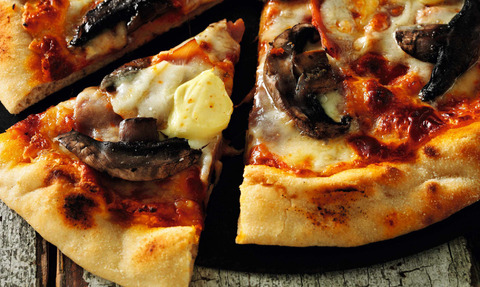
Food company Bakkavor Group takes a more proactive route to maintenance.
Bakkavor Group supplies over 5000 products across 18 different product categories including ready meals, pizzas, desserts, salads and soups.
It has 32 operations in the UK, from Edinburgh in Scotland to Dover in Kent, and its primary business is private label food for the larger grocery retailers across the country, including: Tesco, M&S, Waitrose and Sainsbury’s.
Since rolling out Agility across Bakkavor, and with help from SoftSols configuring the system, we have seen a definite improvement in system utilisation and recorded jobs
Bakkavor’s Gary Smyth
In 1997 Bakkavor first implemented Impact XP, a CMMS (computerised maintenance management system) solution provided by SoftSols Group, which was rolled out across many sites over a 10-year period. In 2007 Bakkavor began an extensive search for the best next generation CMMS solution from all major system providers.
Bakkavor required a system that could efficiently manage its reactive and proactive maintenance schedules while allowing the engineering department to manage its own inventory and purchase orders.
The system also needed to interface with Bakkavor’s core Enterprise Resource Planning (ERP) systems, Protean and Great Plains.
The chosen solution was Agility, the next generation maintenance management molution from SoftSols.
The first site to adopt Agility was the Cucina Sano operation in Lincolnshire, which began implementation in 2010, and allowed the business to review its current data and processes and dedicate time and resources to improving these.
It also gave Cucina Sano the opportunity to ensure each of its assets was identified and included in Agility.
Since implementation, the company says Agility has enabled all reactive and proactive maintenance activity to be managed together in a single system, also giving visibility of historical data allowing job trends to be monitored.
Engineering inventory and purchase orders are also being managed through Agility and Agility Mobile Stores.
Since 2010, Agility has been implemented in 13 Bakkavor sites with each one having the opportunity to review its processes and assets and make improvements.
Using Agility across multiple sites has given the business the significant benefit of a standard system, with reports and KPIs that can be generated and used by the engineers and each individual operation, says Gary Smyth, Business Analyst at Bakkavor.
“Through using Agility the engineers have embraced ownership of the data in Agility and each team has worked hard to improve the quality of data captured, benefitting the engineering teams and the whole business.”
The planned maintenance schedule generated in Agility has also enabled greater collaboration between the engineering and planning departments, ensuring the required equipment is available for planned maintenance. This results in less interruption for the production departments and increased uptime.
Through using Agility to manage inventory and purchase orders, stock values and levels are being constantly reviewed and optimised while ensuring that critical parts are available at all times using Min/Max levels, regular stock checks and running the system stock replenishment functions.
Using Agility Mobile Stores, the engineering team complete stock transactions in real time ensuring immediate and accurate visibility of stock levels, says Smyth. Across the current sites approximately 2,300 work orders are now generated per week and Bakkavor has seen a significant improvement on its reactive versus planned maintenance from 80/20 to a 50/50 split, he adds.
“Since rolling out Agility across Bakkavor, and with help from SoftSols configuring the system, we have seen a definite improvement in system utilisation, recorded jobs (both reactive and proactive), and been able to successfully interrogate repetitive maintenance. Based on this, we are now seeing an increase in product throughout within the manufacturing environment.”
Next steps
Agility will continue to be rolled out across Bakkavor sites and by the end of 2015 Agility will be used on 20 sites with over 500 users. Smyth says Agility will continue to be used to improve the reactive versus planned maintenance split and also be used with other production systems. Smyth says Agility can also be used with other plant production systems.