Sea Change
22 Apr 2015
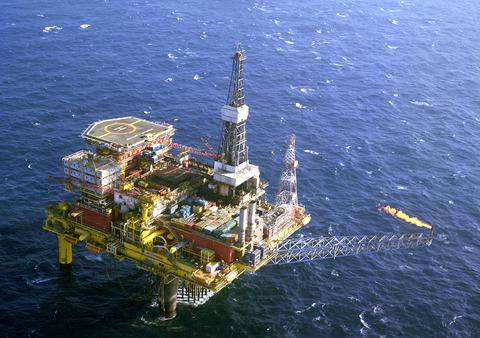
Plummeting oil prices have added further impetus to the Wood Review’s call for greater production efficiency in the North Sea.
Over the past couple of years it has become a recurring theme of chancellor George Osborne’s budget to announce some kind of new tax deal for North Sea oil & gas.
First came brownfield allowances, and last year the promise of a single basin-wide Investment Allowance that is designed to reduce the effective tax rate for companies investing heavily in the UK Continental Shelf (UKCS).
Last month, in his final budget of this Parliament, Osborne saved his best for last, cutting the supplementary tax rate from 30% to 20%.
Osborne said he was making the cut - five times a 2% cut to the supplementary rate that he only announced in the autumn statement last year - because the fall in the oil price to $50 per barrel posed a “pressing danger” to the future of the North Sea oil and gas industry.
In reality, the North Sea has been in danger for some time, and the current low oil prices are only serving to make the high cost of exploration and production in the mature region seem even more unsustainable than they already appeared.
In his government-commissioned review of the industry last year, Sir Ian Wood set out the stark reality over production levels: in the three years prior to 2014, the North Sea’s output fell by 38%. While some early figures suggest this decline may have bottomed out in 2014 and in coming years production could grow as new fields come on line, one fact that hasn’t changed is the poor average level of production efficiency.
Efficiency across all North Sea fields has plummeted from 80% in 2004 to just 60% in 2013. In other words, for every 100 barrels of production capacity that a platform has, it is, on average, only producing 60 barrels.
Wood said there was an urgent need to return production efficiency to 70% as soon as possible, and in the medium to longer term bring efficiency back up to 80%.
The difficulty is that the majority of production in the North Sea is coming from assets built in the late 1970s and early 1980s that are coming to (if not already passed) the end of their design life.
Battling breakdowns
Ageing equipment has the nasty habit of breaking down: the Wood Review revealed that half of all production losses are as a result of unplanned production outages.
It goes on to suggest that more could be done to prevent these events by improving equipment monitoring.
However, according to those that provide equipment monitoring services and technology, taking such a step will require a sea change in North Sea operators’ attitude to maintenance.
“The oil industry is very conservative over the techniques it adopts,” says ABB Consulting Oil Gas & Chemical manager Philip Lawson.
“Typically, a time-based maintenance regime is used and people are very familiar with that. However, the reality is that with this approach you have to perform intrusive maintenance.”
Under time-based maintenance approaches, inspection of equipment will be scheduled on a periodic basis, with each inspection and replacement of equipment usually requiring a costly shutdown of production.
In addition, given that half of all production losses are due to unplanned outages, it suggests that the time-based approach rarely prioritises maintenance to focus on the equipment closest to failure.
Moving from time-based to condition-based lowers the costs of maintenance as the personnel required to assess the data can do so remotely
ABB Consulting Oil Gas & Chemical manager Philip Lawson
What is required, says Lawson, is a shift to condition-based maintenance. In this approach various sensing technology is used to provide data on how a piece of equipment is performing.
This information can then be used to prioritise maintenance for those pieces of equipment that most need it, when they need it.
“Moving from time-based to condition-based lowers the costs of maintenance as the personnel required to assess the data can do so remotely - they don’t need to be offshore,” says Lawson.
“It also increases efficiency as it allows you to run for longer without stoppages. However, as I said it is a very conservative industry and installing additional equipment to understand the health of the asset - many operators simply say ‘it’s not for us just yet’.”
Given the Wood Review’s call for an urgent return to 70% efficiency, how long this will continue to be operators’ attitude remains to be seen.
As well as considering technology such as sensors that can help improve efficiency, Mike Whittaker, senior manager at Emerson Process Management’s new Reliability Consulting business, says operators also need to consider in more detail what they actually do when carrying out a shutdown or turnaround (TARs) for maintenance and/or improvement.
“In the offshore world the major challenge they face is the logistics of getting maintenance work done,” says Whittaker.
“Companies often seem to get planning and scheduling mixed up. They talk about planning but what they actually mean is that they are simply scheduling when maintenance work will get done. True planning of TARs allows the operators to optimise the activities they will be undertaking, and do things like making sure all the equipment necessary for the work will be available at the time.”
While unplanned outages from equipment failures and planned TARs outages represent the main factors damaging production efficiency, another issue that can be addressed with technology is slugging.
Honeywell Process Solutions upstream oil & gas marketing leader Paul Bonner says that slugs at the riser are becoming increasingly common as more and more fields opt for subsea completion of wells, transferring oil and gas over long distances for processing either onshore or at another platform or a floating production storage and offloading (FPSO) vessel.
“When you move oil and gas over long distances, you get slugs of seawater coming up to the riser along with the oil and gas,” says Bonner.
“This can create a big burp of liquid that fills up the separator, and the system will automatically close the chokes on the wells to back off production as it thinks the well is producing over a safe limit. When you cut back production like that you have lost those barrels for that period of time forever.”
Using pressure and level measurement technology, says Bonner, it is possible to predict whether a slug can be contained within the separator without the need to back off production, or to do so by only a minimal amount.
Low oil prices and high production costs will continue to push production efficiency to the top of the agenda over the coming year: it remains to be seen how long operators can be conservative and resistant to new techniques and technology.