Soft assets: energy management
1 Dec 2015
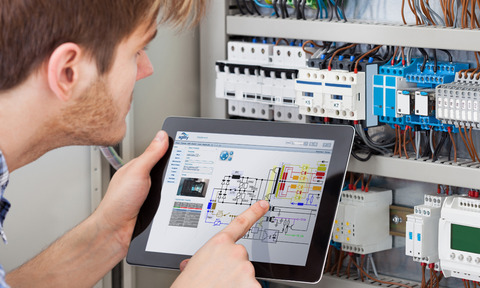
Squeezing more efficiency from plant equipment is the next frontier for CMMS.
The process sector is littered with high-energy-use items of equipment such as motors and drives, refrigerators, lighting and air compressors.
But with energy prices gobbling up ever larger slices of budget, the race is now on to weed out rogue equipment and trim processes.
You can schedule some maintenance at a cheaper period because some manufacturers have different electricity or water usage fees at different times of day
Idhammar Systems’ John Roberts
The Carbon Trust says that while best practice for industrial energy efficiency is relatively well understood, most companies still focus their efforts in non-process related areas, such as space heating and lighting.
“Many also deploy sound practices in process efficiency [such as] steam distribution and compressed air.
“However, we found very few have the internal systems to identify and deploy genuine innovations in processes such as heat recovery, combustion efficiency and novel cleaning methods,” says the Carbon Trust.
Because the manufacturing industry accounts for nearly a third of the world’s total energy consumption, regulators are also cracking down.
The Government is poised to introduce the Energy Savings Opportunity Scheme (ESOS) in December which will demand independent energy auditing of large companies.
Improving operational efficiency of plant equipment can make a significant contribution to reducing energy consumption, says John Roberts, managing director of Idhammar Systems.
Many manufacturers have already introduced a wide-range of energy-related programmes including switch-off campaigns, intelligent production scheduling at a lower time-tariff, installing new energy-efficient equipment or enhancing maintenance to reduce energy leakages.
“You can schedule some maintenance at a cheaper period because some manufacturers have different electricity or water usage fees at different times of day,” says Roberts.
However, while a lot of people in the energy measurement business can tell them what they are using on a minute-to-minute basis, they can’t show how individual assets are performing, says Roberts.
Idhammar’s Overall Equipment Effectiveness (OEE) software was developed to help users discover any hidden losses, justify improvements and monitor their impact on the bottom line.
Users can monitor electricity, gas or water consumption, or any meterable resource consumption minute-by-minute in line with production output.
“If they have downtime events or breaks in production, they can see how energy consumption goes down correspondingly.
Wasted compressed air causes manufacturing companies to incur high energy bills, costly repairs and substantial downtime
Brammer’s Iain Hanson
“We can then point the manufacturer in the direction of making savings by deactivating equipment when production stops,” Roberts says.
Softsols has also increased its focus on energy management, with its Agility software acting as the hub.
“A big part of what we are doing with Agility is improving the visibility of information by hooking into other systems in the plant,” says SoftSols group managing director David Hipkin.
This might involve connecting with building management systems or bringing in readings from meters and intelligent devices, he says.
“There is an increasing focus on intelligent devices and the Internet of Things is very much a big part of what we’re looking at.”
It can also connect to energy monitoring devices attached to key items of equipment that allow operators to determine whether there is an abnormal drain on energy.
“The big critical items have been monitored for a long time, but this is rippling down through next level,” says Hipkin.
“The number of connected devices out there is spiralling all the time and the technology is becoming more and more affordable, and hence commercially viable.
“This allows the CMMS (computerised maintenance management system) to become a hub to give engineers the data from all these disparate devices, which is enterprise asset management in its widest sense.”
Sam Sweetman, a maintenance consultant at Real Asset Management, says energy management is an important factor within asset intensive industries.
CMMS can help operators schedule planned rather than reactive strategies. “The more planned maintenance you do, the more efficient any asset is going to be and the less likely to break down,” he says.
Another important approach is to replace inefficient equipment with higher efficiency models.
If you want to drive down energy consumption you need to identify the worst offender assets, and replace these with higher-efficiency models.
“Often the older an asset is, the more energy it will consume, so another approach is to look at a replacement programme behind the asset base,” he says.
That means looking at each asset, taking readings on the amount of time it is working compared with time sitting and using energy when it is doing nothing.
Iain Hanson of Brammer, a supplier of maintenance, repair and overhaul (MRO) products and services, says he has seen well-managed, proactive maintenance play a significant role in reducing energy consumption.
Factors such as the correct design, specification and maintenance of drives and compressed air systems, can all help manufacturers meet industry standards as well as impacting positively on profitability.
“Compressed air systems continue to play a vital role in a wide range of manufacturing processes, from cooling and drying to the removal of scrap product, contamination and vacuum generation,” he says.
The most common areas compressed air is wasted are through air leaks, poor maintenance, misapplication and poor control, and these can result in “high energy bills, costly repairs and substantial downtime,” Hanson says.
Switch and save
- A compressor installation that is switched on when there is no demand will consume 20-70% of its full load power. Automating the switch-off process will help reduce energy consumption.
- Compressed air leaking through a single 3mm hole could cost you nearly £700 per year in energy costs. Fixing the hole to result in a 1 bar reduction could save about 7% of the energy required for compression.
- Running old motors at full speed could be as effective as reducing the motor’s speed by 20%. Fitting a variable speed drive could reduce a motor’s energy consumption by as much as 50%.
- A faulty door seal could increase a refrigeration unit’s power consumption by as much as 11%. Replace the seal and implement inspection checks, as dirty refrigeration condensers can increase costs by around 26%.