Growing case for CHP
10 Jul 2013
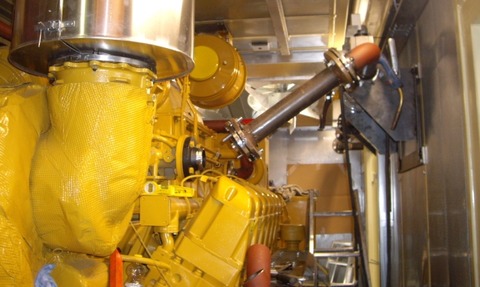
If carefully adopted, facilities for power generation and transfer of waste heat offer significant savings for plant operators.
Combined heat and power (CHP) systems are increasingly used in UK industrial plants, where the technology can reduce the amount of electricity purchased from the grid and capture and transfer useable heat that may otherwise be wasted.
While CHP technologies are gaining momentum, according to the Carbon Trust around 76% of the UK’s CHP electrical capacity is generated by just three industrial sectors chemicals (33%), oil refineries (32%), and paper and publishing and printing (10%). Rising energy costs, plus new regulatory drivers, however, point to a much broader adoption in the near future.
CHP technologies have been making the headlines recently as changes to the Government’s Climate Change Levy (CCL) took effect on 1 April this year, notes Nigel Thompson, sales manager at Finning Power Systems, a provider of both natural gas and biogas CHP technologies.
CHP installations should normally be sized to meet the base load consumption
“Previously, suppliers of electricity generated by ‘good quality’ CHP were exempt from CCL legislation, a tax on non-domestic supplies of electricity in the UK,” he explains. “The Government has now removed the existing exemption from CCL on input fuels, replacing it with a proposal that such fuel will be subject to a new tax called the carbon price support (CPS) tax.”
“For small and medium-sized businesses (SMEs) this is not all bad news as the CPS tax is waived on CHP plant with an output of less than 2MWe which could apply to up to 70% of all sites in the chemical and processing industries.”
“SMEs, in particular, are being encouraged by the Chemical Industries Association (CIA) to consider adopting CHP technologies,” he said. “The CIA identified that CHP could generate up to 49% of the potential savings available to SMEs through the implementation of energy-efficient measures, alongside other low, medium and longer term cost saving opportunities.”
A CHP system consists of a prime mover, such as an internal combustion gas engine to provide motive power, an electrical generator and a means of recovering heat, typically from the engine water jacket and exhaust.
A four-year payback
“Industrial sites will often use this heat generated to provide hot water or to heat the building, but in process applications, this heat can also be used during the manufacturing cycle,” said Thompson.
“Uses of the heat could include steam generation, medium pressure and low temperature hot water and even cooling water, reducing the need for separate boilers or other heat related equipment.”
As a general rule, Thompson said operators should expect payback within three to four years, depending on the difference between their gas and electricity supply prices. The higher the demand for power and heat, the greater the achievable savings.
For example, a 1200kWe CHP operating 24 hours a day and producing 1189kW of heat could save £125,000 per year. This is based on a 3.5 pence per unit cost for gas and a 10 pence per unit cost for electricity.
There are a number of factors that will affect return on investment, including the cost of bought-in gas and electricity from the utility provider, the demand for heat and whether this is continuous or cyclical.
The distance that the heat will have to travel to reach the process should also be accounted for, as any heat losses will mean that CHP station efficiency will be lowered.
Before commissioning a CHP package, processors should first carry out a site survey to ensure suitability and to make any necessary modifications to site infrastructure. Feasibility services, said Thompson, are available that include checking the gas supply and assessing the electrical connection for the CHP power element among others.
“CHP installations should normally be sized to meet the base load consumption,” said Thompson. “It is important that this is based on the demand profile during a full production year to account for peaks and troughs in output and that it includes an assessment of yearly gas and electricity bills, based on half-hourly measurements of heat and power consumption.”
Sizing it up
This will enable a heat-to-power ratio to be calculated. For example, a chemicals’ site may require 500 kW of heat and 500 kW of electricity to operate to maximum production output. In a conventional installation, the heat will be provided by a series of gas boilers and the electricity purchased directly from the grid.
In contrast, a CHP installation may produce 400 KWe of heat and electricity respectively from one natural gas fuel source, meaning that the operator can significantly reduce its utility costs, importing only the additional power it needs above the 400kWe base.
To achieve the power-to-heat ratio necessary, Thompson said it can sometimes be more economic “to oversize the package from a power perspective to meet the site’s heat demand and sell any excess electricity back to the grid at a profit.”
“In other applications, it can be more profitable to size to the building’s lowest average heat demand, with the CHP system acting as the lead boiler and backup boilers picking up additional heat requirements.”