What goes around
24 Jun 2015
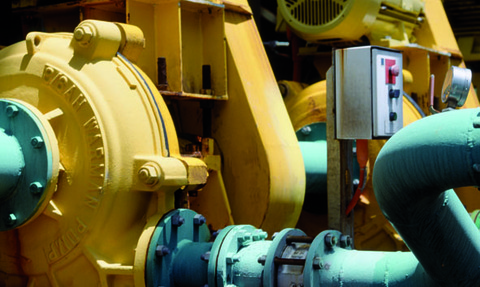
Prevention is far better than a cure when it comes to safeguarding critical rotating equipment.
As the backbone of many processes, rotating equipment is charged with keeping the modern-day process plant in business. This means a minor breakdown of a piece of equipment such as a compressor, pump or turbine can cost a company dearly. While investing wisely in the right predictive monitoring tools can help to keep things running smoothly, knowing where to place your resources is equally important.
Jean-Luc Goutagny, director of reliability solutions at Emerson Process Management, says there is a hierarchy for the different levels of condition monitoring equipment in process plants that enables plant managers to make optimum use of their resources.
Prediction and diagnostics allow you to anticipate the damage and catch it before something happens, and about 60% of this is vibration monitoring
Emerson Process Management’s Jean-Luc Goutagny
At the top of the condition monitoring pyramid is critical high-speed equipment such as compressors and steam turbines which are highly monitored because they are so important to the process and safety.
“These machines need both protection and predictive technologies,” says Goutagny. “Prediction and diagnostics allow you to anticipate the damage and catch it before something happens, and about 60% of this is vibration monitoring.”
“For smaller, less critical equipment, either wireless or wired technologies are more commonly applied. And further down the chain, even less critical equipment is generally monitored off-line using portable data collectors,” he says. “From here, data may only be collected every two weeks and analysed. Then at the final layer is equipment that is not worth monitoring. This is either redundant or very low criticality, so when it fails the maintenance staff just replace it.”
Digging into the data
Goutagny says larger companies such as refineries, are more or less covered when it comes to condition monitoring equipment.
“Their issue is how to extract real value from the data generated by condition monitoring equipment. They have a lot of data but don’t always know how to ask for the right information or have the knowledge to analyse it. They may have a lot of data, but they need tools to filter and extract the right information to get this to the right people,” he says.
Emerson recently acquired an asset reliability consulting company called Management Resources Group, to boost its credentials in this area. The tools can also help to shine a spotlight on how maintenance can impact the bottom line, says Goutagny.
“Those working in maintenance can become a little bit isolated and are not always certain of the value they bring to management. That means they sometimes have issues with allocation of budgets because they are not in a position to justify themselves,” he says.
“By connecting condition management with Enterprise Resource Planning (ERP) they have some key performance indicators that show the value of these kinds of solutions.”
Rolling bearing manufacturer, Schaeffler, supplies a wide range of products for monitoring rotating equipment, from lubrication sensors to online vibration monitoring systems.
By carefully analysing the measurement data from condition monitoring systems, it is possible to detect an early deterioration in a machine’s condition, says Ian Pledger, an industrial aftermarket field service engineer at Schaeffler UK.
“Some plant operators may already know what the problems are likely to be with their rotating equipment, and just need some help to monitor them. For others, their machines fail for reasons they don’t understand.”
Condition monitoring is a mature technology that is well suited to applications such as pumps, fans and electric motors, says Pledger.
“Because we apply vibration to ensure fans are running at a reasonable speed, we can be very specific about what sorts of problems they are having. This can also allow for a root cause analysis, if you wish to take it that far.”
Some companies want access to more data than others, he adds. “They may just want to know when they should change a fan, and then apply alarms to it or they may want to dig down into the data to observe time signals and develop a diagnosis and prognosis, and an action plan to resolve those problems.”
Industry 4.0 is all about making machinery a bit smarter than it currently is, says Pledger. The resulting machines and products will be more capable of independently diagnosing their condition and maintenance requirements in the future.
“This would mean machines could indicate when they are in need of lubrication or a bearing change, based on feedback from sensors on the machines.”
To further this cause, Schaeffler has developed the FAG SmartCheck, which is an online system that provides information on the condition of machine components alongside additional parameters such as torque. The device forms part of the control system for the machine and is an integral part of the monitoring process.
“The idea was to make it user friendly so that it could be used by operators without too much knowledge of condition monitoring,” he says. “You can set it up to learn current conditions and it will create alarm levels that are completely suitable for that particular application.”
On the assumption everything is in good working order then it is almost completely autonomous, he says.
“It just gets on with the job and waits until normal operating conditions change and one of the alarms is breached.”
A wider initiative that Schaeffler has recently become involved with is Mitsubishi Electric Europe’s e-F@ctory Alliance.
Automated protection
The partnership combines the Mitsubishi Electric control unit with Schaeffler’s FAG SmartCheck as a pre-configured condition monitoring solution, with an automated link from the manufacturing level through to the control level.
Unlike alternative monitoring concepts that typically measure values such as temperature, pressure and operating hours, FAG SmartCheck provides additional vibration-based parameters, Pledger says.
The data can also be sent via Ethernet to other data receivers, such as the automation control units of other manufacturers or database-supported receivers, such as SCADA or Manufacturing Execution Systems (MES).
Sensonics supplies condition monitoring equipment for rotating plant equipment, and a key market is the oil processing industry says Russell King, managing director of Sensonics.
On the protection side it supplies monitoring equipment in combination with vibration sensors to enable safe shutdown of the plant in the event of excessive vibration recorded on the equipment shaft or bearing.
“These measurements are the most common, however, we do also supply both speed and thrust bearing wear protection systems on similar machinery as required,” he says.
“Our portable vibration equipment is utilised as a maintenance tool by site staff to look for trends in vibration as part of a preventative maintenance routine.”
Sensonics also supplies overspeed protection solutions for the power generation industry where failure of the turbine or pump speed governing system can lead to rotor damage with expensive consequences.
“Independent speed monitoring and protection is therefore an essential requirement to minimise these risks as far as practicable,” says King.
“Over the past several years the machinery directive has forced end users to look at suitable protective measures which may involve monitoring vibration or utilise an independent speed monitoring system,” he adds.
Continuous protection and monitoring is also becoming an essential requirement for reducing energy consumption and eliminating downtime for all companies.
Typically, however, the higher cost of more sophisticated protection systems can be difficult to justify for smaller machinery operating on less critical applications, even when there is a requirement for monitoring.
For this market, King says Sensonics developed its DN26 G3 machinery protection monitor as a more cost-effective solution for smaller plant equipment such as, pumps, fans, motors, centrifuges, turbines, or any item of small to medium industrial machinery.
Wireless technology is also helping to bring adoption costs down across the board, but is still being held back in industry due to a “perceived lack of reliability and potential security issues,” says King.
Another interesting development he has observed is the movement of data processing into the sensor.
“This lowers cost and provides the end user with processed data. Intelligent sensors are the way forward offering long battery life and wireless communications. Once established, this will open up a currently untapped market,” he says.