inch series 1200; Rated ANSI 150; 25Cr Super Duplex material; 60% VHFT(L) three-stage cage trim; and Blackhall Engineering pilot valve.