The ebb of flow computers
29 Mar 2016
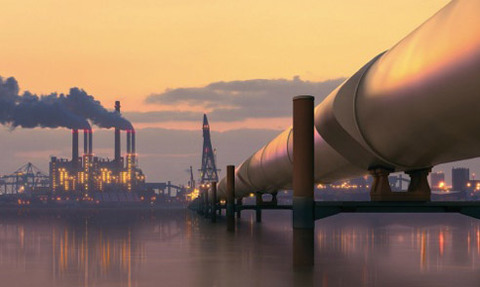
Does the growing trend of metering devices capable of monitoring multiple variables spell the end for conventional flow computers? John McKenna reports.
When it comes to measuring how fluids and gases move through process facilities, plant operators can choose from a plethora of devices.
These devices can monitor basic variables such as temperature and pressure through to more advanced analysis of viscosity and gas composition. Most are also wireless and can send their data direct to a plant’s control system, where an overall picture of flow rates and variables can be calculated.
Traditionally, to make sense of the information offered by flow meters and other sensors, their outputs have been plugged into a separate flow computer.
Flow computers are stand-alone electronic devices that take the analogue and digital signals received from flow meters, temperature, pressure and density transmitters, and calculate the flow of fluid and gases through a process plant.
They calculate the exact amount of flow and record the data, important events, and alarms. Then, that data is transferred to external computers or workstations for inspecting, managing, and accounting.
Flow computers calculate the exact amount of flow and record the data, important events, and alarms. Then, that data is transferred to external computers or workstations for inspecting, managing, and accounting
They are most commonly found in sectors where the fluid or gas being transferred is high value. Consequently, by far the largest sector for flow computer manufacturers is the oil & gas market.
In the oil & gas sector, flow computers are used for different functions such as liquid & gas measurement, wellhead measurement and optimisation, custody transfer and control, fuel monitoring, fiscal flow metering, flow meter proving, pipeline transmission and distribution, supplies loading, and in other billing and calculation functions (see box below).
Even in the current climate of cripplingly low oil prices, research by Markets and Markets predicts that the global oil & gas flow computer market is predicted to grow at a compound average growth rate of 5.5% every year up to 2020, when it is expected to be valued at US$1.04 billion (£743m).
Tech threat
However, despite this apparent buoyancy of the flow computer market – at least as far as oil & gas is concerned – there are clouds on the horizon. Specifically, flow computers face a very real threat in many sectors of becoming, if not already, surplus to requirements.
This is because many of the sensors used in a process facility can now monitor multiple variables and carry out some of the calculations that were once the sole domain of the flow computer.
“There are many different types of instrumentation where historically you had to buy a flow meter and a flow computer, but you can now carry on the calculations within the device,” says ABB pressure and process flow product manager David Bowers.
For example, says Bowers, ABB’s vortex flowmeter, the VortexMaster FSV450, is described by the company as having “advanced flow computer functionality”. It can receive signals from remote sensors like pressure, temperature, density or gas content and compute them directly with the signals from the internal flow and temperature that the flowmeter is measuring.
Likewise, Magnetrol global product manager Tom Kemme says some of his company’s thermal mass flow meters are now so sophisticated that they could be considered to be flow computers.
“In many of our markets, flow computers are not being utilised so much,” adds Bowers.
“To be honest, the reason why they are not being utilised so much is that a lot of instrumentation is negating the use of flow computers.”
Cash counters
The key market resisting this trend away from flow computers is oil & gas, and this is driven by rules surrounding custody transfer (see box below).
Where you have a flow of oil or gas, for instance, there is a tax on that, says Bowers.
“Custody transfer, fiscal measurements – this is all about taxation. Oil and gas will always have a stand-alone flow computer as long as the rules for custody transfer dictate that,” he says.
Flow computers used for custody transfer calculations need to be able to provide calculations to the accuracy and resolution required to meet the approvals laid down by the relevant metering authorities throughout the world, says Emerson Process Management Flow Solutions sales manager (North & South Europe) Andrew Crowther.
There are many different types of instrumentation where historically you had to buy a flow meter and a flow computer, but you can now carry on the calculations within the device
David Bowers, ABB pressure and process flow product manager
Specifically, custody transfer and fiscal metering applications require 64-bit calculations to meet the low levels of uncertainty required by regulators, while many control systems only operate to 32-bit – meaning that such systems are as yet unable to replace flow computers in taking the signals from sensors and calculating flow to the required accuracy for custody transfer, Crowther says.
Virtual flow computers
However, while flow computers look unlikely to be ousted from custody transfer applications by instrumentation connecting directly to control systems, there is the potential for their current stand-alone hardware form.
In 2014 ABB acquired a company called Spirit IT that has developed a concept that it calls Virtual Flow Computing (VFC). The term ‘Virtual’ refers to the fact that no flow computer hardware is used.
Instead, the software component of a flow computer is reused on a standard PC. Instead of providing physical connectivity to field signals as provided by conventional flow computers, measurement values for the VFC are acquired by data communication devices such as a PLC, or data historian, or IO interfacing hardware. So far Virtual Flow Computing systems are mostly being used as an online verification and back-up for conventional flow computer.
However, Virtual Flow Computing systems have been approved and successfully used for custody transfer in countries including the UK and Norway. With rapidly improving communication technologies and networks – 5G was being discussed at February’s Mobile World Congress in Barcelona as an enabler of the ‘Internet of Things’ – who would bet against flow computers being reduced to the software that is able to connect intelligently with remote wireless devices?
What is custody transfer? And why do you need a flow computer?
In oil & gas, custody transfer simply refers to the transfer of ownership of a liquid or gas from one party to another: so, for example, the transfer of oil from the upstream producer to the downstream process plant, or the onward sale of petrol or diesel by the refinery on to the retailer.
The need for an extremely high level of accuracy in measuring how much oil or gas is being passed between parties is clear, as the level of measurement determines the level of revenue a producer or producer receives.
A high level of accuracy is also required for fiscal flow metering – in other words, calculating how much tax needs to be paid on what is flowing through the pipeline
In addition to this commercial imperative, a high level of accuracy is also required for fiscal flow metering – in other words, calculating how much tax needs to be paid on what is flowing through the pipeline. This need for accurate metering applies not only to oil & gas, but also to the food & beverage sector when calculating the duty on alcohol.
Indeed, the terms custody transfer and fiscal metering are often used interchangeably. What both terms point to is a situation where payment is made as a function of the amount of fluid or gas transferred, so accuracy is paramount: even a small error in measurement can quickly add up to huge losses or incorrect payment of tax.
Expensive errors
Because errors in measurement for custody transfer can be so expensive, custody transfer and fiscal metering are regulated in most countries, and alongside government regulations there are also standards set by industry associations such as the American Gas Association (AGA) and American Petroleum Institute (API), the Physikalisch-Technische Bundesanstalt (PTB) in Germany, and the gosudarstvennyy standart (GOST) in Russia.
In the UK, the Department of Energy and Climate Change (DECC) has set the allowance for uncertainty in measuring gas at plus or minus 1%, while for liquid the tolerance for uncertainty is just 0.25%.
A single flow meter is unable to record all of the variables necessary to reach such low levels of uncertainty. Other components that are required to reduce uncertainty include:
• A meter prover
• Density measurement instruments
• Sampling systems
• Composition measurement for gas
• Temperature measurement
• Pressure measurement
• Flow conditioning
Presently only flow computers can take all of these inputs, record and log them, and then calculate the highly accurate flow rate required by regulators.