On the level
17 Nov 2015
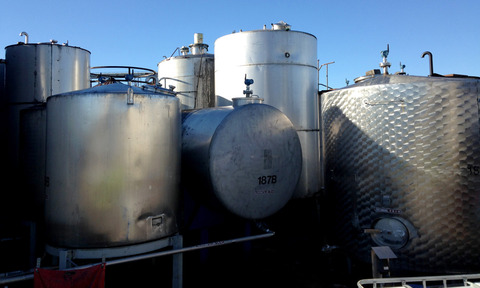
Level measurement can offer a line of defence against industrial spills, and regulators are taking note.
Plant operators must have ‘eyes’ everywhere when it comes to monitoring the level of liquids and solids used within their processes.
While oil spills at sea often dominate the headlines, smaller-scale chemical discharges can also be very toxic and damaging to the environment.
Regulators are coming down quite hard on companies in regard to monitoring content in tanks as well as making sure these things don’t spill
Pulsar Process Measurement’s Alistair MacKinnon
With the threat of fines and even imprisonment, regulators are cracking down on process breaches such as spills and discharges which can find their way into waterways or groundwater.
Last year Essex-based company Industrial Chemicals Limited (ICL) was fined £50,000 after four of its chemical storage tanks failed and spilled 150 tonnes of hazardous material.
Although nobody was harmed in the incident, the firm was prosecuted by the Health and Safety Executive (HSE) after an investigation found it failed to manage, inspect and maintain the tanks in question.
Level measurement instruments can form a strong layer of defence against industrial spills.
For this reason, regulators are making them mandatory in many instances, says Alistair MacKinnon, director of sales and marketing at Pulsar Process Measurement.
“A lot of pressure is being put on by the Environmental Agency in the UK and the Scottish Environment Protection Agency (SEPA),” he says.
“They are coming down quite hard on companies in regard to monitoring content in tanks as well as making sure these things don’t spill. This means many companies are having to monitor the contents of tanks, whether they are running a chemical or water process.”
Unfortunately these measures require funds that many companies haven’t planned for in their budget, MacKinnon says.
Pulsar mainly supplies the water, wastewater and food and beverage industries with non-contacting and non-invasive ultrasonic instruments.
“We can help to soften the blow for them by developing technology that aims to reduce overall expenditure,” says MacKinnon.
The company has developed a range of intelligent transducers for event monitoring, that can be used in tanks to measure various mediums, and can also be hooked into a distributed control system (DCS) where they can be monitored and measured centrally.
These were designed to be low maintenance, and provide a level of inbuilt intelligence.
“So if there is some form of false echo, it can adapt and ignore it, and then the user has years of maintenance-free monitoring,” he says. But you can’t throw ultrasonics at everything, warns MacKinnon.
“It is adequate for the majority of applications but where you have vapours, high pressure or temperature, then radar is the way to go. This is something we’ve also been exploring.”
An event that highlights the importance of effective level measurement is Buncefield, says Andreas Hessel, marketing manager at Emerson Process Management.
Emerson supplies a broad portfolio of instruments, with a core customer base in hazardous industries such as chemicals, and onshore, offshore and downstream oil and gas.
“These days there are some really good methods for safe overfill, but it is difficult for many customers to take these from theory into practical life,” says Hessel.
“Emerson knows how to do reliable level measurement and how to do it safely, so we can bring our competence and supply these companies with certified products,” he says.
“The common denominator is that we supply technologies that are very reliable in their performance and need no calibration,” he says.
“They don’t have moving parts, so they don’t have to be fine tuned. Set them once and they are pretty much good to go.”
We are noticing a big change to wireless and because ultrasonic is electronically-based, it is easy to adapt and put into a process system
Morgan Advanced Materials’ Charlie Dowling
He says experienced labour is also becoming an “endangered species” with the new smartphone generation often bringing with it an entirely different approach to technology.
“They want quick and simple access and are ready to reap all the benefits from a smart transmitter. We have invested a lot in developing a human centric design within our products to suit them,” he says.
“Now many of our transmitters have the capacity to provide diagnostics to tell operators ahead of time whether the sensor parts of a switch or radar are compromised.
“Then if there is product build-up or corrosion, it gives them that information ahead of time to plan some maintenance, which makes a huge difference because unplanned downtime is the last thing our users want to experience.”
Hessel says he has also witnessed a nascent interest in wireless products, growing out of more stringent regulations on safety.
“Operators have had to get by with manual measurements that are taken now and then, but now many need something automated to alert them when overfill occurs,” says Hessel.
“Running wires is undesirable because in the short term it requires a lot of investment in infrastructure, so if they can do something at a fraction of cost there is a huge interest.”
Hessel expects interest in wireless to grow as companies become more familiar with it. “What is required is a leap of faith, but they often quickly realise it wasn’t so different at all.”
For example, Hessel recently saw a level measurement installation with four storage tanks that would normally have taken a whole week, but with wireless was done and commissioned in seven hours.
Morgan Advanced Materials is another company witnessing a move towards wireless instruments.
“We are noticing a big shift to wireless, and because ultrasonic is electronically-based it is easy to adapt and put into a process system,” says Charlie Dowling, sales and marketing manager for Morgan Advanced Materials.
The company specialises in ultrasonic level instruments, for the oil and gas industries, as well as general process control such as silos of grain, syrup or water.
“Basically anything that ultrasound can bounce off, you can measure,” says Dowling.
However, investment in this technology is often highly dependent on the price of the material being measured.
Morgan Advanced Materials develops materials with tolerance to aggressive mechanical environments, heat or chemical attack.
“For water applications you would use a low cost device, but with oil and gas, the investment is larger, and the solution is very often customised,” Dowling says.
“Some materials are high-temperature resistant … but incorporating them into electric sensors is difficult.”
Nevertheless, investment in customised instruments can pay off in the long run, because they can operate on lower voltages and with lower risk of an explosion, he says.
Level sensors
Simon Dear of Cynergy3 Components provides an overview of five common level sensing technologies.
Float switches: A cost effective and reliable mechanical technology for liquid level sensing. They are best suited to relatively small tanks or chambers and suit most fluids, chemicals, temperatures and pressures.
Optical level switches: These are solid-state devices used for point level sensing of liquids or suspended solids. These switches can be used with aqueous, organic or corrosive liquids.
Cable-suspended switches: Relatively simple, cost effective mechanical devices, these switches are typically installed in large tanks or containers, as well as in natural open spaces such as reservoirs.
Cable-suspended pressure/depth sensors: These are submersible or externally mounted pressure sensors suitable for measuring the level or depth of liquids in large/deep tanks or water in reservoirs. Chemically compatible materials are important to ensure high performance.
Fixed pressure/depth sensors: Permanently mounted to the side wall or base of small or large tanks, these solid-state, analogue output devices provide continuous depth/level measurement and are impervious to surface movements and agitation.