Clean screens
6 Jan 2016 by Louisa Hearn
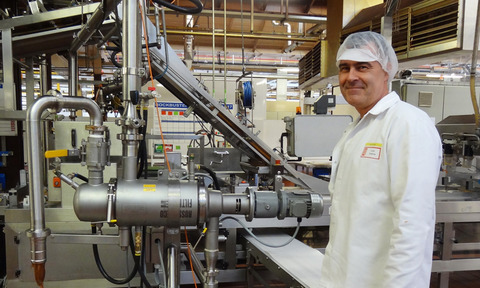
Self-cleaning filters are making steady inroads into production processes, writes Louisa Hearn.
When a filter fails, important processes can be disrupted and valuable products wasted.
This makes filtration a critical piece of the puzzle when managing complex industrial requirements.
"We required a machine which could filter a high viscosity paste, at a high temperature"
Glasgow-based pipe manufacturer Vallourec designs and manufactures products for the offshore oil and gas industry, including the steel pipes used as drill collars.
Due to the tight tolerances required offshore, the quality of the pipes it supplies to these industries must be 100%.
However, the company found its quality testing procedure was being disrupted by water contamination that was affecting its ultrasound readings.
To remove the contamination, the company installed a Double Automag AM6 magnetic filter from filtration supplier, Eclipse Magnetics.
“It’s solved all the problems we were having previously with downtime and maintenance costs,” said Kenneth McRae, Vallourec’s principle engineer.
“The filter means that we are able to use recycled water, which is saving us £1000 per week.”
Mondelēz International also recently added a filtration solution to optimise production of one of its biscuit brands.
Its Belgian factory, which produces brands such as Pims, Prince, TUC and Cha-Cha, was experiencing product wastage.
When the wafer was covered with caramel, the wafer crumbs were getting into the excess caramel, making it non-reusable.
“We sought a solution to recover the wasted caramel in order to reduce the product loss and improve the production process,” says Alex Pardon, continuous improvement facilitator at Mondelēz International.
“We required a machine which could filter a high viscosity paste, at a high temperature in order to keep the caramel in liquid form for it to be reclaimed for reuse.”
Russell Finex offered to test its self-cleaning Russell Eco Filter at the Mondelēz site.
It said that during testing, the filter was able to keeping the high viscose caramel in a liquid state by filtering at a temperature of 35°C.
When a taste test found no difference in quality between a bar with or without the reclaimed caramel, Mondelēz installed a Self-Cleaning Russell Eco Filter, which it says cut product loss by 20% and improved the waste disposal process.
Filtration supplier BHS Sonthofen is also developing self-cleaning technology.
The company has expertise in mechanical solid-liquid separation, especially in the fields of chemicals, pharmaceuticals, food and minerals, and has recently expanded into gas processing and offshore plants.
"The clean up and environmental cost of all chemicals is substantial, so new filtration membrane technology is always being investigated"
According to Tim Ochel, project manager for filtration technology at BHS Sonthofen, management and disposal of consumables such as filter cartridges, and filter cake are key challenges for operators in the gas industry.
To aid this process, the company has been working on new self-cleaning filtration processes for the purification of monoethylene glycol (MEG).
MEG is commonly added as a corrosion and hydrate inhibitor for the transport of Natural Gas in pipelines.
Most systems used to recover this tend not to be self-cleaning and are difficult to dispose of.
As an alternative to the existing systems, Ochel says BHS-Sonthofen has combined a pressure plate filter and a candle filter, which improves MEG recovery and can reduce operating and maintenance costs.
“By washing the filter cake, the MEG-loss is lower by a factor up to 30 than what can be achieved with previously known methods using pre-coating or other technologies,” he says.
“The washed filter cake can then be disposed as a nonhazardous waste.”
Material world
Advanced materials and techniques are providing the platform for new and potentially disruptive filtering technologies.
Ceramics
Specifiers of filters for process water applications have until recently been limited to filters made of metals or polymeric materials, says Klaus Prosiegel of Morgan Advanced Materials.
“However, to date, few of these materials have been found to offer the desired performance attributes in the three key areas of mechanical resistance, chemical resistance and flux properties,” he says.
This has driven the filter manufacturers to seek alternative materials that provide all three of these properties, without compromising on their effectiveness.
Two materials have come to the fore in recent years, both of which are ceramics, says Prosiegel.
Alumina (Al2O3) enables the creation of extremely fine pore sizes, vital when purity is at a premium.
Silicon carbide, on the other hand, delivers exceptional performance in terms of resistance to both abrasion and corrosion.
Graphene
Another material that shows great promise when applied to filtration equipment is a self-cleaning graphene enhanced coating.
Haydale is a materials specialist working on enhanced graphene and nanoparticulate materials.
It has recently been awarded a number of research grants to fund projects such as the development of low cost, self-cleaning graphene enhanced coatings for industrial membranes used in the cleaning and filtering of wastewater, desalination and offshore drilling fluids.
“I think everyone is looking at this because water is a scarce commodity,” says Ray Gibbs, chief executive of Haydale.
“The clean up and environmental cost of all chemicals is substantial, so new filtration membrane technology is always being investigated.”
Additive manufacturing
Additive manufacturing or 3D printing, is allowing some manufacturers to offer more customised filtration solutions.
UK manufacturer Croft is deploying a process called Metal Additive Manufacturing, which places metal powder on a bed and then uses a computer controlled laser to melt and fuse the metal at the required points.
On completion of the process, the excess powder is removed and recycled leaving the solid metal in the required form.
The company says the key advantage of additive manufacturing is the ability to enhance the design of a part in ways previously not thought possible.
It is also possible to graduate metal thicknesses to give strength only where it is required, produce internal features and intimately produce assemblies or finished products in a single production cycle.
Readers' Comments
There are no comments on this article, leave a comment below to have your say
Have Your Say
The comments have closed for this article