Planning the journey
14 May 2013
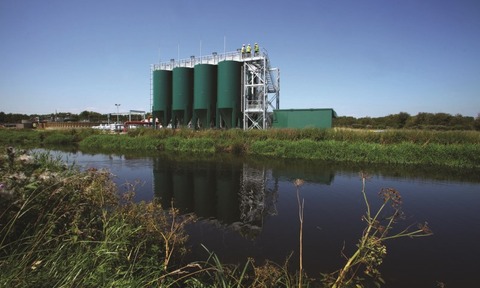
Patrick Raleigh reports on efforts at Southern Water to move the utility to a more planned maintenance regime.
While maintenance people might quite reasonably regard their activities as the most vital aspect of any process operation, this is not a good attitude to start out with on a journey to a planned maintenance regime.
As Bob Phillips, principal legislation engineer at Southern Water points out, even very good and regular maintenance will be ineffective if a company installs the wrong kit, or does not operate it correctly.
“If you try to work without one of these elements you are going to fail,” Phillips explained recently at the Maintec show in Birmingham. “It is not just about maintenance: it is about all three [aspects].”
Phillips was setting out the challenges faced by the utility in reducing its current heavy reliance on unplanned maintenance procedures an estimated 73% of the company’s maintenance activities is currently reactive.
A planned maintenance environment is more cost-effective for customers. Ofwat is looking for improvement…
Southern Water serves a large geographical area, stretching across Kent to Hampshire. The operation encompasses over 100 water supply works and over 400 wastewater treatment works, including 13,000 km of drinking water mains and 21,000 km of wastewater and rising mains.
The utility’s level of reliance on reactive maintenance is fairly standard throughout the water and wastewater industry, an issue that regulator Ofwat seems to be aware of.
“A planned maintenance environment is more cost-effective for customers,” Phillips noted. “Ofwat is looking for improvement in the balance between planned and reactive maintenance environment. We have to report on that to the regulator every year and are judged on that.”
Around three quarters of activities in the field are to do with reactive maintenance jobs, which most would regard as “not an ideal position to be in,” continued Phillips citing figures showing that a purely reactive approach worked out about three times more expensive than a reliability-centred maintenance (RCM) system.
Phillips also presented figures to show how a typical utility budget of £3.5 million could be reduced by almost a third by a modest shift in the maintenance approach moving from a profile of RCM 10%/Preventative 17%/Reactive 73%, to one of RCM 10%/Predictive 40%/ Preventative 30%/ Reactive 20%.
Interestingly, though, Phillips said he was not being guided by percentage figures for reactive versus planned maintenance.
“I don’t know if there is an ideal figure [for the percentage of planned maintenance], but I do know that as you start getting towards it, all the key performance indicators, such as unit cost of production, show when you are getting close.” To get there, though, companies first need to understand the performance of their asset base. This, said Phillips, requires gathering and managing huge amounts of data from across the operation.
“Again, if you use just one element of that data you will make the wrong decisions. You need to understand why the assets are performing in such a way,” said Phillips. As a simple example, he said, engineers could target a problematic pump and carry out more maintenance, on it, more regularly.
In the meantime, while the maintenance department at Southern Water clearly wants to move to a more planned maintenance approach this cannot happen overnight.
“This is where we have got stuck with the cycle,” he said. “When we reached 75% reactive we couldn¹t stop being reactive, because things are falling over and breaking. We are not doing it this way just because we like to.”
In recent years, this issue has led Southern Water to bring in more contractors in order to give the in-house teams more time to carry out predictive and preventative work.
The utility has around 250 in-house technicians working between mechanical, electrical and C&I. These are supported by contractors, some embedded within the company under service framework agreements. However, the move to outsource work has created some unexpected issues, which have led it to return some core work back in-house.
“Over the years, we have reduced our in-house resource. There have been some good drivers behind that: contractors, on the surface, present a good cost structure,” said Phillips.
But, he added, “we did lose some ‘ownership’ inside the company. So what might have been a good idea at the start of the contract is less so because of the hidden value we were getting out of the internal staff that we were not fully aware of.”
Moving forward, Southern Water is now engaging with people throughout the company, to develop an understanding of their requirements in moving to a more planned maintenance culture.
“There is a technical solution for everything, but the reality is that it is all down to individuals.” concluded Phillips. “Maintenance,” he added, “definitely, cannot be looked at in isolation: the entire organisation needs to understand that message.”