Hidden assets
11 Aug 2015
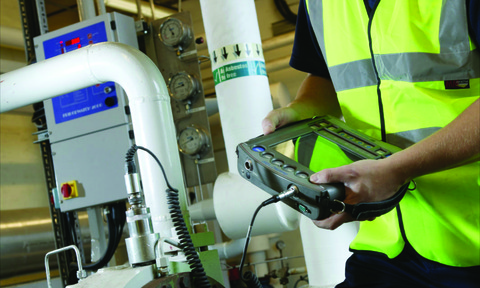
When it comes to protecting assets, monitoring those hard-to-reach places need not be a hit and miss affair.
Out-of-sight assets are no longer out of mind, thanks to a growing legion of sensors and cameras.
As environmental and safety restrictions increase, well-equipped maintenance crews can now monitor important plant assets such as pipelines and storage vessels around the clock.
While moving to condition monitoring using infrared may have an initial price tag, the savings over time are unquestionable if implemented correctly.
Stuart Holland, director of Thermographic Consultancy
Assets such as pipelines with a potentially hazardous payload can present particular challenges, says Andy Tonge, sales manager of Hima-Sella.
Used to transfer liquids and gases between locations far and wide, they must be protected along their entire length to prevent environmental damage and financial losses or fines that result from escaping product.
Hima-Sella offers solutions for pipelines and other critical plant equipment where operation at higher-than-normal pressures is not permitted. The risks faced by these pipelines include potential process or control issues, accidental damage or even acts of terrorism.
Most pipelines have valves along their length for the express purpose of being able to isolate sections, and it is here that local, automated safety protection is best implemented, says Tonge.
For this purpose, Hima-Sella has developed a High Integrity Pressure Protection System (HIPPS) solution that provides an autonomous layer of protection.
The technology, which can also be applied to low pressure or temperature parameters, is not monitoring the process, but tasked with looking after the pipeline end to end, which might stretch the length of entire continent.
“Our equipment supervises conditions in a pipeline so it if goes over a certain design pressure we can shut a valve and stop it from going to bursting point,” he says.
HIPPS is used mainly in oil and gas and it can handle hazardous substances in pipelines such as gas and petroleum, where venting or flaring is not an option.
“We have had applications where part of the pipe has a problem or needs to be maintained, so we shut individual points down on pipeline,” says Tonge.
“This acts like a canal, and allows you to drain off the exact area you need to.”
Thermal imaging tools born from infrared detection tools deployed by the military are also growing in popularity to support condition monitoring.
Stuart Holland, director of Thermographic Consultancy, says that as well as fluid pipework, thermal imaging equipment can also monitor motors, pumps, bearings, condensers, evaporators, valves and compressors.
The consultancy works in partnership with FLIR, distributing its thermal imaging equipment throughout the UK.
Holland adds that thermal imaging cameras are becoming increasingly powerful, at more affordable price points.
“Now the cost of owning a camera and learning how to use it correctly is also a realistic option for smaller companies,” he says.
FLIR has recently released the FLIR C2, a pocket-sized thermal imaging tool designed to boost on-the-spot troubleshooting capabilities for process industry maintenance teams.
“While moving to condition monitoring using infrared may have an initial price tag, the savings over time are unquestionable if implemented correctly,” says Holland.
“It is the rigorous regime of monitoring that allows any organisation to determine the wear rate and life expectancy of equipment,” he says.
“This in turn takes the guess work out of maintenance, avoids costly over maintaining of equipment and allows the risk of failure to be reduced to near zero.”
Monitoring the structural integrity of pipelines is another important requirement in many industries.
It is in this application that strain sensors are often deployed to measure mechanical loads on structures such as pipelines in the oil & gas industry, says Greg Todd, sales engineer at HBM.
“What we see more and more is our customers saying they’ve seen some anomalies on a pipeline, and want some kind of structural integrity monitoring for it,” he says.
HBM manufactures sensors and transducers used to detect the displacement or deformation that may cause equipment to fail.
“You can install our equipment on anything – on a pipeline or a piece of older plant equipment that a customer wants to run beyond its specified lifetime,” says Todd.
“We will instrument it up and add additional sensors such as strain gauge sensors to measure for structural fatigue.”
This is a popular option for plants looking to squeeze more life out of existing assets, he says. “We will analyse this and provide feedback to the customer on whether it is still serviceable or not. It could cost them initially, but they may then get an extra five years from their equipment,” he says.
The technology can also be used to extrapolate data for a wider range of equipment than that being measured, he adds.
AVT Reliability is another engineering firm specialising in condition-based maintenance, deploying techniques in vibration analysis, thermal imaging, oil analysis and ultrasound.
“Vibration induced fatigue of process piping systems is an important and fundamental failure mechanism,” says Neil Parkinson, a technical director at AVT Reliability.
Data published by the UK’s Health & Safety Executive (HSE) for the offshore industry has shown that in the UK sector of the North Sea, fatigue and vibration failures account for 21% of all hydrocarbon releases.
“Although overall statistics are not available for onshore facilities, available data for individual plants indicates that in Western Europe, between 10 and 15% of pipework failures are caused by vibration induced fatigue,” says Parkinson.
Accelerometers from AVT Reliability are in use at the Chirag-1 oil-drilling platform in the Caspian Sea, an area of high seismic activity, which is operated by an international consortium, headed by BP. The explosion proof system installed on the Chirag-1 uses high sensitivity servo accelerometers to collect data on a real time basis. These have been fitted to measure the motions of the rig in the x, y and z axes.
The data is downloaded every three months by Bomel, a structural analysis and risk assessment specialist.
“The information allows us to monitor the life cycle of the Chirag-1 and from this we can put together detailed inspection routines, appropriate to the changing conditions,” says Keith Ward of Bomel.
Tiptop condition
David Manning-Ohren, condition monitoring manager at Eriks, offers his tips on how to prevent costly condition monitoring mistakes.
Never use condition monitoring on its own
For monitoring to work best it needs to be implemented in harmony with a strong maintenance strategy and repair feedback from the maintenance team or outside suppliers.
Spend your money on the most valuable asset
Not everything needs to be monitored. The key to more uptime is assessing what is critical and then devising a schedule that takes into account its failure or repair history and cost to a business.
Get close to your key plant and machinery
The best condition monitoring device ever invented is man. Tap into the people who are using the machine every day and notice the rattles, smells, squeaks, drips, bumps that are out of the ordinary.
There is no ideal condition monitoring frequency
This depends on many variables from the maintenance regime, through to the quality and age of the equipment and its criticality, which can only be determined with a thorough understanding of the plant and its role in production.
Keep a vibration database
A good vibration database will include three types of vibration reading, trend, spectrum and time waveform. Vibration checks every 4-8 weeks is a good starting point.
Understand the operating conditions
Always walk around a site before taking any readings and switch on machinery to ensure that it is warmed up and fully operational. Base-lining with respect to speed and operating load is excellent practice.
Certification is better than qualification
If you are condition monitoring in-house you need to ensure that your key people are up-to-speed with the appropriate certificates, new technologies and practices.
Insist on seeing some paperwork
There are sound reasons for outsourcing, but do ask to see some paperwork. Engineers should be qualified to ISO 18436 and abide by the British Institute of Non-Destructive Testing (BINDT) code of ethics.
Judge on more than the day-rate
Condition monitoring is a specialist job but all-too-often price is the key determinant for users of plant and equipment. Consider the support that an organisation can offer; expertise on bearings, gearboxes, pumps and motors is essential.
Delay failure with good maintenance
Take common sense measures to delay the failure as long as possible by doing the obvious things like lubrication, dusting down cooling fans on motors, running a vacuum over the distribution board and cleaning oil from under the machine.