Interview: Drax squares up to carbon-mitigation challenge
11 Apr 2016
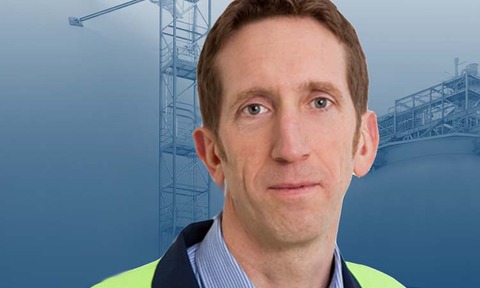
Pioneering new methods to reduce the nation’s carbon footprint is one of the most critical issues facing the power generation industry today. Jason Shipstone reveals how Drax has embraced the carbon-mitigation challenge.
When Drax began investigating methods for converting coal-fired power generation technology to renewable biomass, there was no well-trodden path for the company to follow.
But in the face of tremendous engineering challenges, it is slowly transforming itself from one of the region’s largest coal-fired plants into a predominantly biomass-fuelled generator.
“For over a decade we experimented with different types of biomass and a lot of R&D went into understanding the combustion process so that we could ensure we could maintain high reliability and efficiency,” says Jason Shipstone, engineering manager at Drax.
“Then, with support from the government, we were able to begin converting half the plant to efficiently burn biomass.”
Drax is slowly transforming itself from one of the region’s largest coal-fired plants into a predominantly biomass-fuelled generator
With two of the six Drax units now fully converted to biomass, and another close to completion, Shipstone says the company met with myriad engineering challenges at every step of its journey.
When you’re responsible for 8% of the UK’s electricity, the highest sustainability standards, availability and efficiency must be met, says Shipstone.
The company also had to conform to strict recording and reporting standards for agencies such as gas and electricity regulator, Ofgem.
“We had to do the conversion whilst the power station was live, so we simply couldn’t compromise on safety or availability,” he says.
Biomass has very different properties to coal, so one of the first technical obstacles to be addressed in the conversion of the plant was how to store the biomass.
Handle with care
“Biomass can’t be left on the ground or even out in the open,” says Shipstone. “It is far more combustible than coal so requires different storage and handling techniques. For example, if it becomes damp it becomes unusable as it can start to compost, so you have to keep it dry and in modified conditions.”
Another critical factor was the volume. This is due to coal having a higher density than biomass, which means a larger volume (around double) is needed to produce the same amount of energy as a unit of coal.
“When we started to do the numbers it became clear that the scale would be immense,” says Shipstone.
The breakthrough solution was to construct giant, 50m high domes – four in total – that can hold up to 112,000 cubic metres of biomass.
“They’re actually taller than the Royal Albert Hall and are secured to a concrete ring in the ground, with 370 Vibrafloor panels covering the W-shaped floor,” says Shipstone.
The atmosphere inside the domes has been specially modified to prevent the biomass from self-heating.
Done and dusted
Dealing with dust generated by biomass required another highly tailored solution, he said.
“We use a specially developed conveyor system which is fully covered, operates under a slight vacuum and features a dust extraction system at every transfer point,” he says.
“All extracted dust is transported via a pneumatic system and collected and stored centrally, then weighed and sampled before being recombined with the pellets just prior to combustion.”
Along with the dust, came inevitable safety challenges.
To store the biomass safely, the atmosphere in the domes had to be modified, says Shipstone. This is because biomass is still chemically active and the more you pile it up, the more it wants to compost.
“In order to control this self-heating we had to create an inert atmosphere in the dome,” he says.
“We worked with Air Products and looked at modelling the distribution of nitrogen, which had never been done before on biomass. The atmosphere is now managed to almost 100% nitrogen and using on-line sensors we can be sure the gas is evenly distributed around the pellet voids.
“A series of temperature sensing arrays allow us to detect any temperature changes and modify the nitrogen injection regime to stabilise an area if needed.”
Biomass also burns very differently to coal, which presents a significantly increased fire risk – and it’s 100 times easier to ignite than coal.
Biomass is quite a dusty fuel and hence highly flammable, so we needed to change the mind-set of the operators to treat it such, and adopt a zero-tolerance approach to fugitive dust
Jason Shipstone, engineering manager at Drax
“In order to transport the biomass safely into the boiler house, we again had to come up with an innovative solution,” says Shipstone.
“Biomass is quite a dusty fuel and hence highly flammable, so we needed to change the mind-set of the operators to treat it such, and adopt a zero-tolerance approach to fugitive dust.
“We minimised the amount of biomass we stored in the boiler house by fitting smaller ‘day silos’ outside, then working with a specialist supplier we develop a pneumatic system for moving the biomass pellets and dust from these day silos to the mills instead of using a conveyer belt like elsewhere on site. The pellets are blown through pipes at up to 50 tonnes an hour and propelled by air at around 1bar pressure.”
It wasn’t only the plant infrastructure that needed a rethink, adds Shipstone.
“There was a lot of redesign work involved across the entire supply chain, way back to sourcing the wood pellets. Sustainability is absolutely paramount when it comes to sourcing and managing our fuel, and the entire supply chain has been independently audited to ensure we are being as efficient, sustainable and environmentally-friendly as possible.
“The result is that we’ve achieved a carbon saving of 86% across the whole supply chain when compared to coal.”
On the right track
In the UK, specially designed freight trains were produced to transport the biomass from one of Drax’s four UK ports to the power station.
Shipstone says there’s an added time pressure when it comes to importing and delivering biomass so Drax had to upgrade some facilities to unload the biomass as quickly as possible.
“For example, new rail tracks and signal equipment were put in place so arriving biomass trains could run at 15mph, instead of the previous 5mph limit.
“In fact, we can now turn a delivery around in just 90 minutes.”
Shipstone says the company is now ready to convert a fourth unit, and is seeking support from the government. “We’re learned a huge amount since starting the conversion to biomass,” he says. “It was a £700m project to convert the original three units and develop the supply chains – but we believe it will cost less next time around because a large chunk of the original costs were in developing the most efficient and sustainable design.”
Biography – Jason Shipstone
JOB TITLE:
Engineering Manager – Strategic Project Engineering, Drax.
EDUCATION:
2003 – B.Eng Electrical/Electronic Engineering, Leeds Beckett University.
CAREER:
1987 – Becomes Electrical Craft Apprentice at CEGB/ National Power.
1991 – Joins Drax FGD Commissioning Team at Nation Power PDAC, working as part of the team responsible for the safe and timely construction and commissioning of the Drax FGD plant.
1995 – FGD Process Technician, Nation Power – responsible for plant improvements and process optimisation.
1998 – Operation Technician, National Power/AES Drax Power 2000 Shift Manager, Drax.
2005 – Materials Handling Manager, Drax.
2008 – Generation Manager, Drax.
2009 – Named Engineering Manager of Strategic Project Engineering at Drax, working closely with the Business Development and Strategy team to develop new growth opportunities.
Also responsible for overseeing the transition of Drax’s biomass conversion project to the operational teams.