Keeping it clean
2 Oct 2013
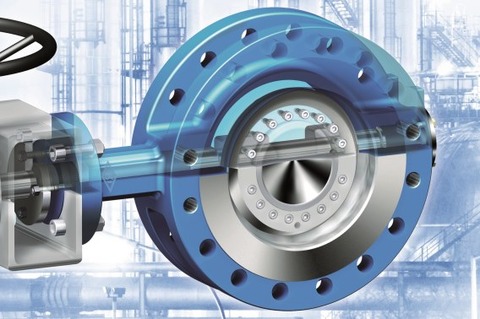
Constantly rising hygiene standards in the food and pharmaceutical sectors are driving demand for new and improved pumps and valves.
Of the many industry sectors that are driving the growth in demands for pumps, process manufacturing in food, beverage and healthcare products have been identified as key players.
As standards of living improve and populations grow, the pressure is on manufacturers to produce larger volumes of processed foodstuffs and healthcare products more economically and to higher standards of quality.
As governments, international and national quality assurance organisations require ingredient and processing traceability audits, the onus is on manufacturers to design and provide hygienic process equipment that conforms to all relevant quality standards and legislation.
EHEDG is a consortium of equipment manufacturers, food industries, research institutes as well as public health authorities
The US Food and Drug Administration (FDA) has been in existence for over a century and is recognised worldwide as the benchmark for hygiene standards in processing plant and equipment.
The European Hygiene Engineering Design Group (EHEDG) is a relatively new organisation having been established as recently as 1989. In its own words, EHEDG is a consortium of equipment manufacturers, food industries, research institutes as well as public health authorities and was founded with the aim to promote hygiene during the processing and packing of products.
In a relatively short time, it has become widely adopted by pump and valve manufacturers, amongst others, and is having a significant impact when equipment is being specified.
The principal goal is the promotion of safe food by improving hygienic engineering and design in all aspects of food manufacture.
EHEDG actively supports European legislation, which requires that the handling, preparation, processing and packaging of food is done hygienically using hygienic machinery in hygienic premises (EC Directive 2006/42/EC for Machinery EN 1672-2 and EN ISO 14159 Hygiene Requirement).
The United States Pharmacopoeia (USP) is an independent organisation that established a set of standards to ensure the quality of medicines and health care technologies.
Many device manufacturers continue to use the USP Class VI test to determine biocompatibility, although ISO 10993 is superseding USP as the reference standard in measuring material biocompatibility.
Hygienic design
The design of process equipment for hygienic applications can have a positive impact on reducing the risks of contaminating food during production and contribute to the quality of the finished product.
If hygiene has not been taken into account at the design stage, then the possibility for the build up of bacteria is enhanced and cleaning diminished. Furthermore, bacteria can survive and multiply in crevices and dead areas.
The poor hygienic design of components used in food, beverage and pharmaceuticals processing can therefore be instrumental in finished product contamination or reduced shelf-life.
Hygienic requirements are typically addressed at the design and development stages of components as this will remove the need to make modifications or upgrades later in the development cycle, or after equipment has entered service.
Products manufactured with equipment meeting EU legislation and regulations e.g. EU Machinery Directive 98/37/ EEC are on the increase.
However, the CE mark, which is granted on the basis of the EU Machinery Directive, does fall short in terms of hygiene, so even if the manufacturer meets the additional hygiene requirements formulated in the European Standard EN1672-2, the microbiological safety of the foods produced cannot be guaranteed.
Legislation does impose strict requirements in technical specifications for the hygienic design, construction and installation of process equipment. Similarly there is a need for criteria and procedures for the testing, assessment and certification of process equipment to formally certify that the equipment functions in conformity with predefined requirements.
For pump and valve manufacturers it is important to have the design tested against given requirements. The hygienic design of equipment is subsequently assessed and the cleanability of the equipment can be tested.
Such tests identify weak points in the hygienic design, including places where product residues may accumulate or where bacteria may grow. The various guidelines and test methods for hygienic design, construction and installation developed by working groups within the EHEDG meet these requirements.
Valve Development
Valve manufacturer ARI-Armaturen provides a good example of this approach to the design process. When it came to the development of a triple offset process valve, ARI-Armaturen applied all its resources to the valve’s design and production.
The recently introduced ZETRIX brings together the benefits of a metal-seated process valve with all the advantages of a butterfly design. The triple offset principle guarantees a permanently tight seal, conforming to leakage rate A in accordance with DIN EN 12266-1. It can also be used as an isolation and control valve, making it extremely versatile.
According to ARI-Armaturen, the design and development of the ZETRIX involved optimising the very latest generation of tools and modern manufacturing technologies.
Included in these tools was Finite Element Analysis (FEA), a numerical calculation technique that simulates the stresses and their distribution occurring in the valve. Minimal stress on all features of a process valve greatly improves valve longevity and safety.
This testing and simulation method resulted in development of a valve of the required strength at pressure load levels up to PN40 in combination with optimal weight design and flow-friendly shape.
The flow values at different opening angles were measured in an accredited testing laboratory using Contact Angle Calculations (CAC). The resulting curves were used to determine the control characteristic of the valve.
ARI sizing software allowed the contact angle at the perimeter of the valve seat to be visualised and the peripheral closing angle was optimised to ensure that the valve opens and closes without sticking and without friction.
The twofold objective of uniform flow and high flow capacity was realised from Flow Simulations using special flow software. The software simulations enabled the flow velocity, flow direction and pressure distribution to be visualised. As a result of the optimised ZETRIX geometry, turbulences are reduced to a minimum and pressure loss prevented.
Pump Technologies
The pump technologies that are prominent within food, beverage and personal healthcare processing are rotary lobe, rotary piston, reciprocating positive displacement, progressing cavity, peristaltic hose and air-operated double diaphragm designs.
The common factor in all these types is their gentle pumping action, cleanability and ability to handle media containing solids. Rotary lobe pumps employ timing gears which eliminate contact between the rotors and enables them to handle non-lubricating fluids.
Providing low shear and gentle handling of the liquid, thereby minimising product degradation, rotary lobe pumps are also easy to clean in place (CIP) or strip clean between operations for batching applications.
The factors affecting the choice of a metering or dosing pump as opposed to other types of pump are normally associated with precision
A rotary piston pump, whilst offering many of the benefits of the rotary lobe pump, is of the external circumferential piston (ECP) type. In this design the arc-shaped rotary pistons, or rotor wings, travel in annular-shaped cylinders machined in the pump body.
The resulting long sealing path reduces slippage and produces a smooth product flow without destructive pulses or pressure peaks and without the need for valves or complex parts.
Because the rotors produce a scooping action, they do not squeeze and compact the medium being pumped. This pump type combines a very gentle, pulse-free pumping action with the high suction capacity necessary for allowing thick mixes to be drawn into the pump without any separation of ingredients.
The reciprocating positive displacement process pump is a very different technology and is a proven method for the in-line proportioning and dosing of liquids and provides the highest levels of accuracy and repeatability available.
The factors affecting the choice of a metering or dosing pump as opposed to other types of pump are normally associated with precision over a range of flows and the fact that the capacity is not influenced by pressure fluctuations within the process.
The metering pump is very adaptable and due to its design is ideal for the continuous, in-phase metering of single or multiple liquid systems at varying rates. Where media needs to be moved at low velocities, progressing
cavity pumps provide low shear characteristics.
Employing a single rotor to move fluids in a continuous flow, the performance of progressing cavity pumps is largely down to the geometry of the rotor and the stator in which it turns.
The materials from which these two elements are manufactured need to be matched to the pumped media in which they come into contact. In order to achieve life-cycle costing goals, the rotor and stator need to offer high levels of resistance to aggressive fluids, which brings into play rotor geometry and material specification.
The food and pharmaceuticals processing industries are large users of air-operated double diaphragm (AODD) positive displacement pumps as the number of applications for them is simply enormous.
This is because the AODD pump can transfer almost anything. The absence of close fitting parts allows solids to pass through the pump without harm, whilst abrasive and viscous products can be pumped without any damage to the fluid characteristics.
Dynamic components
AODD pumps use compressed air to act upon the diaphragm and draw the liquid media into the pumping chamber and then eject it, so there are no rotary parts involved.
When running, the dynamic components that come into contact with the fluid are the two diaphragms which are connected by a common shaft, the two inlet valve balls and the two discharge valve balls.
The diaphragms act as a separation membrane between the compressed air supply and the fluid. Driving the diaphragms with compressed air, rather than the shaft, balances the load on the diaphragm which removes mechanical stress and therefore extends diaphragm life.
The valve balls open and close on the valve seats to direct the flow. Over the past half century the AODD pump has evolved to become a unique solution for the complex fluid transfer needs encountered within the biopharmaceuticals industry.
Because of the critical nature of some processes, inefficient product transfer methods such as manual rolling carts with containers, purging tanks to evacuate product or manual gravity feeding transfers have been common.
However, purpose-designed AODD pumps for this industry now allow further use of pumped transfer processes approaching the degree already encountered in the general chemical/ industrial sectors.
With the innovations and enhancements for the ultra-sanitary conditions needed by the pharmaceutical industry, the AODD pump is now an attractive option for many fluid transfer duties.
The growing demand for pumps and valves that are suitable for sanitary and hygienic applications is encouraging many manufacturers to develop new products.
This year companies that have introduced new products include Grundfos, seepex, Waukesha Cherry Burrell, Rotork, Crane- Pharma, Lutz, ARI-Armaturen, Watson-Marlow and Wilden, to name just a few. With the global
market for pumps and valves predicted to keep rising over the next few years, the opportunities for further product development are clearly evident.