A sense of danger
5 Aug 2015
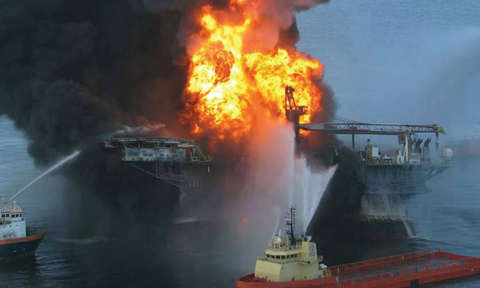
Can a new generation of detection devices mitigate the risk of catastrophic gas leaks within the process sector?
A Black Swan event is the most feared of all industrial disasters. Striking out of the blue, these highly improbable, catastrophic events are often the result of a whole chain of safety failings that coincide with unanticipated and deadly force.
In 2010, BP’s Deepwater Horizon oil rig claimed the title when high-pressure methane gas from the well rose to the drilling rig, igniting and destroying the platform. It claimed the lives of 11 workers and triggered the largest accidental oil spill in history.
It appears that manual forms of detection by visual means are the common form of detection when the four main automatic types fail, followed closely by sound and smell
Heath and Safety Executive
Disasters such as this have given industrial safety more prominence in the public consciousness, and made it a top priority at plants both new and old, says ARC Advisory Group senior analyst, Inderpreet Shoker. Many governments have now begun imposing heavy fines to push corporations toward safe practices. BP had to pay $4.5 billion (£2.9 billion) in fines and pleaded guilty to 14 criminal charges related to the Deepwater rig explosion.
“This has spurred demand for both safety systems and safety instrumentation like toxic and combustible gas detectors, which are the frontline for defense against dangerous emissions of toxic and combustible gases,” says Shoker. The reasoning is that advanced functionality in detection devices can help to mitigate some industrial risk factors.
“Users want features like wireless technology, remote monitoring, and data logging,” she adds. Remote monitoring helps end users effectively monitor challenging environments where detection is difficult.
Shoker says it allows real-time transmission of critical information to safety operators for a more effective response in an emergency. There is also an increasing requirement to archive toxic gas emissions data and alarms, both to meet regulatory requirements and fend off potential litigation by plant employees, she says.
“This is fuelling demand for detectors that incorporate data logging and management capabilities and use digital communication protocols,” says Shoker.
“The higher price of these smart detectors minimises the decline in average sales price while increasing total revenues. Wireless technology not only allows users to connect field devices to their systems, but can also help justify the replacement of older detectors with smart wireless devices.”
In an effort to mitigate risk and avoid heavy fines, many companies are also choosing to diversify their detector portfolio, she says (see box below).
Many gas detection technologies are available and Shoker says that in a “complex hazardous environment, one single technology may not offer [a high enough] level of assurance regarding safety”.
Gas is the most common form of process release, so it would be reasonable to assume that gas detectors should be the main detector type, says the Health and Safety Executive (HSE) in a report on offshore hydrocarbon releases dated between 2001-2008.
“However, it appears that gas detectors fail to spot a large proportion of releases, which in turn are detected by other means,” says the report. The issue is that poor detection systems may not sense smaller releases, says the HSE, which, when given the chance, can escalate into much more serious releases resulting in potential loss of life.
“It appears that manual forms of detection by visual means are the common form of detection when the four main automatic types fail, followed closely by sound and smell,” says the report. “A significant proportion of releases may be discovered by chance, especially if there happens to be personnel in the vicinity of a release.”
Loss of life
Sometimes this approach can prove fatal. Even though the hazards associated with CO2 in the brewing industry are well known, people working in this field are still dying needlessly, says Chris Wilson, a senior support engineer at Crowco.
Because the gas is heavier than air, it collects at the bottom of containers and confined spaces such as tanks and cellars commonly found in the brewing industry, claiming the lives of two workers at the same German brewery in separate incidents during 2013.
In the first incident, the owner was found dead with his head and torso in a beer mixing tank after being overcome by CO2, says Wilson. Some months later, a worker was found dead in a pressure tank used to recirculate wheat beer.
“He had probably forgotten to fit a yeast plug and had leaned into the tank – which was already pressurised with CO2 – to fit one,” says Wilson. “Both these accidents demonstrate the extremely hazardous nature of CO2 and how quickly one can be overcome by its deadly properties.”
Both portable and fixed CO2 detectors can be used for CO2 monitoring in breweries, he says. “Then, if a detector reads a dangerous CO2 level, extractor fans are automatically triggered and sirens or visual beacons can also be activated to warn workers to vacate the area.”
However, confined space work in the brewing industry often takes place in more restricted areas like fermentation tanks where fixed detectors cannot be installed, and this is where compact portable units become necessary, he says.
“There is a real trend towards multiple detection methods being used on-site,” says Louise Early, strategic industry manager at Crowcon.
This gives greater awareness of potential risks and better coverage, especially in the process industries where the complexity of the plants can make detection more challenging. “There are multiple ways a gas hazard can be recognised – where a particular type of gas is used or introduced into a process,” she says.
Crowcon, which supplies both fixed and portable gas detectors for industrial environments, has a wide client base, including food and beverages, and the steel industry. Different gases are often associated with different industries, says Early.
“Across our key industries there are potentially hundreds of different gases, each in a different environment, with different background levels,” she says. “There are two key things to look at in a new application. We do look at the type of gas to be detected but also at how the product is going to be used because its environment will have a large impact on which solution is most suitable.
“This is all about understanding our customers’ needs rather than recommending a broad brush solution.” Often, where a range of diverse hazards exist, a combination of both portable and fixed gas detection is needed, says Kevin Honner, a portable gas detection specialist at Dräger.
“Confined space entry is a key area of concern for companies working in the process industry as the danger of a hazardous gas occurring is always present,” he says. The HSE recently revised its regulations on confined space entry to reinforce the importance of calibrating equipment to the right levels before work takes place.
“It goes without saying that an employee cannot be placed in a situation where the risk of death or serious injury could occur,” says Honner. “Therefore, purchasing portable gas detection – while not foreconomic benefit – is vital for protection.”
The result is that calibration of safety equipment plays an important role in the industry today. “With some of the harsh conditions faced day-to-day, along with general wear and tear; gas detection units can be subjected to shock, sudden temperature changes, dust and other elements,” he says.
“Therefore to remain effective, bump-testing is a daily essential.” The company has also developed a communications system called the Dräger X-zone Com, which allows users to track gas detection levels outside the areas being monitored.
“Time, place and gas concentration levels are the most important data in the event of a gas leak and in an emergency situation, every second counts,” says Honner. In some industries, such as oil & gas, simply detecting whether a gas is present is not enough.
Where there is risk of explosion, operators need to know in absolute terms what is in there, and gas analysers fulfil this role.
Volatile compounds
ABB manufactures a wide range of gas analysers used for monitoring of emissions to atmosphere or the concentration of gas components in a particular process stream, says John Kelly, engineering procurement and construction (EPC) sector sales manager for ABB Measurement and Analytics.
Some operators need to know the exact amount of a component in a process stream so they can either reduce volatile compounds or make sure they will not go into an explosive state,” he says. “Because of the environments in which we operate, most of our process equipment needs to have some level of ATEX certification.”
ABB’s business falls into two key areas: process measurement for control purposes, and the rapidly expanding area of emissions monitoring for certain prescribed compounds where there are legal controls in place. “Regulation of sulphur content in fuel has become stricter in recent years, and we are also seeing growth in the development of biofuel manufacturing and verification to meet industry specifications and improve fuel efficiency,” says Kelly.
ABB recently supplied new gas analysers to Enviropower, a waste to energy plant in West Sussex. The electricity plant has a 5MW generating capacity, burning around 60,000 tonnes a year of biomass fuel, and uses an ABB ACF-NT multi-gas analyser on each of its two combustion lines.
All emissions data is sent to a reporting system, allowing it to prove that it is meeting the requirements of the Environment Agency. “Because our operation is permit-based, we have to meet certain criteria,” says the plant’s general manager, Mick Adams.
“One of these is the use of equipment that complies with the requirements of the Environment Agency’s MCERTS standards.” The ACF-NT emission and process monitoring analyser uses FTIR technology to provide offers continuous, quantitative and selective measurement of numerous gasses, including HCl, HF, H2O, CO, CO2, SO2, NOX, NH3, N2O, O2, TOC and NMHC (non-methane hydrocarbons).
“Our permit specifies a minimum oxygen content of 11%, which will shortly reduce to 6%, so it was important that the analysers had the flexibility to adapt to changing regulations,” says Adams.
The new wave
In a complex hazardous environment, one single technology may not offer a high level of assurance regarding safety, says Inderpreet Shoker, a senior analyst at the ARC Advisory Group.
Although conventional gas detection technologies such as catalytic bead, infrared point, and electrochemical have evolved over time, Shoker says open-path, ultrasonic, and gas imaging are newer technologies that are gaining wider acceptance as complementary solutions.
“By diversifying, shortcomings of one type of technology are overcome by the strengths of other ones, to reduce the chances of undetected leaks,” she says. Open path detectors These are used for leak detection for flammable gases in the oil & gas, petrochemical, mining and water & wastewater industries. Infrared and hyperspectral cameras can visualise various toxic and combustible gases to produce a picture of the scanned area in real-time, and are well suited to detection of various types of volatile organic compounds (VOCs).
“The technology has improved tremendously over the years and the latest versions of the detectors are immune to interference from sunlight, rain, fog, or snow,” says Shoker. Ultrasonic gas detectors Their ability to detect hydrocarbons makes them an attractive choice for the oil & gas industry, says Shoker.
An ultrasonic detector detects gas leaks by sensing the ultrasonic ‘noise’ produced by leaking gas. The detector uses acoustic sensors to continuously monitor the ultrasound noise level and generates an alarm upon detecting a deviation from normal ultrasonic sound level. Although these detectors do not measure gas concentrations, they can determine the rate of leakage, and work effectively in outdoor environments.
Infrared and Hyperspectral Imaging Cameras Infrared and hyperspectral cameras can visualise various toxic and combustible gases to produce a picture of the scanned area in real time, says Shoker. Hyperspectral imaging cameras can capture the complete spectral image of all objects within their field of view. Once spectral libraries are established, the cameras can also colour render the image to highlight the presence of specific material or gas, making it easier to spot any unusual material in the field of view.
TDL takes the spotlight
Mettler-Toledo’s GPro 500 TDL series recently received the 2014 Global Frost & Sullivan Award for Competitive Strategy Innovation & Leadership. Based on its recent analysis of the process tunable diode laser (TDL) analysers market, Frost & Sullivan found that the GPro 500 had an original design that was adaptable to almost any kind of process.
The series comprises four separate products for the measurement of oxygen, carbon monoxide, carbon dioxide, and moisture. “Mettler-Toledo stands out for its ability to integrate unique and standout features into its product line,” says Frost & Sullivan research analyst Janani Balasundar.
“Unlike competing solutions, the GPro 500 TDL series is compact and lightweight and, therefore, easy to install.” Mettler-Toledo has a track record in analytical measurement of pH levels in liquids, and decided to enter the TDL market to provide a broader service for its customers, says Jean-Nic Adami, head of gas process analytics at Mettler-Toledo.
“For users, gas analysis is so high up on the safety ladder that these are some of most critical measurements they make,” he says. “If, for example, oxygen measurements are too high, they may blow up a plant, so there is great motivation to find the best possible solution and strategy.”
Often oxygen is the only part of an explosive situation you can control, and for this reason, it is the most measured gas within explosive environments, says Adami. As a single gas measurement solution, TDL is becoming a valid alternative to paramagnetic, zirconia oxide and nondispersive infrared detector (NDIR) technologies.
“Some instruments need to be pampered and maintained, but TDLs are not like this,” he says. “They can run for a very long time without calibration. We have also found many ways to adapt TDL technology in the plant meaning you can measure where no TDK could measure before.”
A toxic brew
Carbon dioxide (CO2) is a by-product of the fermentation process, and can create a substantial hazard within the brewing industry. With a density that is heavier than air it collects in small toxic pockets low on the floor and can build up in confined spaces in and around the brewing process.
Two UK breweries were recently seeking a CO2 gas detection system, and approached A1-cbiss based on the company’s experience working within the brewing industry. During an external air monitoring survey on the sites, certain areas were identified as having (or potentially having) elevated levels of CO2 and required modification to remove the problem for health and safety reasons.
The breweries selected A1-cbiss to supply and install a full CO2 monitoring system to cover all site processes. The project installation has three phases, and is planned over a three-year period. The A1-cbiss proposal consists of a fixed gas detection system specified to provide visual warnings, communication to extraction or ventilation systems once alarm levels are reached, and integration to data acquisition and reporting software.
Each detection zone provides two alarm levels with sufficient outputs from the gas detection system to interface with the alarm beacons/klaxons providing internal alarm notification as well as notification at each entrance to the zone, as a warning to workers.
CDAS data acquisition & reporting software will be integrated on a local PC or into SCADA. Stage one of the installation has already been successfully completed, and covers all the areas within the packaging cell, and cold yeast storage room, says A1-cbiss. Gas sensors have been positioned around all the hazardous areas within the packaging cell, and cold yeast storage room and cabled back to a central MX43 control panel.