Subsea saviour
8 Apr 2013
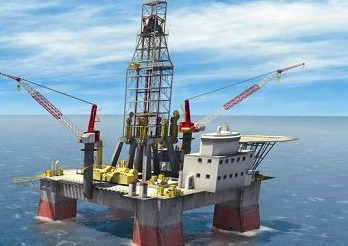
Much of the low-hanging fruit has already been picked. In future, offshore natural gas fields will be located ever further from land in deeper, colder and harsher environments.
This, of course, makes the cost of production higher and more risky. With energy at a premium, the oil & gas industry has been embracing more energy efficient processes to reach untapped reserves at the lowest costs.
In recent years, the sector has made inroads into advanced process operations and equipment, such as increased use of flare gas recovery systems and made use of more efficient pumps and compressor turbines. Developments such as the heat and power plant at the Mongstad refinery in Norway have also gone some way to improving the industry’s green credentials.
One particular energy efficient development is now gaining traction in the industry. Compressing gas on the seabed and sending it straight to shore - as an alternative to building an offshore platform – is seen as an ideal solution to tackling deeper gas fields at improving energy consumption.
The theory is straightforward. Gas reservoir pressure naturally falls over time, causing output to decline. To maintain and maximise recovery, pipeline pressure must be raised; the closer to the well the gas is compressed, the higher the efficiency.
While the concept of subsea gas compression is sound, progress has been slow. Hitherto, oil and gas companies have been happy to boost recovery rates by building new offshore platforms, retrofitting existing platforms with new compressors or merely plugging and abandoning gas fields no longer deemed economic.
Along with energy savings, subsea gas compression could save 30-40% over the cost of surface developments. This technology could ultimately eliminate the need for surface production facilitates and support gas production from reservoirs otherwise not seen as economically attractive.
But introducing subsea compression takes years of testing and qualification and few companies have been willing to shoulder the risk. Norwegian NOC Statoil and its partners are hoping to change this by investing nearly $2.7 billion to boost volumes from its Åsgard B platform, located 124 miles (200 kilometres) offshore in the Norwegian North Sea. The group claims that in doing this, it will be implementing energy efficiency processes that will help reduce costs and pave the way for others in the oil and gas industry to do the same.
Since the early 1990s, Statoil claims its processes have helped to reduce carbon dioxide emissions by approximately 40 million tons on the Norwegian continental shelf compared with a business-as-usual scenario. Now, the group is leading the way in energy efficiency by installing the world’s first subsea gas compression station. When completed in 2015, two 10 MW compressors placed near the wellheads of the Mikkel and Midgard reservoirs will boost recovery to the platform located 25 and 31 miles away respectively.
Statoil has chosen to implement subsea compression at these sites because it expects reservoir pressure will become too low in 2015 to avoid unstable flow to the Åsgard B platform. The subsea compression station, which will be installed in 250m depth, will measure 70m x 40m x 20m and weigh around 3,500 metric tonnes.
Production from the two fields will be routed to the compression station, which will have the capacity to compress 21 million cubic metres of gas per day. Statoil expects the compressor station to boost the pressure of the flow in the different lines by roughly three times; prolonging life of the fields by 15 years; enhancing gas and condensate recovery by 278 million barrels of oil equivalent; and improving reservoir recovery rates from the fields from 67% to 87% for Midgard and 52% to 67% for Mikkel.
Compressor technology
Early on in the project, Statoil decided that a wet gas centrifugal compressor was the most suitable technology. While a topside compressor is fed dry gas with extraneous material taken out, the subsea unit has to deal with wet gas containing condensate and natural gas liquids, and whatever else comes out of the well – like sand.
Following a vigorous testing process of various compressors, including Siemens’ ECO-II unit, Man Diesel & Turbo won a contract in 2011 from EPC contractor Aker to supply four single compressor units, each with a compressor frame (size RB 45) with integrated MAN motor, size M43.
MAN Turbo’s wet gas compressor unit is based on its HOFIM design, which was originally conceived for dry gas operations. A guiding principle for the modified design was simplification.
A high-speed motor is used, which means that no gears or couplings are necessary to connect it to the compressor shaft. The casing is hermetically sealed and process gas is used to cool the motor; the cooling gas is extracted from the process gas as it passes through the scrubber.
ABB is supplying the power distribution equipment. The electrical system will be able to transmit 15 megavolt-amperes and 189 hertz, enough to power over 10,000 homes, over a distance of 26 miles from onboard the Asgard A floating vessel off the northern coast of Norway.
Compared with a conventional compressor weighing around 82 metric tonnes, the units developed for Åsgard B are smaller, weighing around 50 metric tonnes, with a footprint 50-60% as big. The designs of the subsea compressor station is modular to facilitate retrieval of components and sub-systems, rather than the whole compressor train, in the event of a malfunction; Statoil’s goal is to have a five-year interval between regular maintenance.
The subsea compressor station will look much the same as that on an offshore platform, said Statoil. Arriving at the subsea compression station, the wellstream will pass through a scrubber which will separate the gas from the liquids.
Two of the compressor units will be installed on the seabed at any time. They will be incorporated in two separate trains operating in parallel, though when production starts to tail off, they could be put to work in series to maximize production.
The endgame
In parallel, Statoil is working on two other subsea compression projects. In conjunction with partner Petoro aims to boost recovery from Gullfaks South gas field from 62% to 74% via two 5 MW wet gas compressors; installation is also scheduled to be completed by the end of 2015.
Statoil is also responsible for the technology qualification for a $500m pilot project at Ormen Lange gas field, now owned by Shell. The project will feature GE Oil & Gas’ new Blue-C compressor, with installation on the seabed expected in 2019.
The stakes are high for Statoil. While these initial projects are aimed at refurbishing gas fields with declining production, the endgame is developing subsea compression stations for new gas fields in frontier locations.
Bjørn Kåre Viken, Senior VP, subsea and marine technology, said the Åsgard project is viewed as the first major stepping stone towards its ambition to build ‘subsea factories’ in challenging areas such as the Barents Sea and hit an ambitious production goal of to 2.5 billion barrels per day equivalent by 2020.
“The Åsgard project is crucial for us to reach another ambitious technology goal, the subsea factory,” said Viken. “Without it we won’t have the experience and courage to reach our subsea factory goal, which is key to success in Arctic areas or in deepwater areas like the Gulf of Mexico and Brazil.”
With hundreds if not thousands of stranded gas fields and new deepwater fields to be opened up, the energy and cost savings for manufacturers of subsea gas compression systems is enormous. Compressor manufacturers hope Statoil and other can prove the concept and open the door to a new, more energy efficient future.
Deep sea electrical power
Subsea gas compressors are an energy efficient solution for the oil and gas industry as they operate closer to the well. But powering them is such harsh conditions is a huge engineering challenge.
The overall power requirement for subsea gas compressors range from tens of kW to tens of MW. Researchers at GE Global Research Center have developed a novel power transmission and distribution concept: modular stacked direct current system (MSDC). The MSDC technology achieves the required DC transmission voltage by stacking a number of power converter building blocks in series, both on the shore and on the subsea field. According to the company, this could provide a cost effective and reliable solution to powering subsea gas compressors in formidable deep sea environment.
Downstream refining
Downstream refining requires huge amounts of energy. In the United States, for example, refining consumes more energy than any other sector of manufacturing. Some studies estimate that refineries spend 50% of operating costs on energy purchases.
According to a 2012 ‘Sustainable Energy for All’ report by Accenture, achievable targets for improving energy efficiency should be a top priority for most refinery managers. The report highlights that any solution that improves the conservation, recovery and use of heat will increase the refinery’s efficiency.
Techniques such as enhanced heat integration, increased automation, energy management systems, and the use of modern catalysts can all noted to improve the energy efficiency of a refinery. The report added that combined heat and power plants can generate twice as efficiently as the average power supplied by a local utility company and are key energy efficiency technologies in refineries.