Maintenance regimes can be a balancing act
8 May 2013
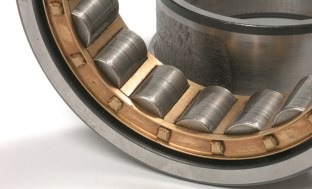
Patrick Raleigh asks industry expert about the impact of technology, business and skills trends on maintenance regimes.
While establishing an effective balance between reactive and planned maintenance is still a long-term goal for many UK process manufacturers, there are signs that companies are moving in the right direction.
The current economic climate is having a surprisingly helpful effect: forcing companies to take a more proactive approach to asset maintenance, believes Steve Dye, business development manager of Parker Kittiwake a supplier of condition monitoring equipment and predictive maintenance systems.
Reactive maintenance, notes Dye, can be expensive, so maintaining plant and equipment in line with manufacturer recommendations and the use of condition monitoring can generate significant cost efficiencies.
“Condition monitoring is no longer just about stopping equipment before catastrophic failure, but rather spotting problems at an early stage and implementing efficient preventative maintenance scheduling as part of a reliability-centered maintenance strategy,” he commented.
However, amid what he sees as a strong trend towards increased planned maintenance, Dye emphasises the continuing importance of reactive maintenance and for companies to be fully prepared for things going wrong.
Business matters often dictate the pace at which process companies adopt new maintenance technologies and practices.
“In most industries, financial pressures can create opportunities for change,” said Dye. “The usual attitude to condition monitoring is: when day rates are low, there’s no money for it. When day rates are high, people simply don’t care.”
But this mindset is changing, Dye noted: “Multiple mergers and acquisitions have created much larger companies. Engineers are being promoted up through the company and now occupy positions with significant corporate influence. They have the experience and understanding of condition monitoring to present a solid business case for its adoption.”
Another significant trend relates to the changing demands of operators who are pushing engineers harder than ever before to increase uptime and asking for proof that the equipment is ‘healthy’.
Engineers now have the experience and understanding of condition monitoring to be able to present a solid business case for its adoption
This is particularly relevant where the equipment is mission critical, as if this fails, the business cannot function effectively.
“With the spectre of downtime ever present, condition monitoring systems and oil analysis programmes are the first means of defence in diagnosing problems with critical plant machinery and equipment,” said Dye.
“And by ‘de-skilling’ technology, all maintenance professionals are empowered to make informed decisions quickly and with confidence,” he added.
Asked about whether effective maintenance should be more about people than technology, Dye replied that even with tools, such as on-line condition monitoring, the engineer still needs to be there to analyse the data and ensure the equipment is functioning as it should be.
The engineer, he noted, will be the one to make the decision to plan necessary downtime or to get the problem solved, where the data shows that something is not working well.
“Installing an easy-to-use proactive maintenance system motivates employees to take part and ensure several aspects of the business are running smoothly,” said Dye.
“Good results are important to everyone. Many organisations that have implemented proactive maintenance solutions have hired engineers in conjunction to ensure the installation is handled properly and can continue to manage the system.”
But, where critical plant machinery and equipment is concerned, the Parker Kittiwake manager sees a clear benefit in knowing what is going on at an exact point in time not just when the engineer can get to a machine for a routine, scheduled test and analysis.
“The condition monitoring arena has been influenced by a number of innovations,” he concluded. “These now allow engineers to [utilise] onsite and online testing; working in unison with offsite lab analysis to, ultimately, protect revenue for customers.”