Process safety: smart enclosures
4 Apr 2016 by Rob Smith
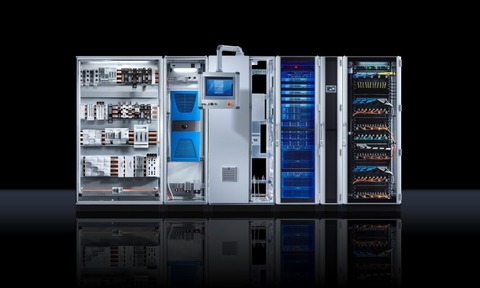
Materials specification and innovative design are modernising the enclosures market, writes Robert Smith.
Industrial enclosures are installed throughout many of the process industries, but this important piece of kit rarely grabs the headlines.
Though they are frequently over-shadowed by the bigger-ticket items, enclosures play a vital role – even in the harshest environments.
Philip Glenister, industrial manager of infrastructure at enclosures provider Rittal, says enclosures with access are designed for protection and to keep critical processes running.
“Essentially, enclosures protect equipment from external sources and they protect the external sources from the equipment within the enclosure as well,” Glenister says.
“It’s a two-way street and that remains true regardless of location.”
Typically, says Glenister, you would find an enclosure within a manufacturing facility or inside a clean environment, but they can also be installed in the desert or the Arctic Circle.
Materials and design are integral in ensuring the right bit of kit is specified for each individual application
Clearly, there is no ‘one-size-fits-all’ type of enclosure, so materials and design are integral in ensuring the right bit of kit is specified for each individual application.
Glenister says there are a number of different materials used for enclosures and the selection process is largely dependent on the final location.
“Pharmaceutical manufacturers, for instance, would generally install a stainless steel enclosure, and it would be specifically designed to make it easy to clean and to stop it harbouring dirt and bacteria,” Glenister says.
They would also typically be looking to install an enclosure with an IP69K Ingress Protection (IP) rating. Glenister says installations in pharmaceutical facilities have to be very particular, which is why they require a higher IP rating.
Kitted out
Martin Hess, chief executive officer of Intertec, which designs enclosures for outdoor process applications in particular, says there is a trend towards the specification of advanced materials.
He says these materials are designed to optimise resistance to long-term threats such as corrosion. They also provide superior insulation properties, he adds.
This is vital to stable and problem-free internal operating environments because “good insulation is critical to almost all outdoor protection applications”, he says.
“The basic glass reinforced polyester (GRP) sheet material used in Intertec’s enclosures has a very high thermal resistance compared to metal, with an efficiency that is around 10,000 times better.
“GRP sheets are also fabricated easily in composite ‘sandwich’ forms, enclosing high performance insulation.”
According to Hess, a holistic approach to enclosure design has particular benefits in avoiding the ‘cold-spots’ or ‘hot- spots’ that can lead to problems.
This approach delivers a stable operating environment for instrumentation, which can be crucial in many process control applications.
“Naturally, this construction technique also greatly reduces the energy required to heat – or cool – electronics equipment,” says Hess.
The major hazards that enclosures are designed to protect against are dust, fire and explosion, water damage and electrocution
While materials play a vital role in enclosures design, manufacturers must also consider safety.
The major hazards that enclosures are designed to protect against are dust, fire and explosion, water damage and electrocution.
Glenister says the IP rating is designed to protect against these types of hazards.
“Then you have the ATEX products that are providing an environment that stops explosive gases or dust from getting into an electrical component, which can cause a spark and explode from inside the enclosure.”
Hess, meanwhile, says there is increasing demand for products with fire resistance, which are designed to house critical resources within plants.
Flame resistant
“There is no global standard in the instrumentation industry for fire resistance, so currently Intertec is seeing requests from large users and processing companies asking for conformance to fire resistance classifications such as F60 or F120,” he says.
According to Hess, these specifications come from fire regulations designed to protect buildings. “Intertec has transferred this kind of specification to the outdoor enclosure world by producing special composite constructions,” he says.
“These can keep the control and instrumentation equipment inside an enclosure – such as an actuated shutdown valve – below 60°c for periods of up to two hours, even in the presence of a high temperature hydrocarbon fire.”
Industry is also demanding enclosures that are blast-proof, Hess adds.
He says high pressure waves can easily damage and break bent-metal or thermoplastic materials often used to build enclosures.
“One interesting attribute of enclosures constructed from GRP in this application is intrinsic flexibility. This allows the enclosure, cabinet or shelter to flex and absorb blast-wave forces.”
He adds that such GRP enclosures are typically fabricated using sandwich panels with GRP sheets enclosing an inner core, which are designed to provide insulation and further strength.
According to Hess, the manufacturing process does not rely on moulds, so the thickness of the inner layer can be varied to provide the strength required for particular applications.
Industry is also demanding enclosures that are blast-proof
Martin Hess, chief executive officer of Intertec
“This is not possible with solid plastic enclosures fabricated using injection moulding as they would require new moulds in order to vary the properties,” Hess says.
“Similarly, applications that must withstand seismic events can also be made easily using custom sandwich-style GRP construction to withstand the extreme loads.”
Special equipment design is also becoming a common requirement for outdoor enclosures.
“Common reasons [for special equipment design] include size, shape and weight optimisation because of the location, which might be an oil platform, or close to the process in a difficult location such as on top of piping, or on a process column,” Hess says.
Meanwhile, Fibox, which manufactures enclosures for demanding environments, has recently developed a range of glass reinforced electrical enclosures as an alternative to the sheet steel wall-mounted cabinets currently being installed in corrosive environments.
Designed specifically for the panel building market, the company’s ARCA enclosure has been developed to offer engineers a range that demands “superior performance and security in some of the most demanding environments”, says Fibox managing director Steve Gallon.
Readers' Comments
There are no comments on this article, leave a comment below to have your say
Have Your Say
The comments have closed for this article