Case study: tighter water management boosts Kraft Heinz
3 May 2016
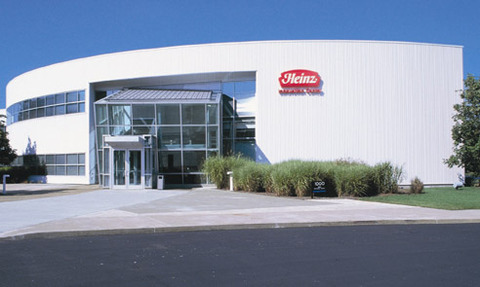
Advanced water technologies boost sustainability and cut costs at Italian Kraft Heinz food plant.
As one of the world’s leading manufacturers of food products, Kraft Heinz operates in over 200 countries in the world.
With the aim of protecting the planet from environmental risks, Kraft Heinz has made a commitment to the sustainable development of production processes and other operations.
This includes the creation of eco-friendly packaging and the goal to reduce greenhouse gas emissions by 20% by 2015.
Additional sustainability goals are in place to reduce environmental impacts across all manufacturing operations, including a large manufacturing plant in Latina, Italy.
The Latina plant produces a range of food products for its businesses, which include baby foods, biscuits, and fruit juices.
With the aim of protecting the planet from environmental risks, Kraft Heinz has made a commitment to the sustainable development of production processes and other operations
Following a call for tender at Kraft Heinz, a team of specialist Nalco Water staff conducted a mechanical, operational, chemical and sustainability assessment to identify opportunities to improve the sustainability performance of plant operations, and in particular the reduction of water use and effluent.
The system includes the boiler systems, cooling towers, reverse osmosis (RO) system and sterilisers and a pasteuriser.
A competitor had treated the plant for many years by considering each part of the system performance separately.
As a result, the water system was not under full treatment control, and could not maintain the necessary water quality across the entire system. This led to the need for frequent cleaning of the heat exchangers and of the sterilisers.
In addition, the water parameters on site were not ranged to specification, which caused frequent episodes of corrosion, leading to the replacement of asset parts.
Liquid assets
Nalco Water made a comprehensive proposal to renovate the entire system. This included installation of its 3D Trasar system on cooling towers, four 3D Trasar systems to each of the sterilisers and one on the RO system, plus Nalco Water’s System Assurance Centre.
The 3D Trasar water management programme was developed to deliver on-demand control and optimisation of cooling water chemistry and microbiology, protecting the system from corrosion, scale formation, and microbial infection.
Nalco Water’s System Assurance Centre also offered continuous oversight of the system, assistance in immediate alarm response, and problem identification with the goal of extending asset life and enhancing plant safety.
The proposed system was implemented by the Nalco Water team with 3D Trasar units installed on towers, boiler, and sterilisers.
According to Nalco, system efficiency has improved, and corrosion, scale, and microbiological fouling have been reduced.
Towering achievement
The towers had needed to be cleaned at least every 40 days due to the low quality of recirculated water, with two people needed to conduct the necessary maintenance.
Since the implementation of the new programme, no cleaning has been necessary, Nalco says. In addition, no breakdown or unexpected system maintenance has been required.
A survey made by the towers producer highlighted a perfect operating performance, with scale and fouling control maximising energy efficiency and minimising CO2 emissions.
A survey made by the towers producer highlighted a perfect operating performance, with scale and fouling control maximising energy efficiency and minimising CO2 emissions
The savings in water use, energy consumption, improved staff safety, asset protection and overall cost reduction, have all contributed to improved sustainability performance, Nalco says.
The company has continued to work with Kraft Heinz seeking further opportunities to improve performance and cost efficiency. Nalco Water is now also treating a new boiler and an aseptic cooling tower for the new vacuum-packing line for the manufacturer.