Biomass: material matters
26 Mar 2013
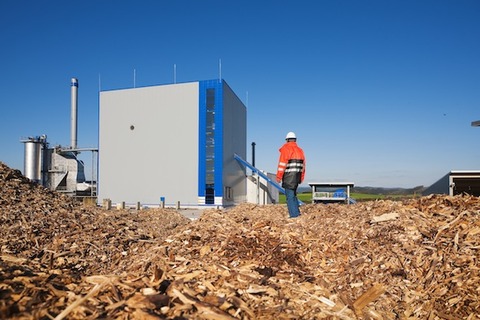
With generous subsidies available through the Renewable Heat Incentive (RHI), organisations can turn a profit for burning biomass rather than having to cope with high energy prices.
It looks easy; take some organic waste on site, or import a low cost fuel like wood chips, burn it to make heat, and claim the money. Get it right, and it can seriously boost income. But the problems can be many and often these systems fail to meet expectations.
The challenges usually lie not with burning the fuel, but getting it to flow properly. The first question the prospective biomass CHP developer should ask is: “What sort of biomass will I have to handle?”
Biomass materials have very different bulk densities. For example pellets can be around 600-800 kg/m3 and wood chip as low as 180 kg/m3. This dramatically affects the storage volume and the scale of the equipment needed. For the same tonnage the equipment size may need to vary by a factor of six.
Water content also profoundly affects the heat output as it needs to be boiled off during combustion, absorbing heat. At 50% water content, many materials approach zero net heat output. So for a given heat output, the water content affects the weight and volume of fuel needed, as well as the size of stores and handling equipment.
Another key concern is resistance to flow, which varies for different material. Tippers and wheel loaders will handle most materials at similar volumetric capacity. Belt conveyors will also, but may suffer blockage in transfer points with some materials. Screw and pneumatic conveyors can be affected by material flow properties, working fine on some materials and failing completely on others.
Equally important is understanding the discharge pattern inside any silo. There are two distinct patterns, “core flow” and “mass flow”. Core flow gives first-in, last-out, i.e. the first material loaded stays put until the silo is emptied.
Mass flow gives first-in, first-out stock rotation, reducing self-heating. Mass flow requires some investment in material characterisation, and can be more costly to build, so before selecting a silo it is critical to decide which you need, and take steps accordingly. Core flow may be acceptable even for materials with a short storage life, provided the silos are emptied completely on a regular basis.
Safety must always be considered. Most biomass materials will degrade and ignite, if stored outdoors. There are exceptions; wood chips can be stored outdoors for limited time, even in the UK climate, depending on their initial condition and the customer’s tolerance of moisture. For long-term storage, wood chip can be covered with matting.
Biomass dust is dangerous, being emitted readily, travelling well, and posing great fire and explosion risks. How material is handled affects the tendency for dust to come out of it, but also affects how much dust is manufactured by breakdown of the particles.
Dust must not be allowed to build up on surfaces or equipment inside plants. Dust on beams, for example, can get suspended, supporting a devastating “secondary explosion” after a minor incident.
Housekeeping must be scrupulous. If you can write your name in the dust, you have a catastrophe waiting to happen. Youtube “Imperial Sugar Explosion” to see the effects.
Mike Bradley is the director of The Wolfson Centre for Bulk Solids Handling Technology at Greenwich University.