Learning the lessons
8 Apr 2013
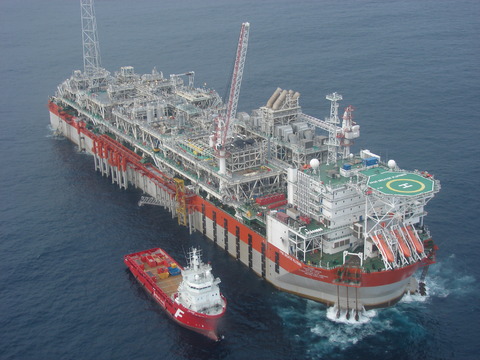
This summer Oil & Gas UK will stage a major offshore safety conference to mark the 25th anniversary of the Piper Alpha disaster - still the world’s worst offshore disaster, claiming the lives of 167 men.
The event, to be held in Aberdeen, 18-20 June, will bring together people from across the global oil and gas industry to reflect on the lessons learnt from the tragedy, and review how far offshore safety has evolved since.
According to Oil & Gas UK’s health and safety director, Robert Paterson, the event shows industry’s “determination to continuously improve safety performance to ensure the next 25 years and beyond never see a repeat of such disasters.”
Such goals reflect the fundamental challenges facing oil & gas and all other process industries involved in hazardous activities: putting in place sustainable systems and procedures that address the myriad of often complex elements and interactions that determine process safety
A further concern is that traditionally, safety issues have risen sharply to the top of the agenda in the wake of major disasters, only to gradually slip back once all the low-hanging-fruit-type improvements have been made, and other business priorities take over.
Well intentioned
“All too often we find the actual ‘effectiveness’ of well intentioned schemes can very rapidly diminished as managers seek to influence outcomes and meet targets,” said Jake Molloy of the RMT (Rail, Maritime and Transport Worker) trade union - speaking at an event, last year, on lessons from the Macondo disaster.
At the same meeting, Ian Travers of the HSE’s Chemical Industries Strategy Unit, noted that the risk/reward equations on which the individual decisions seem to have been taken on the rig look as though they were heavily weighted towards getting things done quicker, and thus cheaper.
Likewise, he said, in the run-up to the accident on 20 April 2010 a series of decisions were made where higher-risk options were chosen over lower-risk ones to save time.
Poor management was also found to have left no overall effective monitoring of these risks overall, while poor communication left key people on the rig unaware of the increased risks.
Since the accident, BP has been working to develop a programme of offshore risk indicators. The company is using leading and lagging metrics to help drive performance improvements.
In a recent speech, Richard Morrison, vice president, global Deepwater Response at BP, said the company was moving to enhance and continue systematising risk management within the company from the boardroom to the rig.
A revised ‘group risk standard’ at BP now requires the same risk ranking matrix to be used by every operating entity in the company, with no exceptions, according to Morrison. This, he reported, is improving the quality and impact of risk action plans and enhancing BP’s ability to demonstrate year-on-year reductions in risk.
“This systematic approach has yielded important connections and new insights,” he explained. “For example, when we examine the safety and operational risks at the level of our global operations, we find approximately 30 common barriers that we rely upon to prevent risk events.
“These barriers include elements like safety instrumented systems, PSV’s, procedures, competency assessments. More interesting, though, is the frequency with which they show up on our prevention action plans. This is helping us move the right people to the right places to assess and assure the quality of these barriers.”
Meanwhile, BP’s upstream operations have been restructured along functional, rather than asset-based lines.
Morrison explained: “We believe that a functional organisation helps foster the long-term development of specialist expertise and reinforces accountability for risk management.
For the last two years, for instance, a new ‘safety and operational risk’ organisation (S&OR) has been providing an independent view of operational risk. This team is accountable for the overall risk management process and can, when necessary, intervene in, an even veto, all phases of BP’s operations.
Another significant aspect is that the performance-and-reward system at BP is now designed to reflect the fact that all personnel at BP - regardless of their actual job function - have a responsibility for safe operations.
Morrison went on to detail how BP’s leadership site inspections and formal audits have been sharpened: the executive leadership team visiting sites armed with an appreciation of the key issues as identified by the annual risk review process.
They can, therefore, then observe the team’s awareness and understanding of barrier integrity at the site in a more systematic way, he said.
“These fundamental changes were put in place to assure a deep, standardised, and verifiable approach to reducing risk across our global operations,” concluded Morrision. “So we are focusing with exceptional intensity on the barriers that stand between us and the risk we are managing.
“Not only the physical and the human barriers, but systems that sustain those barriers. It all starts with a pretty simple principle - to become more systematic in all that we do.”